Sintering is a manufacturing process that involves heating powdered materials below their melting point to bond particles and reduce porosity, resulting in a denser and more cohesive structure. While sintering is known to enhance properties like strength, hardness, and wear resistance, its effect on ductility is more nuanced. Ductility, the ability of a material to deform plastically under stress without fracturing, depends on factors such as grain size, porosity, and microstructure. Sintering can improve ductility in some cases by reducing porosity and creating a more uniform microstructure, but it may also reduce ductility if grain growth or other microstructural changes occur during the process.
Key Points Explained:
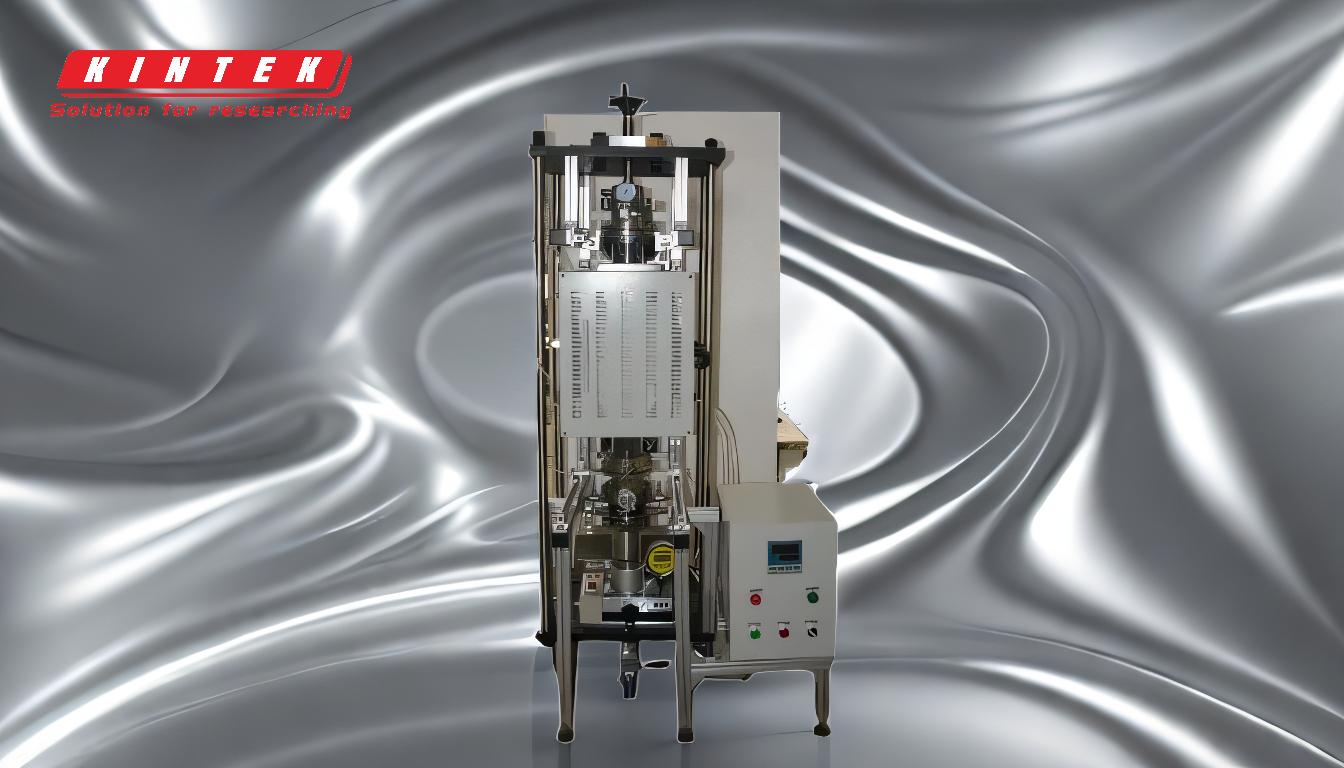
-
Definition and Purpose of Sintering:
- Sintering is a process that heats powdered materials below their melting point to bond particles and reduce porosity.
- It aims to create dense, cohesive structures with improved mechanical properties such as strength, hardness, and wear resistance.
-
Effect of Sintering on Microstructure:
- Sintering reduces surface porosity, which can enhance properties like conductivity, corrosion resistance, and tensile strength.
- It also affects grain size, pore size, and grain boundary distribution, which influence material properties, including ductility.
-
Impact on Ductility:
-
Positive Effects:
- Reduction in porosity can lead to a more uniform microstructure, which may improve ductility by allowing for more even stress distribution.
- Smaller grain sizes, often achieved through controlled sintering, can enhance ductility by providing more grain boundaries that hinder crack propagation.
-
Negative Effects:
- Excessive grain growth during sintering can reduce ductility by creating larger grains that are more prone to cracking.
- Over-sintering or improper sintering conditions can lead to embrittlement, reducing the material's ability to deform plastically.
-
Positive Effects:
-
Material-Specific Considerations:
- Metals: Sintering can improve ductility in metals by reducing porosity and creating a more homogeneous structure. However, the specific alloy and sintering conditions play a significant role.
- Ceramics: Sintering typically increases strength and hardness in ceramics but often reduces ductility due to their inherently brittle nature.
- Composites: The effect of sintering on ductility in composite materials depends on the interaction between the matrix and reinforcement phases.
-
Process Control and Optimization:
- Controlling sintering parameters such as temperature, time, and atmosphere is crucial for achieving the desired balance between strength and ductility.
- Advanced sintering techniques, such as spark plasma sintering (SPS) or microwave sintering, can offer better control over microstructure and properties.
-
Applications and Trade-offs:
- Sintering is widely used in industries requiring high strength and wear resistance, such as automotive and aerospace.
- In applications where ductility is critical, such as certain metal components, sintering must be carefully optimized to avoid compromising this property.
In summary, sintering can increase ductility under specific conditions, such as when it reduces porosity and refines grain size. However, it can also decrease ductility if grain growth or other microstructural changes occur. The effect of sintering on ductility is highly dependent on the material type, sintering conditions, and desired application.
Summary Table:
Aspect | Impact on Ductility |
---|---|
Porosity Reduction | Improves ductility by creating a more uniform microstructure. |
Grain Size Control | Smaller grains enhance ductility; excessive grain growth reduces it. |
Material Type | Metals: Can improve ductility; Ceramics: Often reduces ductility. |
Sintering Conditions | Proper control of temperature, time, and atmosphere is crucial for optimal ductility. |
Advanced Techniques | Techniques like SPS or microwave sintering offer better control over ductility. |
Discover how sintering can optimize your material properties—contact our experts today!