Creating a reducing atmosphere in a furnace involves controlling the chemical composition of the furnace environment to promote reduction reactions, which are essential in processes like metal heat treatment, sintering, and brazing. A reducing atmosphere minimizes oxidation and can be achieved through various methods, including the use of specific gas mixtures, combustion products, or advanced control systems. The key is to tailor the atmosphere to the specific requirements of the process, ensuring optimal conditions for the desired chemical reactions.
Key Points Explained:
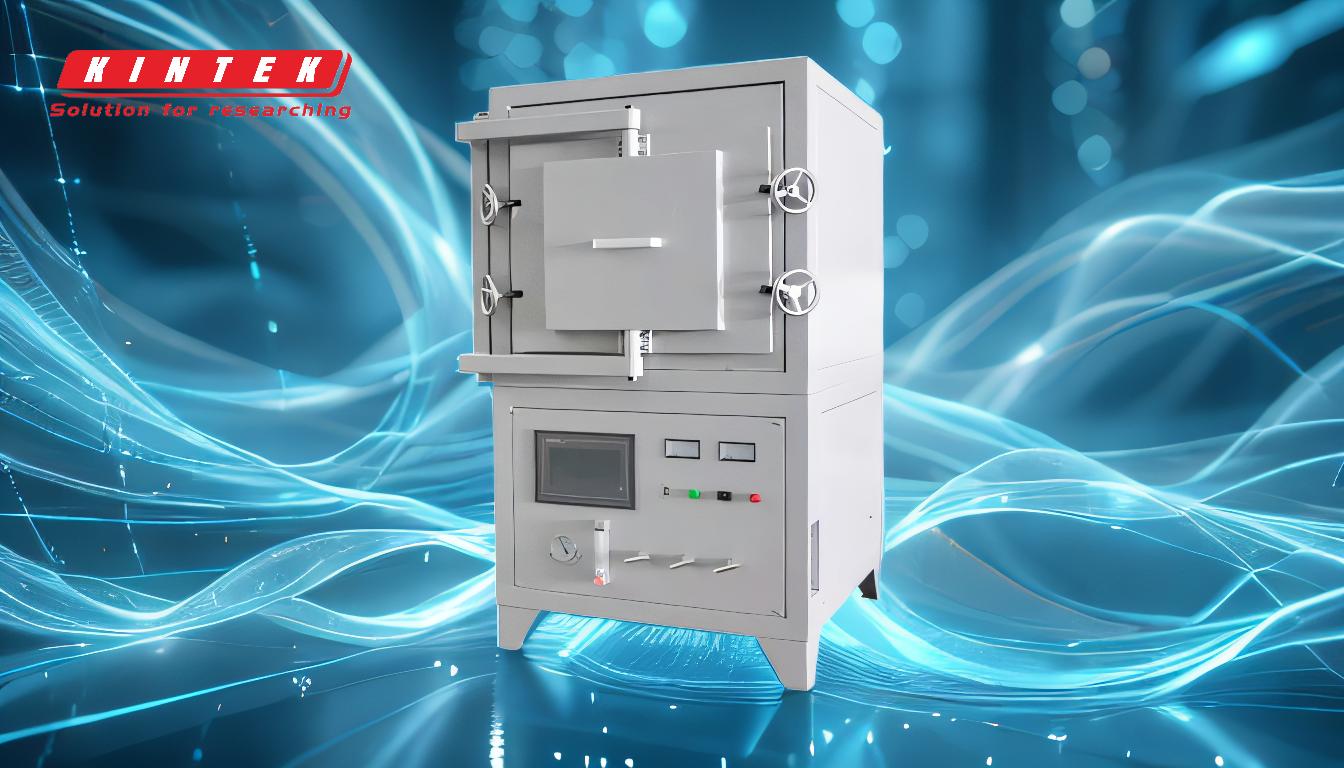
-
Definition of a Reducing Atmosphere:
- A reducing atmosphere is one that contains gases capable of donating electrons, thereby reducing the oxidation state of materials within the furnace. Common reducing gases include hydrogen (H₂), carbon monoxide (CO), and dissociated ammonia (NH₃).
- The goal is to prevent oxidation and promote reduction reactions, which are critical in processes like metal processing, ceramic sintering, and glass manufacturing.
-
Methods to Create a Reducing Atmosphere:
-
Combustion Products:
- By adjusting the ratio of fuel (e.g., natural gas) to air, you can produce combustion products rich in CO and low in CO₂. This creates a reducing atmosphere.
- The CO:CO₂ ratio is critical; a higher CO concentration enhances the reducing potential.
-
Dissociated Ammonia:
- Ammonia (NH₃) can be thermally dissociated into nitrogen (N₂) and hydrogen (H₂). The resulting H₂ acts as a strong reducing agent.
- This method is commonly used in metal heat treatment processes.
-
Pure Gas Blending:
- Direct mixing of pure gases like H₂, N₂, and Ar allows for precise control over the furnace atmosphere.
- This method is often used in modern systems where high purity and consistency are required.
-
Vacuum Atmospheres:
- In some cases, a vacuum environment is used to eliminate oxygen and create a reducing atmosphere.
- This is particularly useful in processes where contamination must be minimized.
-
Combustion Products:
-
Control Mechanisms:
-
Dew Point Analysis:
- Monitoring the dew point (the temperature at which water vapor condenses) helps control the moisture content in the furnace atmosphere.
- Lower dew points indicate a drier atmosphere, which is essential for reducing conditions.
-
Infrared Analyzers:
- These devices measure the concentration of specific gases like CO, CO₂, and H₂O in real-time.
- They provide accurate feedback for adjusting the gas mixture to maintain the desired reducing atmosphere.
-
Oxygen Probes:
- Oxygen probes measure the partial pressure of oxygen in the furnace atmosphere.
- Low oxygen levels are indicative of a reducing environment.
-
Flow and Pressure Control:
- Regulating the flow rates and pressures of incoming gases ensures a consistent atmosphere.
- Mass flow controllers and pressure regulators are commonly used for this purpose.
-
Dew Point Analysis:
-
Equipment and Techniques:
-
Muffle Furnaces:
- A muffle separates the process material from the combustion chamber, allowing for precise control of the atmosphere.
- For reducing atmospheres, the muffle may include a flame curtain or purge chamber to prevent oxygen ingress.
-
Gas Generators:
- Historically, exothermic and endothermic gas generators were used to produce reducing atmospheres.
- Modern systems often rely on on-site generation of pure gases or direct blending by industrial gas providers.
-
Pulse Control Systems:
- These systems maintain a fixed ratio of fuel and air, ensuring consistent temperatures and reducing conditions throughout the process cycle.
-
Muffle Furnaces:
-
Testing and Monitoring:
-
Shim Analysis:
- This involves measuring the weight change of a metal shim exposed to the furnace atmosphere.
- Controlled burning of the shim can also provide insights into the reducing potential of the atmosphere.
-
Multiple Gas Analyzers:
- Using a combination of dew point, oxygen probe, and infrared analyzers provides a comprehensive snapshot of the furnace atmosphere.
- This multi-method approach ensures accuracy and reliability.
-
Shim Analysis:
-
Applications and Considerations:
-
Metal Processing:
- Reducing atmospheres are crucial for processes like annealing, brazing, and sintering, where oxidation must be minimized.
-
Ceramics and Glass:
- In these industries, reducing atmospheres help achieve specific material properties and finishes.
-
Cost and Efficiency:
- The choice of method depends on the required level of control, the scale of the operation, and cost considerations.
- Advanced systems like pulse control and gas blending offer high precision but may involve higher initial costs.
-
Metal Processing:
By carefully selecting and controlling the furnace atmosphere, manufacturers can achieve the desired reducing conditions, ensuring high-quality results in various industrial processes.
Summary Table:
Key Aspect | Details |
---|---|
Definition | Atmosphere with gases like H₂, CO, and NH₃ to reduce oxidation states. |
Methods | Combustion products, dissociated ammonia, pure gas blending, vacuum systems. |
Control Mechanisms | Dew point analysis, infrared analyzers, oxygen probes, flow/pressure control. |
Equipment | Muffle furnaces, gas generators, pulse control systems. |
Applications | Metal processing (annealing, brazing), ceramics, and glass manufacturing. |
Testing & Monitoring | Shim analysis, multiple gas analyzers for accuracy. |
Optimize your furnace processes with a reducing atmosphere—contact our experts today for tailored solutions!