A sputtering machine is a sophisticated tool used in thin-film deposition, particularly in industries like optical media manufacturing, semiconductors, and coatings. It operates by using a plasma, typically of a noble gas like argon, to bombard a solid target material, causing atoms to be ejected and deposited onto a substrate. This process occurs in a vacuum environment, ensuring precise control over the deposition. Sputtering is highly flexible, works at relatively low temperatures, and is ideal for depositing compounds or mixtures with varying evaporation rates. It offers excellent thickness control, conformal step coverage, and the ability to produce films with specific properties like reflectivity or electrical resistivity.
Key Points Explained:
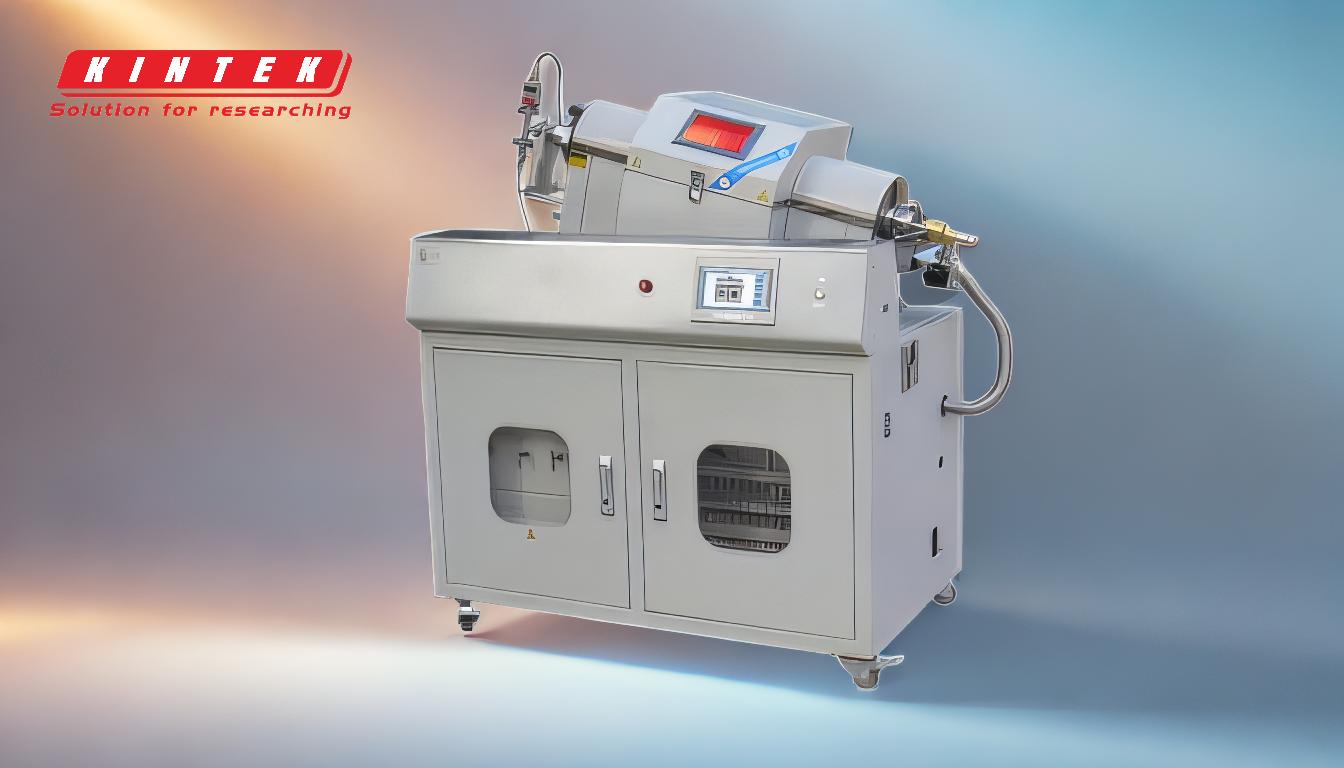
-
Basic Principle of Sputtering:
- Sputtering involves the ejection of atoms or molecules from a solid target material due to bombardment by high-energy ions, usually from a plasma of noble gases like argon. The kinetic energy from these ions is transferred to the target atoms, causing them to overcome their binding energy and be ejected into the gas phase.
- These ejected atoms are then deposited onto a substrate, forming a thin film with specific properties.
-
Role of Plasma and Vacuum Environment:
- A plasma, typically generated from argon gas, is essential for creating the high-energy ions needed for sputtering. The process occurs in a vacuum chamber to prevent contamination and ensure precise control over the deposition.
- The vacuum environment also helps manage the heat generated during the process, as sputtering does not rely on evaporation and can operate at relatively low temperatures.
-
Target and Substrate Interaction:
- The target is the solid material from which atoms are ejected. It is typically made of the material intended for deposition, such as metals, alloys, or compounds.
- The substrate is the surface onto which the ejected atoms are deposited. Common substrates include silicon wafers, glass, or plastics, depending on the application.
-
Deposition Process:
- The ejected atoms from the target travel through the vacuum chamber and deposit onto the substrate. This process is highly controllable, allowing for precise thickness and uniformity of the deposited film.
- The deposited atoms nucleate and form a film with specific properties, such as reflectivity, electrical resistivity, or ionic resistivity, depending on the application.
-
Advantages of Sputtering:
- Low Temperature Operation: Unlike evaporation techniques, sputtering does not require high temperatures, making it suitable for temperature-sensitive substrates.
- Flexibility: It can deposit a wide range of materials, including compounds and mixtures, without issues related to differing evaporation rates.
- Conformal Coverage: Sputtering provides excellent step coverage, ensuring uniform deposition even on complex geometries.
- Precision: The process allows for precise control over film thickness, morphology, grain size, and density.
-
Applications of Sputtering:
- Optical Media: Sputtering is widely used in the manufacturing of CDs, DVDs, and Blu-ray discs, where precise and uniform coatings are essential.
- Semiconductors: It is a key process in the fabrication of semiconductor devices, where thin films with specific electrical properties are required.
- Coatings: Sputtering is used to apply protective or functional coatings on various materials, enhancing their properties like hardness, wear resistance, or reflectivity.
-
Types of Sputtering:
- DC Sputtering: Uses a direct current (DC) power supply to generate the plasma. It is commonly used for conductive materials.
- RF Sputtering: Uses radio frequency (RF) power to sputter non-conductive materials.
- Magnetron Sputtering: Incorporates magnetic fields to enhance the efficiency of the sputtering process, allowing for higher deposition rates and better film quality.
-
Challenges and Considerations:
- Heat Management: Although sputtering operates at lower temperatures than evaporation, the process still generates heat, which must be managed to avoid damaging the substrate or target.
- Target Erosion: Continuous bombardment of the target can lead to erosion, requiring periodic replacement or maintenance.
- Cost: Sputtering equipment and targets can be expensive, making it less suitable for low-budget applications.
In summary, sputtering is a versatile and precise deposition technique that leverages plasma and vacuum environments to create high-quality thin films. Its ability to operate at low temperatures, deposit a wide range of materials, and provide excellent control over film properties makes it indispensable in industries like optical media, semiconductors, and coatings.
Summary Table:
Aspect | Details |
---|---|
Basic Principle | Ejection of target atoms via plasma bombardment, depositing onto a substrate. |
Key Components | Plasma (argon gas), target material, vacuum chamber, and substrate. |
Advantages | Low temperature operation, flexibility, conformal coverage, and precision. |
Applications | Optical media, semiconductors, and protective coatings. |
Types of Sputtering | DC, RF, and magnetron sputtering. |
Challenges | Heat management, target erosion, and high equipment costs. |
Discover how sputtering can enhance your manufacturing process—contact our experts today!