A CVD (Chemical Vapor Deposition) reactor is a sophisticated system designed to deposit thin films of materials onto a substrate through chemical reactions in the vapor phase. The process involves several key steps: feeding precursor gases into the reactor, transporting these gases to the substrate, ensuring they react on the substrate surface, and removing by-products. The reactor consists of components such as gas delivery systems, a reaction chamber, heating sources, vacuum systems, and exhaust treatment systems. The process is highly controlled, with parameters like temperature, pressure, and gas flow rates being carefully monitored to ensure the desired film properties are achieved.
Key Points Explained:
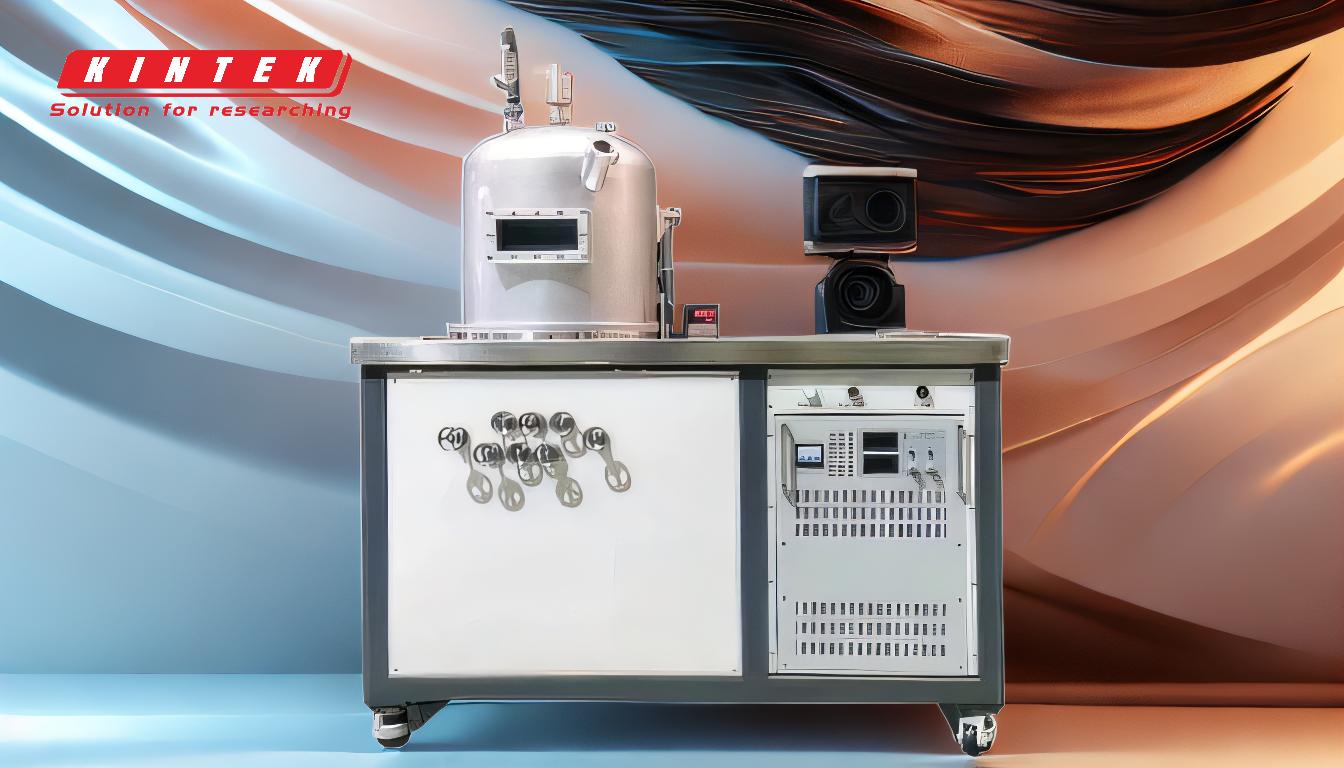
-
Introduction to CVD Reactors:
- CVD reactors are used to deposit thin films of materials onto substrates through chemical reactions in the vapor phase.
- The process is widely used in industries such as semiconductor manufacturing, coatings, and nanotechnology.
-
Components of a CVD Reactor:
- Gas Delivery System: Supplies precursor gases to the reactor chamber. These gases are often controlled by mass flow controllers to ensure precise flow rates.
- Reactor Chamber: The main area where the deposition takes place. It typically includes a quartz tube to hold the substrate.
- Heating Source: Provides the necessary heat to vaporize the precursor gases and facilitate the chemical reactions on the substrate surface.
- Vacuum System: Removes unwanted gaseous species and helps maintain the required pressure within the chamber.
- Exhaust System: Treats and removes volatile by-products, often including harmful gases, to ensure safety and environmental compliance.
- Process Control Equipment: Monitors and controls key parameters like temperature, pressure, and gas flow rates to ensure optimal deposition conditions.
-
Key Steps in the CVD Process:
- Feeding Precursor Chemicals: Precursor gases are introduced into the reactor chamber. These gases are chosen based on the desired film material.
- Transporting Precursor Molecules: The gases are transported to the substrate surface through fluid transport and diffusion.
- Surface Reaction: The precursor molecules react on the substrate surface, forming the desired thin film.
- Desorption of By-Products: By-product molecules are desorbed from the surface to make room for more incoming precursor molecules, ensuring continuous deposition.
-
Chemical Reactions in CVD:
- The CVD process involves several types of chemical reactions, including decomposition, gas combination, hydrolysis, oxidation, and reduction.
- These reactions result in the deposition of the desired material in either crystalline or amorphous form on the substrate.
-
Plasma-Enhanced CVD (PECVD):
- In some CVD systems, plasma is used to enhance the deposition process. A high-frequency voltage is applied to parallel plate electrodes, creating a glow discharge.
- The substrate is placed on the grounded electrode, and the reaction gas is supplied from the opposite plate, forming a uniform film.
- This method is particularly useful for depositing materials like carbon nanotubes (CNTs) on catalytic metal particles.
-
Control and Monitoring:
- The CVD process is highly controlled, with parameters such as temperature, pressure, and gas flow rates being continuously monitored.
- Advanced process control equipment ensures that the deposition conditions remain stable, leading to consistent film quality.
-
Applications of CVD Reactors:
- CVD reactors are used in a wide range of applications, including the production of semiconductor devices, coatings for wear resistance, and the synthesis of nanomaterials like carbon nanotubes.
- The ability to deposit thin films with precise control over thickness, composition, and structure makes CVD reactors indispensable in modern manufacturing and research.
In summary, a CVD reactor is a complex system that relies on precise control of chemical reactions in the vapor phase to deposit thin films onto substrates. The process involves multiple steps and components, each playing a critical role in ensuring the desired film properties are achieved. The versatility and precision of CVD reactors make them essential tools in various high-tech industries.
Summary Table:
Key Aspect | Details |
---|---|
Purpose | Deposits thin films on substrates via chemical reactions in the vapor phase. |
Components | Gas delivery system, reactor chamber, heating source, vacuum system, exhaust. |
Key Steps | Feeding precursor gases, transporting gases, surface reaction, by-product removal. |
Applications | Semiconductor manufacturing, wear-resistant coatings, nanomaterial synthesis. |
Control Parameters | Temperature, pressure, gas flow rates. |
Interested in enhancing your thin film deposition process? Contact us today to learn more about CVD reactors!