Porcelain, like many ceramic materials, requires firing to achieve its final hardened and durable state. Firing is a critical step in the porcelain-making process, as it transforms the raw clay into a solid, vitrified material. The firing process involves heating the porcelain to high temperatures in a kiln, which causes chemical and physical changes in the clay, resulting in a strong, non-porous, and glass-like surface. Without firing, porcelain would remain in a fragile, unfired state, unsuitable for functional or decorative use.
Key Points Explained:
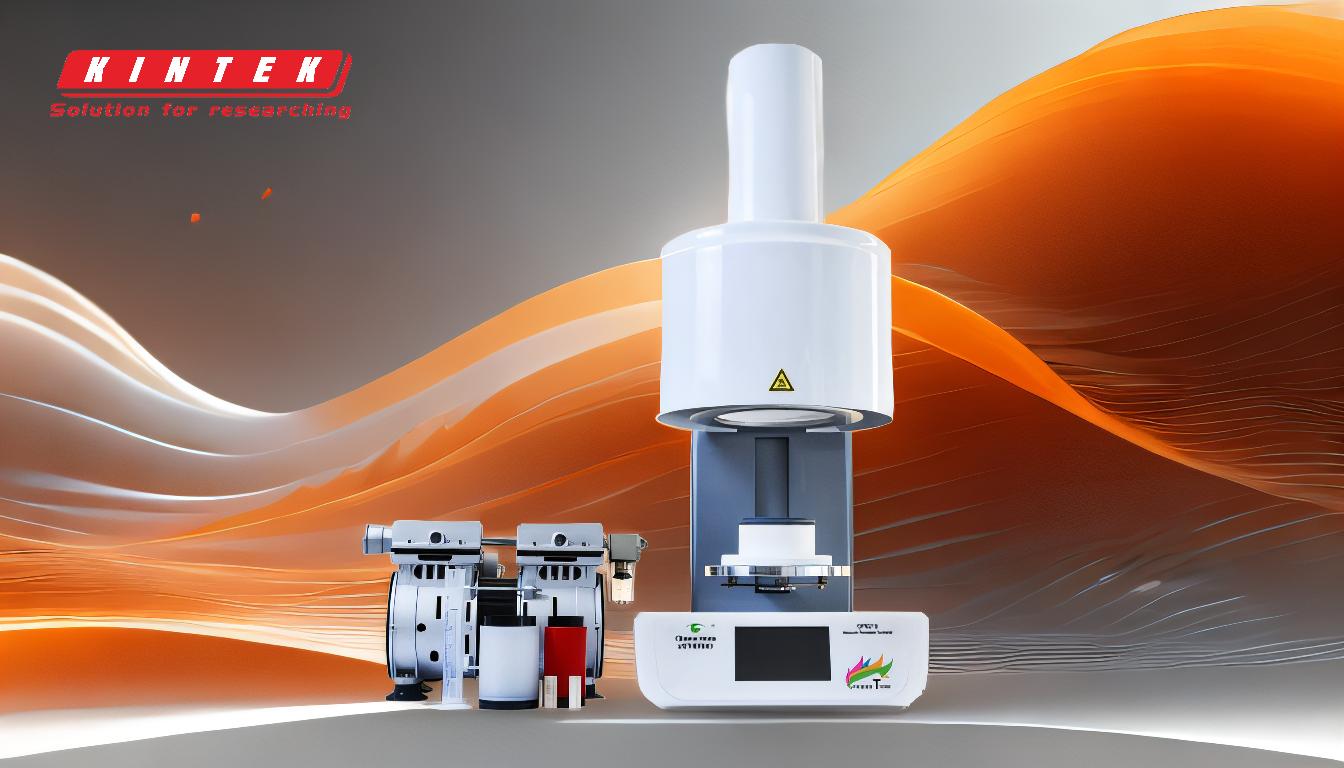
-
Why Porcelain Needs to Be Fired:
- Porcelain is made from a specific type of clay that contains kaolin, feldspar, and quartz. These materials undergo significant changes when exposed to high temperatures.
- Firing causes the clay particles to fuse together, creating a dense and durable material. This process is known as vitrification, where the clay becomes glass-like and non-porous.
- Without firing, porcelain would remain porous, brittle, and unable to hold liquids or withstand everyday use.
-
The Firing Process:
- The firing process typically involves two main stages: bisque firing and glaze firing.
- Bisque Firing: This is the first firing stage, where the raw porcelain is heated to a lower temperature (around 1650°F to 1940°F). This removes any remaining moisture and organic materials, making the piece harder and more stable for glazing.
- Glaze Firing: After the bisque firing, the porcelain is coated with a glaze and fired again at a higher temperature (around 2200°F to 2400°F). This melts the glaze, creating a smooth, glassy surface that is both decorative and functional.
- The firing cycle settings, such as temperature ramp rates and hold times, are carefully controlled to ensure proper vitrification and avoid defects like cracking or warping.
- The firing process typically involves two main stages: bisque firing and glaze firing.
-
Importance of Temperature Control:
- Porcelain must be fired at specific temperatures to achieve the desired results. The exact temperature depends on the composition of the clay and glaze.
- Over-firing can cause the porcelain to warp or melt, while under-firing may result in a weak, porous material that lacks strength and durability.
- Modern kilns often use pre-set or custom programs to ensure precise temperature control throughout the firing process.
-
Role of Atmosphere in Firing:
- The atmosphere inside the kiln can affect the final appearance and properties of the porcelain. For example, firing in a vacuum or reducing atmosphere (low oxygen) can produce unique colors and finishes.
- The general purging process described in the reference—heating the furnace under vacuum and then releasing the vacuum—is an example of how controlled atmospheres are used in advanced firing techniques.
-
Final Properties of Fired Porcelain:
- After firing, porcelain becomes highly durable, resistant to thermal shock, and impermeable to water. These properties make it ideal for tableware, decorative items, and industrial applications.
- The firing process also enhances the aesthetic qualities of porcelain, giving it a smooth, translucent, and refined appearance.
In summary, firing is an essential step in the creation of porcelain. It transforms the raw clay into a strong, durable, and beautiful material through controlled heating and vitrification. Without firing, porcelain would lack the strength, functionality, and aesthetic appeal that make it so highly valued.
Summary Table:
Key Aspect | Details |
---|---|
Why Porcelain Needs Firing | Firing transforms raw clay into a strong, non-porous, and durable material. |
Firing Process | - Bisque Firing: 1650°F–1940°F, removes moisture. |
- Glaze Firing: 2200°F–2400°F, creates a smooth, glassy surface. | |
Temperature Control | Precise temperatures are critical to avoid warping, cracking, or under-firing. |
Role of Atmosphere | Controlled atmospheres (e.g., vacuum) can enhance colors and finishes. |
Final Properties | Durable, water-resistant, and aesthetically refined after firing. |
Unlock the full potential of porcelain with expert firing techniques—contact us today to learn more!