Biomass pellets are formed through a process that involves several key steps: preparation of raw materials, drying, pelletizing, cooling, and packaging. The raw materials, which can include wood chips, sawdust, agricultural residues, or other biomass, are first collected and prepared by reducing them to a uniform size. These materials are then dried to reduce moisture content, which is crucial for efficient pelletizing. The dried biomass is fed into a pellet mill, where it is compressed under high pressure and forced through a die to form dense, cylindrical pellets. The pellets are then cooled to stabilize them and reduce moisture further. Finally, they are packaged for storage or transport. This process not only enhances the energy density of the biomass but also makes it easier to handle, transport, and store.
Key Points Explained:
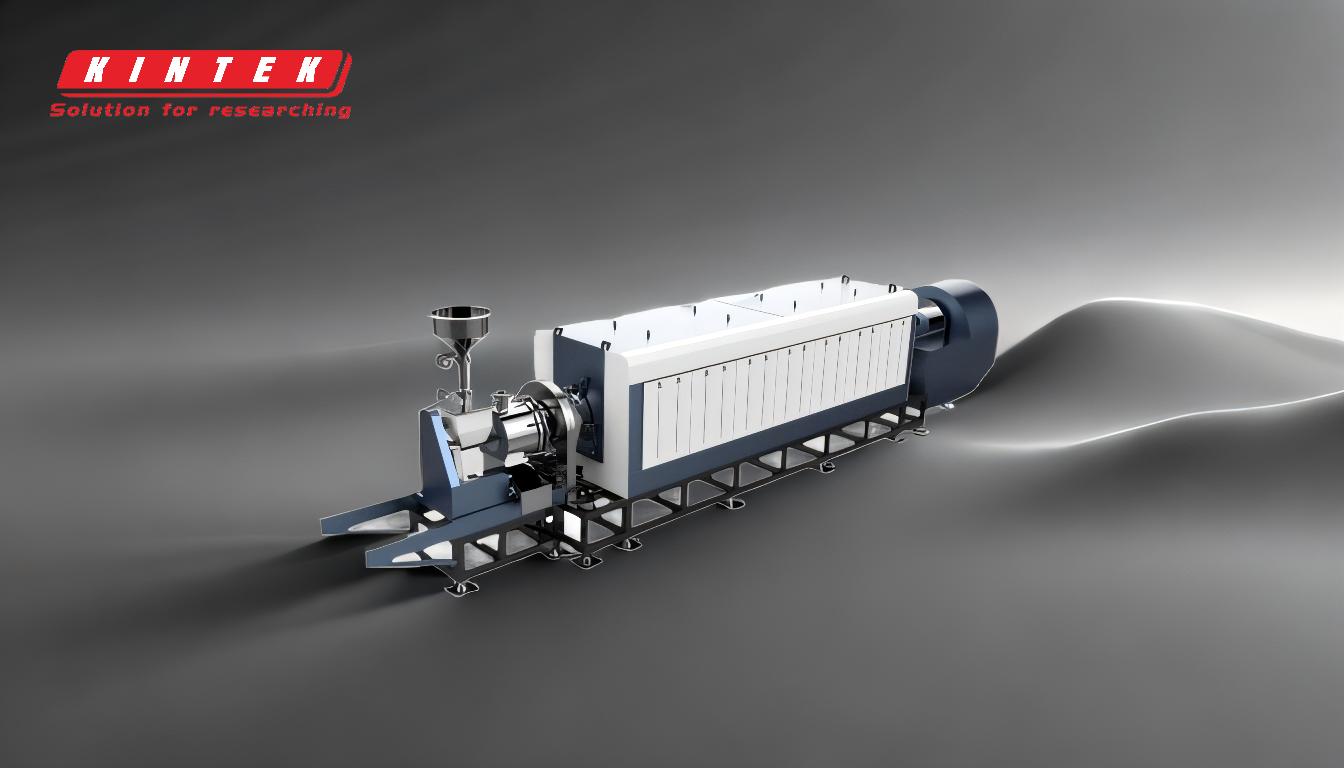
-
Preparation of Raw Materials:
- Collection: Biomass materials such as wood chips, sawdust, or agricultural residues are collected from various sources.
- Size Reduction: The collected biomass is processed to achieve a uniform size, often through chipping or grinding. This uniformity is essential for consistent pellet quality.
-
Drying:
- Moisture Reduction: The biomass is dried to reduce its moisture content to an optimal level, typically between 10-15%. High moisture content can hinder the pelletizing process and reduce the quality of the final product.
- Drying Methods: Common drying methods include rotary dryers or belt dryers, which use heat to evaporate moisture from the biomass.
-
Pelletizing:
- Compression: The dried biomass is fed into a pellet mill, where it is compressed under high pressure.
- Die Extrusion: The compressed biomass is forced through a die with small holes, shaping it into dense, cylindrical pellets.
- Binding Agents: In some cases, natural binding agents like lignin are used to help the biomass particles adhere together during compression.
-
Cooling:
- Stabilization: After pelletizing, the pellets are hot and need to be cooled to stabilize their structure.
- Moisture Control: Cooling also helps to further reduce any residual moisture, ensuring the pellets are durable and less prone to degradation.
-
Packaging:
- Storage: The cooled pellets are packaged in bags or bulk containers for storage or transport.
- Transportation: Packaging ensures that the pellets remain intact and dry during transportation to their final destination.
-
Quality Control:
- Standards: The entire process is monitored to ensure that the pellets meet specific quality standards, such as size, density, and moisture content.
- Testing: Pellets may undergo various tests to ensure they meet the required specifications for burning efficiency and durability.
By following these steps, biomass pellets are formed into a highly efficient and manageable form of fuel, suitable for a variety of applications, including heating and power generation.
Summary Table:
Step | Description |
---|---|
Preparation | Raw materials like wood chips or sawdust are collected and reduced to uniform size. |
Drying | Biomass is dried to 10-15% moisture using rotary or belt dryers. |
Pelletizing | Dried biomass is compressed in a pellet mill and extruded through a die. |
Cooling | Pellets are cooled to stabilize structure and reduce residual moisture. |
Packaging | Cooled pellets are packaged for storage or transport. |
Quality Control | Pellets are tested for size, density, and moisture to meet standards. |
Discover how biomass pellets can transform your energy solutions—contact us today for expert advice!