Brazing is a viable method for joining cast iron, particularly when the goal is to preserve the base metal's properties and minimize the risk of cracking. The process involves using a filler metal that melts above 840 °F (450 °C) but does not melt the cast iron itself. This is achieved through capillary action, which requires a tight fit-up, cleanliness, and the use of flux. Brazing is especially suitable for small tubing, pipes, thin metal, and cast iron exhaust manifolds. However, proper preparation, such as cleaning the base metal and drilling holes at the ends of cracks, is crucial for successful brazing. The process offers several advantages, including limited heating, which reduces the risk of warping or cracking, and the ability to fill large lap joints without external welds.
Key Points Explained:
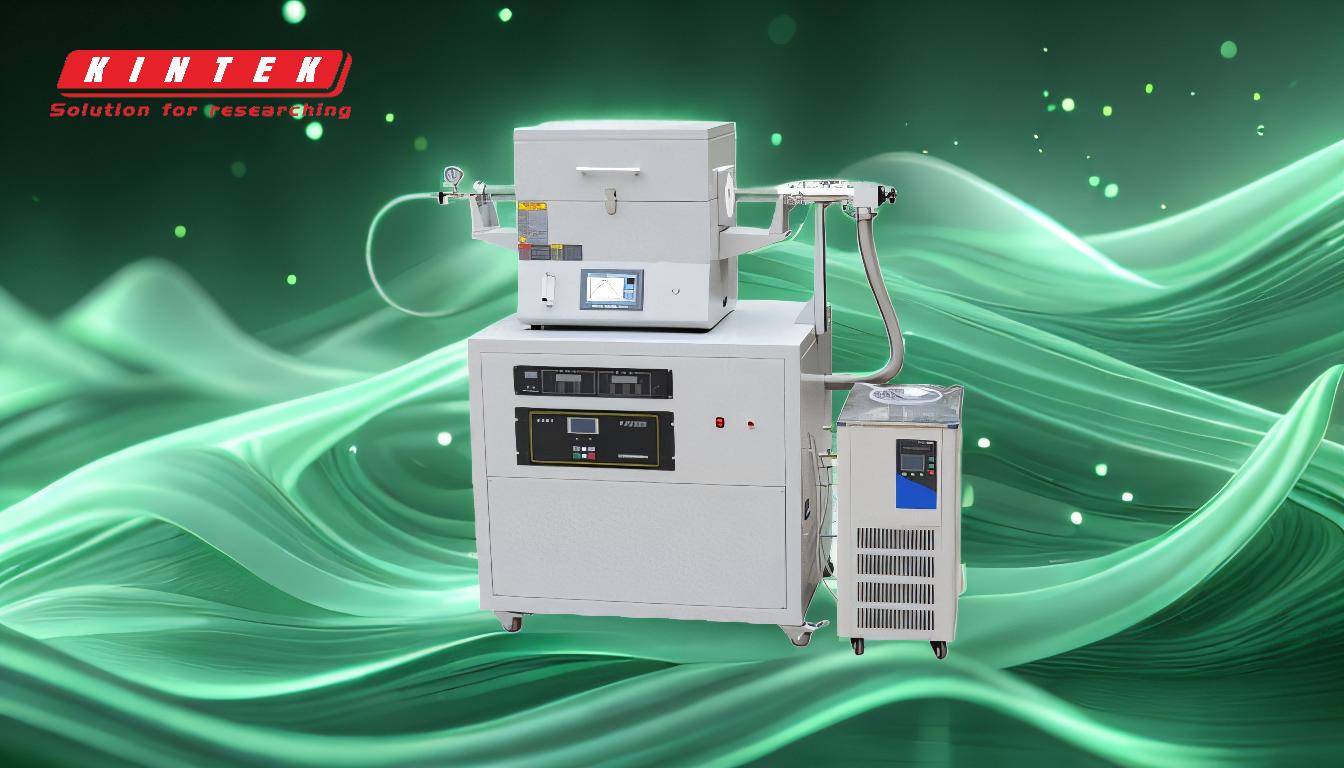
-
Brazing Process on Cast Iron:
- Brazing involves using a filler metal that melts at a temperature above 840 °F (450 °C) but below the melting point of cast iron. This ensures that the base metal remains intact while the filler metal flows into the joint through capillary action.
- The process requires a tight fit-up between the parts being joined, as well as thorough cleaning of the base metal to remove any contaminants like oil, grease, or dust. This preparation is essential to prevent defects in the brazed joint.
-
Suitability for Cast Iron:
- Brazing is particularly suitable for small tubing, pipes, thin metal, and cast iron exhaust manifolds. These applications benefit from the limited heating involved in brazing, which reduces the risk of warping or cracking that can occur with other joining methods like welding.
- For larger cast iron parts, furnace brazing is recommended to ensure uniform heating and to maintain the necessary temperature throughout the process.
-
Advantages of Brazing Cast Iron:
- Limited Heating: One of the primary advantages of brazing is that it does not heat the base metal to its melting point. This preserves the properties of the cast iron and reduces the risk of cracking, which is a common issue with welding.
- Filling Large Lap Joints: Brazing allows for the filling of large lap joints without the need for external welds. This is particularly useful in applications where a smooth, continuous joint is desired.
- Reduced Risk of Cracking: By avoiding the high temperatures required for welding, brazing minimizes the thermal stress on the cast iron, thereby reducing the likelihood of cracking.
-
Preparation and Techniques:
- Cleaning: Before brazing, it is crucial to clean the cast iron thoroughly to remove any contaminants that could interfere with the brazing process. This includes removing oil, grease, and dust.
- Crack Repair: When repairing cracked cast iron, drilling a hole at each end of the crack can prevent it from spreading further. This technique is often used in conjunction with brazing to ensure a durable repair.
- Flame and Temperature Control: A neutral or slightly oxidizing flame with a medium or heavy-duty welding nozzle is ideal for cast iron brazing. Maintaining the correct temperature throughout the process is essential for achieving a strong, defect-free joint.
-
Comparison with Welding:
- While welding provides superior strength by melting both the filler metal and the parent metal, it also introduces significant heat, which can be detrimental to cast iron. Welding is more prone to causing cracks and warping due to the high temperatures involved.
- Brazing, on the other hand, offers a more controlled heating process, making it a better option for applications where preserving the integrity of the cast iron is critical.
In summary, brazing is a highly effective method for joining cast iron, particularly in applications where minimizing heat input and preserving the base metal's properties are important. Proper preparation, including cleaning and crack repair, is essential for successful brazing. The process offers several advantages over welding, including reduced risk of cracking and the ability to fill large joints without external welds.
Summary Table:
Aspect | Details |
---|---|
Process | Uses filler metal melting above 840°F (450°C) but below cast iron's melting point. |
Suitable Applications | Small tubing, pipes, thin metal, cast iron exhaust manifolds. |
Advantages | Limited heating, reduced cracking risk, fills large lap joints without welds. |
Preparation | Clean base metal, drill crack ends, use flux, and control flame temperature. |
Comparison to Welding | Less heat input, lower risk of warping, and preserves cast iron integrity. |
Ready to explore brazing solutions for your cast iron projects? Contact us today for expert guidance!