Sputtering is a physical vapor deposition (PVD) technique used to deposit thin films of materials onto substrates. It involves creating a vacuum in a chamber, introducing an inert gas (usually argon), and ionizing the gas to form a plasma. High-energy ions from the plasma collide with a target material, ejecting atoms that then deposit onto a substrate to form a thin, uniform film. This process is widely used in industries such as semiconductors, optics, and coatings due to its ability to produce high-quality, consistent films, even for materials with high melting points or complex compositions.
Key Points Explained:
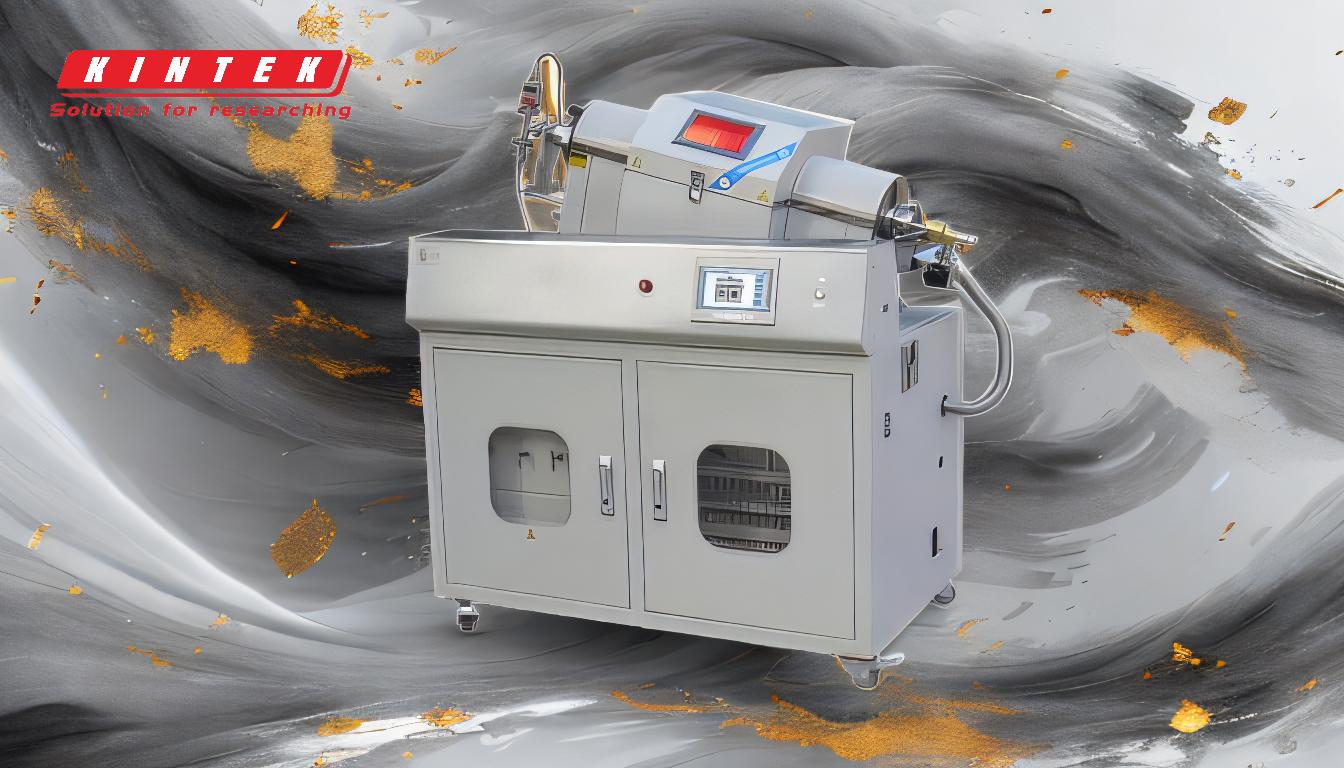
-
Vacuum Creation and Gas Introduction:
- The first step in sputtering is to create a vacuum in the reaction chamber, typically reducing the pressure to around 1 Pa. This removes moisture and impurities, ensuring a clean environment for deposition.
- An inert gas, usually argon, is then introduced into the chamber. Argon is preferred because it is chemically inert and readily ionized, making it ideal for creating a plasma.
-
Plasma Formation and Ionization:
- A high voltage is applied to ionize the argon gas, creating a plasma. The plasma consists of positively charged argon ions and free electrons.
- The ionization process is crucial for generating the high-energy ions needed to bombard the target material.
-
Target Bombardment and Sputtering:
- The target material, which is the source of the atoms to be deposited, is negatively charged. This attracts the positively charged argon ions, which collide with the target at high speeds.
- These collisions eject atoms from the target material in a process known as sputtering. The ejected atoms travel through the chamber and deposit onto the substrate.
-
Film Deposition on Substrate:
- The sputtered atoms traverse the vacuum chamber and land on the substrate, forming a thin film. Due to the low pressure and the nature of the sputtering process, the deposited film is highly uniform in thickness and composition.
- This uniformity is one of the key advantages of sputtering, making it suitable for applications requiring precise and consistent coatings.
-
Magnetron Sputtering:
- In magnetron sputtering, a magnetic field is applied to increase the efficiency of the process. The magnetic field confines the plasma near the target, increasing the density of ions and enhancing the sputtering rate.
- This method is particularly effective for depositing films on nonmetallic substrates, as it allows for better control over the deposition process.
-
Reactive Sputtering:
- Reactive sputtering involves introducing a reactive gas, such as oxygen or nitrogen, into the chamber along with the inert gas. The reactive gas chemically reacts with the sputtered atoms from the target, forming compound films (e.g., oxides or nitrides) on the substrate.
- This technique is useful for depositing materials that are difficult to produce using other methods, such as certain alloys or compounds.
-
Applications and Advantages:
- Sputtering is widely used in the semiconductor industry for depositing thin films of metals, alloys, and compounds onto silicon wafers.
- It is also used in the production of optical coatings, hard coatings for tools, and decorative coatings.
- The ability to deposit materials with high melting points and complex compositions makes sputtering a versatile and valuable technique in materials science and engineering.
By understanding these key points, one can appreciate the complexity and precision involved in the sputtering process, as well as its importance in modern manufacturing and technology.
Summary Table:
Step | Description |
---|---|
1. Vacuum Creation | A vacuum is created in the chamber to remove impurities and moisture. |
2. Gas Introduction | Inert gas (usually argon) is introduced and ionized to form a plasma. |
3. Plasma Formation | High voltage ionizes the gas, creating positively charged argon ions and free electrons. |
4. Target Bombardment | Argon ions collide with the negatively charged target, ejecting atoms. |
5. Film Deposition | Ejected atoms deposit onto the substrate, forming a thin, uniform film. |
6. Magnetron Sputtering | A magnetic field enhances plasma density, improving sputtering efficiency. |
7. Reactive Sputtering | Reactive gases (e.g., oxygen or nitrogen) are added to form compound films. |
Need a sputtering system for your lab or industry? Contact us today to learn more!