Diamond-coated tools are manufactured through a meticulous process that involves preparing the tool surface and applying a diamond-like carbon (DLC) coating using the Physical Vapor Deposition (PVD) method. The preparation stage includes cleaning the tools and chemically treating the carbide surface to enhance adhesion and remove cobalt, which inhibits diamond growth. The PVD process then evaporates a source material, allowing it to condense onto the tool and form a thin, durable DLC coating ranging from 0.5 to 2.5 microns in thickness. This coating provides the tools with enhanced hardness, wear resistance, and performance characteristics.
Key Points Explained:
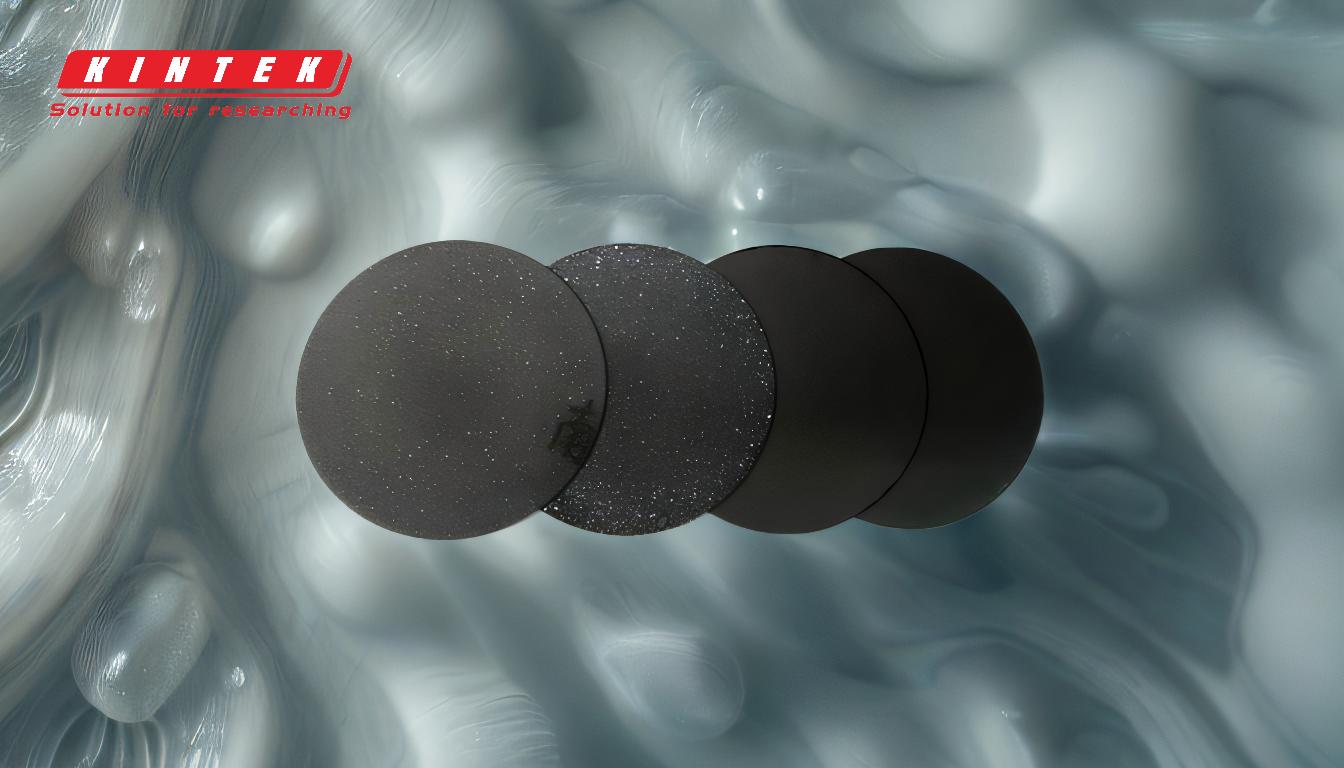
-
Preparation of the Tool Surface:
- Cleaning: The tools are thoroughly cleaned to remove any contaminants that could interfere with the coating process. This ensures a pristine surface for optimal adhesion.
-
Chemical Treatment: The carbide surface undergoes a two-step chemical process:
- Surface Roughening: The first step roughens the carbide surface to improve mechanical adhesion. A rough surface provides more surface area for the coating to bond effectively.
- Cobalt Removal: The second step removes cobalt from the surface. Cobalt, often present in carbide tools, is detrimental to diamond growth. Its removal ensures a more stable and effective coating.
-
Physical Vapor Deposition (PVD) Process:
- Evaporation: A source material, typically containing carbon, is evaporated in a vacuum chamber. This process transforms the material into a vapor state.
- Condensation: The vaporized material is then allowed to condense onto the tool surface. This forms a thin, uniform layer of Diamond-Like Carbon (DLC).
- Coating Thickness: The resulting DLC coating is typically between 0.5 to 2.5 microns thick. This thickness is carefully controlled to balance performance and durability.
-
Diamond-Like Carbon (DLC) Coating:
- Properties: DLC coatings exhibit properties similar to natural diamond, such as high hardness, low friction, and excellent wear resistance. These properties make diamond-coated tools ideal for demanding applications.
- Amorphous Structure: Unlike crystalline diamond, DLC coatings have an amorphous structure, which provides a unique combination of hardness and flexibility.
-
Advantages of Diamond-Coated Tools:
- Enhanced Durability: The DLC coating significantly improves the tool's resistance to wear and abrasion, extending its lifespan.
- Improved Performance: Diamond-coated tools offer superior cutting performance, especially in high-speed and high-precision applications.
- Versatility: These tools are suitable for a wide range of materials, including composites, non-ferrous metals, and plastics.
-
Applications of Diamond-Coated Tools:
- Machining: Diamond-coated tools are widely used in machining applications where high precision and durability are required.
- Cutting and Drilling: They are ideal for cutting and drilling operations in industries such as aerospace, automotive, and electronics.
- Wear-Resistant Components: Tools with DLC coatings are also used in applications where resistance to wear and corrosion is critical.
-
Considerations for Purchasers:
- Coating Thickness: Depending on the application, purchasers should consider the optimal coating thickness. Thicker coatings may offer greater durability but could affect precision.
- Surface Preparation: The quality of the surface preparation process directly impacts the adhesion and performance of the coating. Ensure that the tools undergo proper cleaning and chemical treatment.
- Material Compatibility: Verify that the DLC coating is compatible with the materials being machined or processed.
By understanding the detailed process of creating diamond-coated tools, purchasers can make informed decisions that align with their specific needs and applications. The combination of advanced surface preparation and PVD technology ensures that diamond-coated tools deliver exceptional performance and longevity.
Summary Table:
Key Aspect | Details |
---|---|
Surface Preparation | Cleaning and chemical treatment to enhance adhesion and remove cobalt. |
PVD Process | Evaporation and condensation of carbon to form a DLC coating (0.5-2.5 µm). |
DLC Coating Properties | High hardness, low friction, and excellent wear resistance. |
Advantages | Enhanced durability, improved performance, and versatility. |
Applications | Machining, cutting, drilling, and wear-resistant components. |
Purchasing Considerations | Coating thickness, surface preparation, and material compatibility. |
Upgrade your tools with diamond coatings for unmatched performance—contact us today!