A retort furnace is a specialized heating device designed for processes that require controlled atmospheres or specific environmental conditions. It operates by enclosing the material to be heated within a sealed chamber (the retort), which can be either horizontal or vertical in orientation. The furnace uses external heating elements to heat the retort, which then transfers heat to the material inside. This setup allows for precise temperature control and the ability to introduce specific gases or maintain a vacuum, making it ideal for applications like heat treatment, brazing, and sintering. The retort furnace is particularly valued for its ability to prevent contamination and oxidation of the materials being processed.
Key Points Explained:
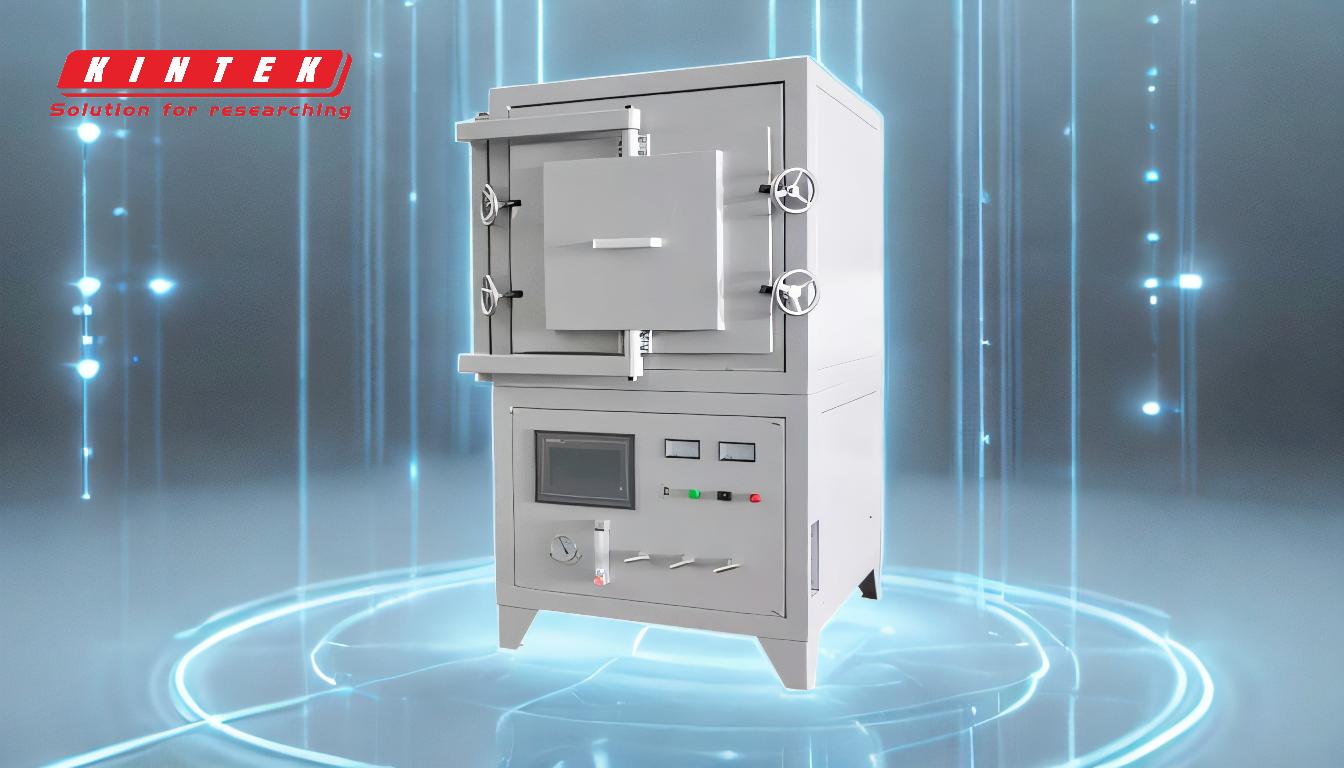
-
Design and Orientation:
- Retort furnaces can be built in either horizontal or vertical configurations, depending on the specific application and space constraints. The horizontal design is often used for continuous processes, while the vertical design is suitable for batch processing.
-
Heating Mechanism:
- The furnace uses external heating elements to generate heat. These elements can be powered by electricity, gas, or other energy sources. The heat is then transferred to the retort, which acts as a sealed chamber to contain the material being processed.
-
Controlled Atmosphere:
- One of the key features of a retort furnace is its ability to maintain a controlled atmosphere within the retort. This can include inert gases, reducing atmospheres, or even a vacuum, depending on the requirements of the process. This controlled environment prevents oxidation, contamination, and other undesirable reactions.
-
Applications:
- Retort furnaces are widely used in industries that require precise heat treatment, such as metallurgy, ceramics, and electronics. Common applications include annealing, brazing, sintering, and hardening of metals and alloys.
-
Temperature Control:
- The furnace is equipped with advanced temperature control systems that allow for precise regulation of heating and cooling rates. This ensures that the material is heated to the exact temperature required for the process and held at that temperature for the necessary duration.
-
Cooling Systems:
- Some retort furnaces are equipped with fast cooling chambers to rapidly cool the material after heating. This is particularly important in processes where controlled cooling rates are critical to achieving the desired material properties.
-
Advantages:
- The sealed retort design minimizes contamination and oxidation, leading to higher quality end products. The ability to control the atmosphere and temperature precisely makes retort furnaces highly versatile and suitable for a wide range of industrial applications.
-
Comparison with Other Furnaces:
- Unlike resistance furnaces, which rely on direct electrical heating, or pusher furnaces, which operate in a continuous manner, retort furnaces focus on creating a controlled environment within a sealed chamber. This makes them uniquely suited for processes that require specific atmospheric conditions.
By understanding these key points, a purchaser can better evaluate whether a retort furnace is the right choice for their specific needs, ensuring optimal performance and quality in their heat treatment processes.
Summary Table:
Aspect | Details |
---|---|
Design & Orientation | Horizontal or vertical configurations for continuous or batch processing. |
Heating Mechanism | External heating elements transfer heat to the sealed retort chamber. |
Controlled Atmosphere | Maintains inert gases, reducing atmospheres, or vacuum to prevent oxidation. |
Applications | Annealing, brazing, sintering, and hardening in metallurgy and ceramics. |
Temperature Control | Advanced systems ensure precise heating and cooling rates. |
Cooling Systems | Fast cooling chambers for controlled post-heating cooling. |
Advantages | Minimizes contamination, oxidation, and ensures high-quality results. |
Ready to enhance your heat treatment processes? Contact us today to find the perfect retort furnace for your needs!