Heat treatment is a critical process in metallurgy that can significantly influence the properties of metallic alloys, including their mechanical and electrical characteristics. By controlling the rate of diffusion and cooling, heat treatment can modify the microstructure of metals, which in turn affects properties such as hardness, strength, and conductivity. While plasma treatment primarily alters surface properties without affecting the bulk material, heat treatment can have a more profound impact on the overall material properties, including electrical conductivity.
Key Points Explained:
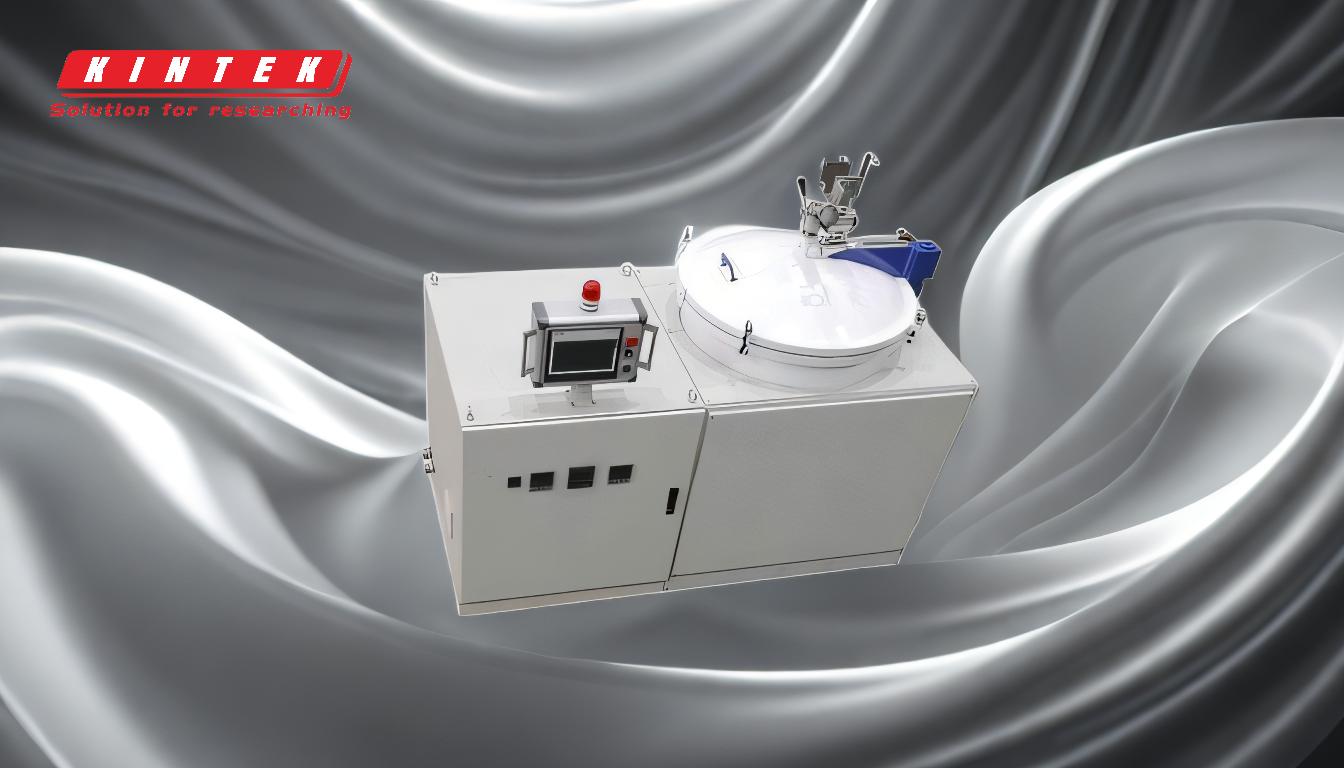
-
Impact of Heat Treatment on Microstructure:
- Heat treatment involves heating and cooling metals to alter their physical and mechanical properties. This process can change the grain structure, phase composition, and distribution of elements within the metal.
- The microstructure changes can lead to variations in electrical conductivity, as the movement of electrons is influenced by the arrangement of atoms and defects within the material.
-
Effect on Electrical Conductivity:
- Electrical conductivity in metals is primarily determined by the ease with which electrons can move through the material. Heat treatment can affect this by:
- Grain Size: Smaller grains can increase the number of grain boundaries, which can scatter electrons and reduce conductivity.
- Phase Transformations: Changes in phase (e.g., from austenite to martensite) can alter the electronic structure and thus the conductivity.
- Defect Density: Heat treatment can introduce or reduce defects such as dislocations, which can impede electron flow.
- Electrical conductivity in metals is primarily determined by the ease with which electrons can move through the material. Heat treatment can affect this by:
-
Comparison with Plasma Treatment:
- Plasma treatment is a surface modification technique that does not significantly alter the bulk properties of the material. It primarily affects surface energy, wettability, and adhesion, but has minimal impact on electrical conductivity.
- In contrast, heat treatment can modify the entire volume of the material, leading to more substantial changes in properties, including conductivity.
-
Practical Implications for Material Selection:
- When selecting materials for applications where electrical conductivity is critical, it is important to consider the effects of heat treatment. For example:
- Annealing: This process can reduce internal stresses and increase ductility, but may also decrease conductivity due to grain growth.
- Quenching: Rapid cooling can increase hardness and strength, but may also introduce defects that reduce conductivity.
- Tempering: This can relieve some of the stresses introduced by quenching, potentially improving conductivity while maintaining desirable mechanical properties.
- When selecting materials for applications where electrical conductivity is critical, it is important to consider the effects of heat treatment. For example:
-
Conclusion:
- Heat treatment can have a significant impact on the electrical conductivity of metallic alloys by altering their microstructure. The specific effects depend on the type of heat treatment and the material involved. Understanding these effects is crucial for optimizing material properties for specific applications, especially those requiring precise control over electrical conductivity.
By carefully considering the type and parameters of heat treatment, engineers and material scientists can tailor the properties of metals to meet the specific needs of their applications, balancing mechanical strength with electrical performance.
Summary Table:
Factor | Effect on Conductivity |
---|---|
Grain Size | Smaller grains increase grain boundaries, scattering electrons and reducing conductivity. |
Phase Transformations | Changes in phase (e.g., austenite to martensite) alter electronic structure and conductivity. |
Defect Density | Defects like dislocations introduced by heat treatment can impede electron flow. |
Annealing | Reduces internal stresses but may decrease conductivity due to grain growth. |
Quenching | Increases hardness but may introduce defects that reduce conductivity. |
Tempering | Relieves stresses from quenching, potentially improving conductivity. |
Need help optimizing heat treatment for your materials? Contact our experts today to achieve the perfect balance of strength and conductivity!