Diamond coating on tools is achieved through advanced deposition techniques, primarily Physical Vapor Deposition (PVD) and Chemical Vapor Deposition (CVD). These methods involve creating a thin, durable layer of diamond-like carbon (DLC) or crystalline diamond on the tool's surface. PVD involves evaporating a source material and condensing it onto the tool, while CVD uses chemical reactions to deposit diamond layers. The process begins with thorough cleaning and surface preparation, including roughening the carbide surface and removing cobalt, which inhibits diamond growth. The resulting coatings, typically 0.5 to 2.5 microns thick, enhance tool durability, hardness, and performance in demanding applications.
Key Points Explained:
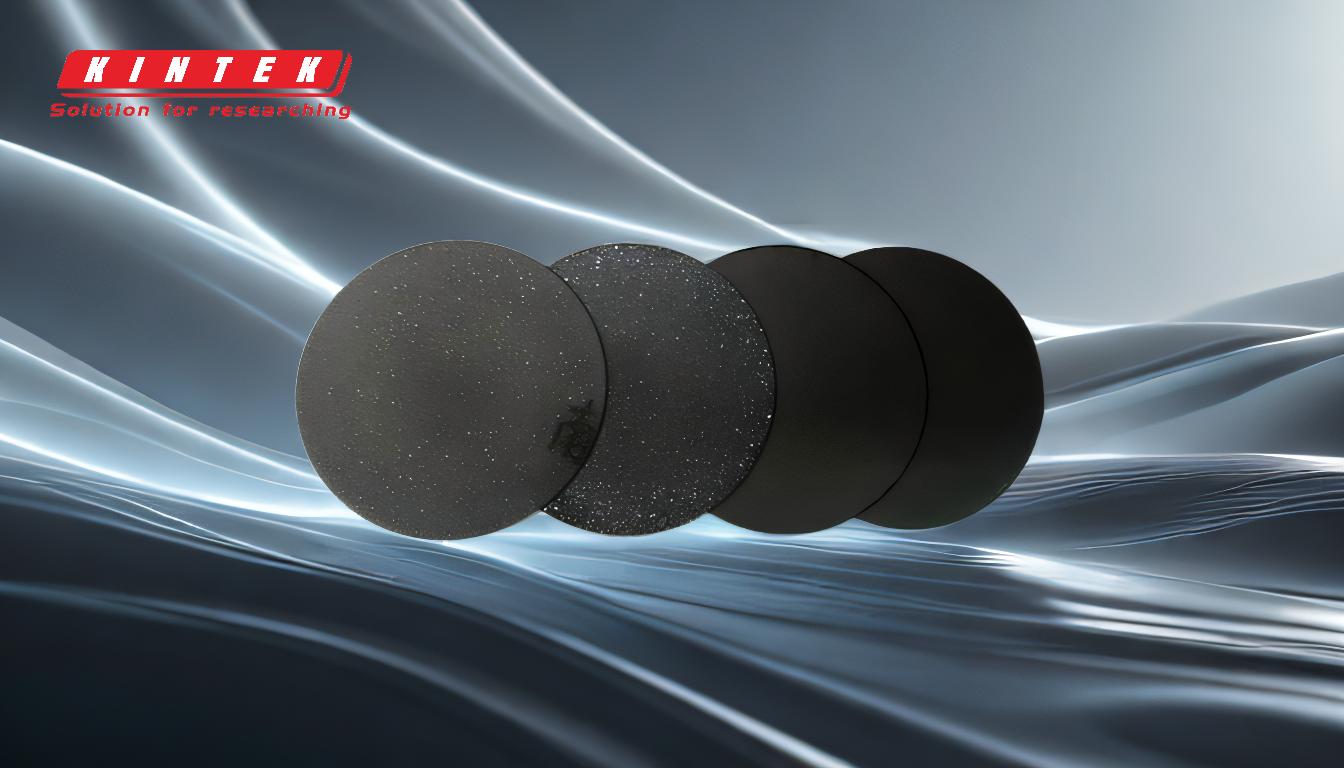
-
Overview of Diamond Coating Methods:
-
PVD (Physical Vapor Deposition):
- A process where a source material is evaporated and then condensed onto the tool surface to form a thin, uniform layer of Diamond-Like Carbon (DLC).
- Commonly used for amorphous diamond coatings.
-
CVD (Chemical Vapor Deposition):
- Involves chemical reactions to deposit diamond layers on the tool surface.
- Techniques include Microwave Plasma CVD (MPCVD), DC Arc Plasma Spray CVD (DAPCVD), and Hot Wire CVD (HFCVD).
-
PVD (Physical Vapor Deposition):
-
Preparation of Tools for Coating:
-
Cleaning:
- Tools are thoroughly cleaned to remove contaminants that could interfere with adhesion.
-
Surface Roughening:
- The carbide surface is roughened to improve mechanical adhesion of the coating.
-
Cobalt Removal:
- Cobalt, which is toxic to diamond growth, is removed from the surface to ensure proper diamond layer formation.
-
Cleaning:
-
Coating Process:
-
PVD Process:
- A source material (e.g., graphite) is evaporated in a vacuum chamber.
- The vaporized material condenses onto the tool, forming a DLC layer.
- The coating thickness typically ranges from 0.5 to 2.5 microns.
-
CVD Process:
- A gas mixture (e.g., methane and hydrogen) is introduced into a chamber.
- Chemical reactions at high temperatures or under plasma conditions deposit diamond layers on the tool.
- Techniques like MPCVD and HFCVD allow for precise control over coating quality and thickness.
-
PVD Process:
-
Types of Diamond Coatings:
-
Amorphous Diamond (DLC):
- Applied via PVD, offering excellent hardness, low friction, and wear resistance.
- Ideal for applications requiring smooth surfaces and reduced friction.
-
Crystalline Diamond:
- Applied via CVD, providing superior hardness and thermal conductivity.
- Suitable for high-precision cutting and machining applications.
-
Amorphous Diamond (DLC):
-
Applications and Benefits:
-
Enhanced Tool Performance:
- Diamond coatings significantly improve tool lifespan, hardness, and resistance to wear and corrosion.
-
Versatility:
- Used in industries such as aerospace, automotive, and manufacturing for cutting, drilling, and machining applications.
-
Cost Efficiency:
- Extends tool life, reducing the need for frequent replacements and downtime.
-
Enhanced Tool Performance:
-
Challenges and Considerations:
-
Adhesion Issues:
- Proper surface preparation is critical to ensure strong adhesion of the diamond coating.
-
Cost of Equipment:
- PVD and CVD systems require significant investment, making the process expensive for small-scale operations.
-
Coating Uniformity:
- Achieving a uniform coating thickness can be challenging, especially on complex tool geometries.
-
Adhesion Issues:
By understanding these key points, purchasers and users of diamond-coated tools can make informed decisions about selecting the right coating method and tool type for their specific applications.
Summary Table:
Aspect | Details |
---|---|
Coating Methods | - PVD: Evaporates and condenses material for DLC coatings. |
- CVD: Uses chemical reactions for crystalline diamond coatings. | |
Preparation Steps | - Cleaning, surface roughening, and cobalt removal for optimal adhesion. |
Coating Thickness | 0.5 to 2.5 microns, enhancing durability and performance. |
Types of Coatings | - Amorphous Diamond (DLC): Low friction, wear resistance. |
- Crystalline Diamond: Superior hardness, thermal conductivity. | |
Applications | Aerospace, automotive, and manufacturing for cutting, drilling, and machining. |
Challenges | Adhesion issues, high equipment costs, and coating uniformity. |
Discover how diamond-coated tools can revolutionize your operations—contact us today for expert guidance!