An Inductotherm induction furnace operates on the principle of electromagnetic induction to heat and melt metals. It converts three-phase power frequency alternating current into direct current, which is then transformed into an adjustable medium-frequency current. This current flows through a capacitor and an induction coil, generating high-density magnetic lines of force. These magnetic lines cut through the metal material inside the induction coil, inducing large eddy currents. The eddy currents, having medium-frequency properties, cause the free electrons in the metal to flow, generating heat through resistance. This process is highly efficient, precise, and widely used in industries for melting, heating, and heat treatment of metals.
Key Points Explained:
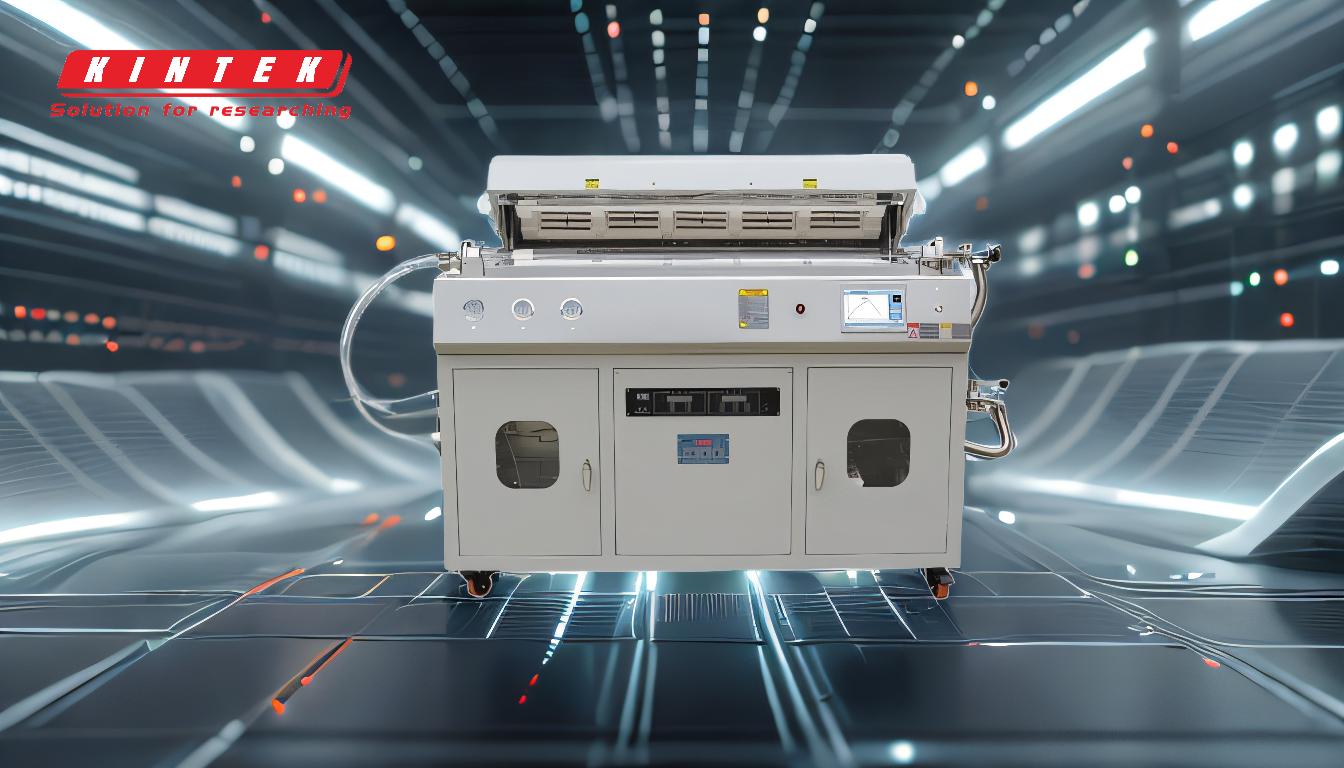
-
Power Conversion:
- The furnace starts by converting three-phase power frequency alternating current (AC) into direct current (DC). This conversion is typically achieved using a rectifier circuit.
- The DC is then inverted back into an adjustable medium-frequency AC using advanced power electronics, such as IGBT (Insulated Gate Bipolar Transistor) technology. This step is crucial for controlling the frequency and intensity of the current.
-
Induction Coil and Capacitor:
- The medium-frequency AC flows through a capacitor and an induction coil. The capacitor helps in tuning the circuit to the desired frequency, ensuring efficient energy transfer.
- The induction coil, often made of copper, generates a high-density magnetic field when the current passes through it.
-
Magnetic Field and Eddy Currents:
- The magnetic lines of force generated by the induction coil cut through the metal material placed inside the coil. This induces eddy currents within the metal.
- Eddy currents are loops of electrical current induced within conductors by a changing magnetic field. These currents have the same frequency as the applied medium-frequency AC.
-
Heat Generation:
- The eddy currents cause the free electrons in the metal to move, generating heat due to the electrical resistance of the metal. This process is known as Joule heating.
- The heat generated is proportional to the square of the current and the resistance of the metal, making it highly efficient for melting and heating applications.
-
Advantages of Medium Frequency:
- Medium frequency induction furnaces offer precise temperature control, rapid heating, and uniform heat distribution.
- They are energy-efficient, as the heat is generated directly within the metal, minimizing heat loss.
- The use of IGBT technology enhances the efficiency and reliability of the furnace, allowing for smoother operation and better control over the heating process.
-
Applications:
- Inductotherm induction furnaces are widely used in foundries for melting metals such as steel, iron, aluminum, and copper.
- They are also used in heat treatment processes, where precise temperature control is essential for achieving desired material properties.
By understanding these key points, one can appreciate the efficiency and precision of the Inductotherm induction furnace, making it a vital tool in modern metallurgical processes.
Summary Table:
Key Component | Function |
---|---|
Power Conversion | Converts AC to DC, then to adjustable medium-frequency AC using IGBT tech. |
Induction Coil & Capacitor | Generates a high-density magnetic field for efficient energy transfer. |
Magnetic Field | Induces eddy currents in the metal, causing heat generation via resistance. |
Heat Generation | Joule heating from eddy currents ensures rapid, uniform heating. |
Advantages | Precise control, energy efficiency, and minimal heat loss. |
Applications | Melting and heat treatment of metals like steel, iron, aluminum, and copper. |
Unlock the potential of Inductotherm induction furnaces for your operations—contact us today to learn more!