PVD (Physical Vapor Deposition) vacuum plating is highly resistant to tarnishing due to its exceptional durability, corrosion resistance, and hardness. The thin, super-hard coating provides long-lasting protection against environmental factors that typically cause tarnishing, such as oxidation, moisture, and wear. With proper care, PVD-plated items can maintain their appearance and functionality for many years, making them a superior choice for applications where durability and aesthetics are critical.
Key Points Explained:
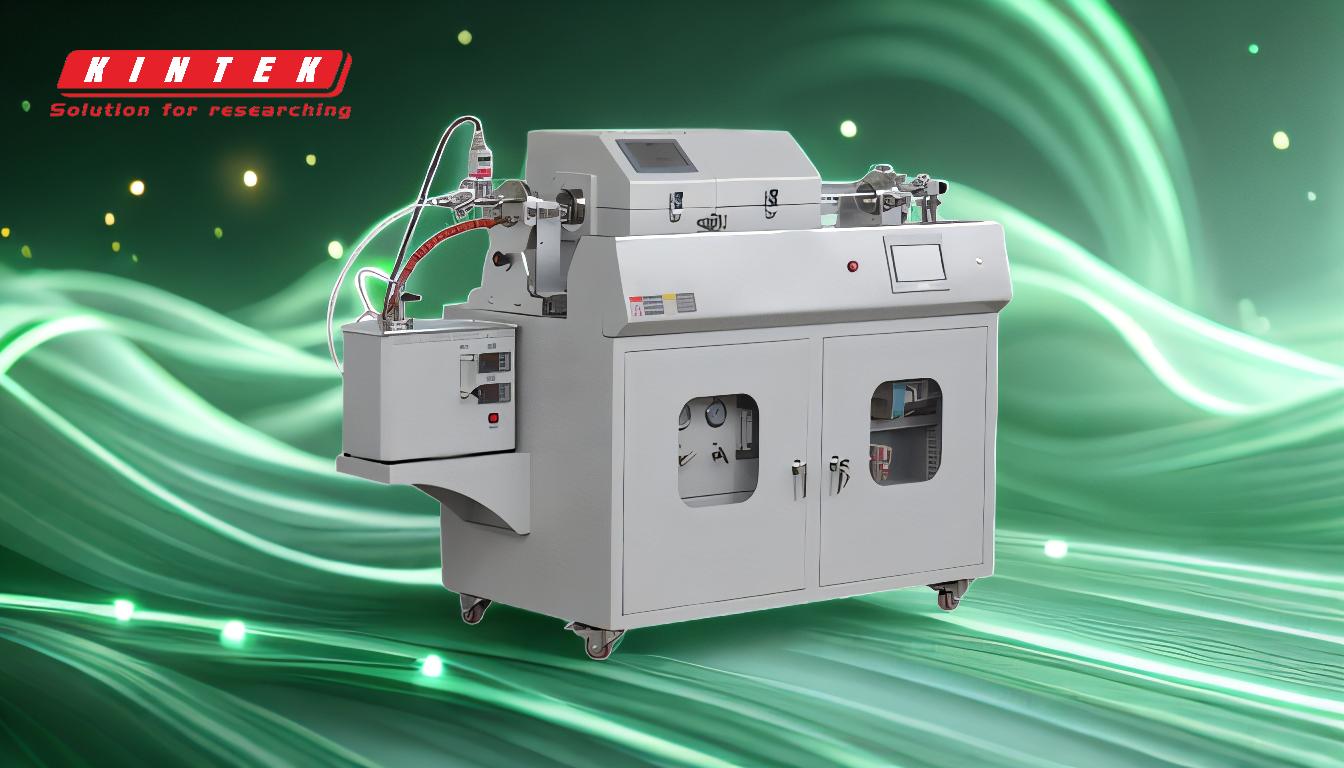
-
Durability and Resistance to Tarnishing:
- PVD coatings are highly durable and resistant to corrosion and oxidation, which are primary causes of tarnishing.
- The coatings are super-hard and provide a robust barrier against environmental factors like moisture, chemicals, and wear.
- This makes PVD-plated items highly resistant to tarnishing compared to traditional finishes like electroplating.
-
Thin and Adherent Coating:
- PVD coatings are extremely thin, ranging from 0.5 to 5 microns, but their adherence to the substrate is strong.
- This thin yet durable layer ensures that the coating remains intact over time, preventing exposure of the underlying material to tarnishing agents.
-
Corrosion and Oxidation Resistance:
- PVD coatings are specifically designed to resist corrosion and oxidation, which are the main contributors to tarnishing.
- This makes them ideal for use in environments where exposure to moisture, chemicals, or other corrosive elements is common.
-
Longevity with Proper Care:
- With correct care and maintenance, PVD-plated items can maintain their elegance and attractiveness for many years.
- This longevity is a testament to the coating's ability to resist tarnishing and wear over time.
-
Comparison to Electroplating:
- PVD-coated items, such as jewelry, are significantly more durable and long-lasting than electroplated items.
- Electroplated jewelry typically lasts about 1 year with everyday wear, whereas PVD-coated jewelry can last 3 years or more, highlighting its superior resistance to tarnishing.
-
Material-Specific Properties:
- The properties of PVD coatings, including their resistance to tarnishing, are influenced by the underlying substrate material.
- For example, coatings like TiN (Titanium Nitride) enhance the fatigue limit and endurance of materials, further contributing to their durability and resistance to tarnishing.
-
Applications in Demanding Environments:
- PVD coatings are suitable for demanding applications where durability and resistance to tarnishing are critical.
- Their ability to replicate the original finish of materials with minimal effort ensures that the aesthetic appeal is maintained over time.
In summary, PVD vacuum plating is highly resistant to tarnishing due to its exceptional durability, corrosion resistance, and hardness. With proper care, PVD-plated items can maintain their appearance and functionality for many years, making them a superior choice for applications where durability and aesthetics are critical.
Summary Table:
Feature | Description |
---|---|
Durability | Highly resistant to corrosion, oxidation, and wear. |
Thin Coating | 0.5 to 5 microns thick, yet strongly adherent to the substrate. |
Corrosion Resistance | Designed to resist moisture, chemicals, and other corrosive elements. |
Longevity | Maintains appearance and functionality for years with proper care. |
Comparison to Electroplating | Lasts 3+ years vs. 1 year for electroplated items. |
Material-Specific Properties | Enhances fatigue limit and endurance, depending on the substrate material. |
Applications | Ideal for demanding environments requiring durability and aesthetics. |
Discover how PVD vacuum plating can enhance your products—contact our experts today!