PVD (Physical Vapor Deposition) coatings are renowned for their durability, hardness, and resistance to corrosion and wear. These coatings are applied in a vacuum environment, which ensures a strong bond with the substrate and prevents contamination, oxidation, and degradation. Due to their high hardness, wear resistance, and low friction properties, PVD coatings are widely used in industries such as automotive, aerospace, and medical. Their resistance to tarnishing is a key advantage, as they are highly resistant to corrosion and oxidation, even in harsh environments. The thinness of the coatings (0.5 to 5 microns) further enhances their durability and ability to replicate the original finish of materials.
Key Points Explained:
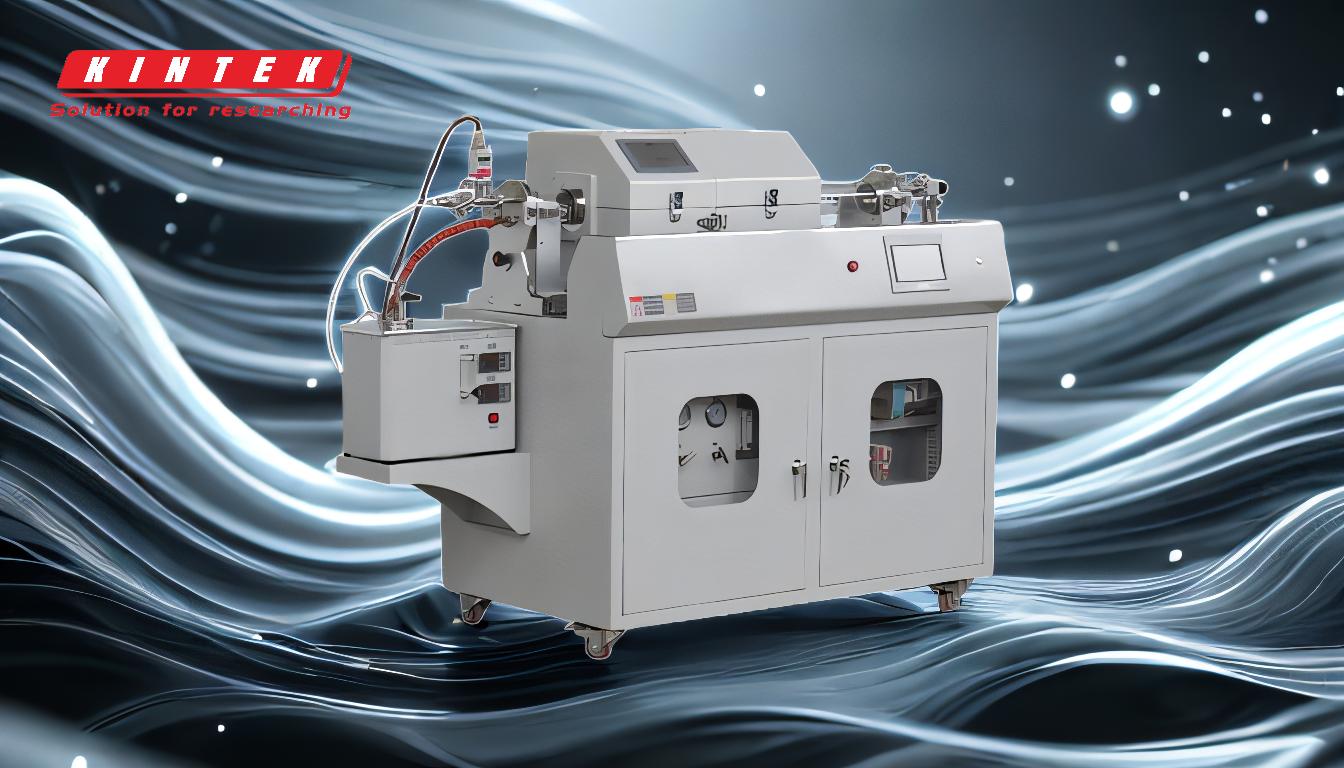
-
Durability and Hardness of PVD Coatings
- PVD coatings are known for their super-hard properties, making them the most durable coatings available today.
- Their hardness contributes to their ability to resist wear, scratching, and abrasion, which are common causes of tarnishing in other materials.
- The hardness of the coating is directly linked to its durability, ensuring that it maintains its appearance and functionality over time.
-
Resistance to Corrosion and Oxidation
- PVD coatings are highly resistant to corrosion and oxidation, which are primary causes of tarnishing.
- The vacuum environment during the coating process eliminates contamination and prevents oxidation, ensuring a longer-lasting finish.
- This resistance makes PVD coatings ideal for applications in harsh environments, such as marine or industrial settings, where exposure to moisture and chemicals is common.
-
Thinness and Bond Strength
- PVD coatings are extremely thin, ranging from 0.5 to 5 microns, which allows them to replicate the original finish of materials with minimal effort.
- The thinness of the coating, combined with its strong bond to the substrate, makes it difficult to remove and enhances its durability.
- This strong bond ensures that the coating remains intact and resistant to tarnishing, even under mechanical stress or environmental exposure.
-
Applications in Demanding Industries
- PVD coatings are widely used in industries such as automotive, aerospace, and medical, where durability and resistance to tarnishing are critical.
- Their robust temperature tolerance, impact strength, and abrasion resistance make them suitable for demanding applications.
- The ability of PVD coatings to maintain their appearance and functionality in these industries highlights their resistance to tarnishing.
-
Superior Quality Compared to Traditional Finishes
- PVD coatings offer superior quality and longevity compared to traditional finishes, which are more prone to tarnishing over time.
- The vacuum environment during application ensures a contamination-free coating, further enhancing its resistance to tarnishing.
- This superior quality makes PVD coatings a preferred choice for applications where maintaining a pristine appearance is essential.
In conclusion, PVD coatings are highly resistant to tarnishing due to their hardness, resistance to corrosion and oxidation, thinness, and strong bond with the substrate. These properties make them an ideal choice for applications where durability and maintaining a pristine appearance are critical.
Summary Table:
Property | Description |
---|---|
Durability & Hardness | PVD coatings are super-hard, resisting wear, scratching, and abrasion. |
Corrosion Resistance | Highly resistant to oxidation and corrosion, even in harsh environments. |
Thinness & Bond Strength | Extremely thin (0.5-5 microns) with a strong bond to the substrate. |
Applications | Widely used in automotive, aerospace, and medical industries for durability. |
Superior Quality | Outperforms traditional finishes with longer-lasting, contamination-free results. |
Discover how PVD coatings can enhance your product's durability—contact us today!