Arc melting is a highly efficient metallurgical process that utilizes an electric arc to generate extreme heat, melting metals without altering their chemical properties. This method is commonly used in industrial settings for melting scrap steel and other metals. The process relies on an electric arc, a self-sustaining discharge phenomenon, created by converting high voltage into low voltage and high current. The arc is maintained between electrodes or between an electrode and the material to be melted, producing temperatures high enough to melt the metal. This technique is widely employed due to its precision, energy efficiency, and ability to handle large volumes of material.
Key Points Explained:
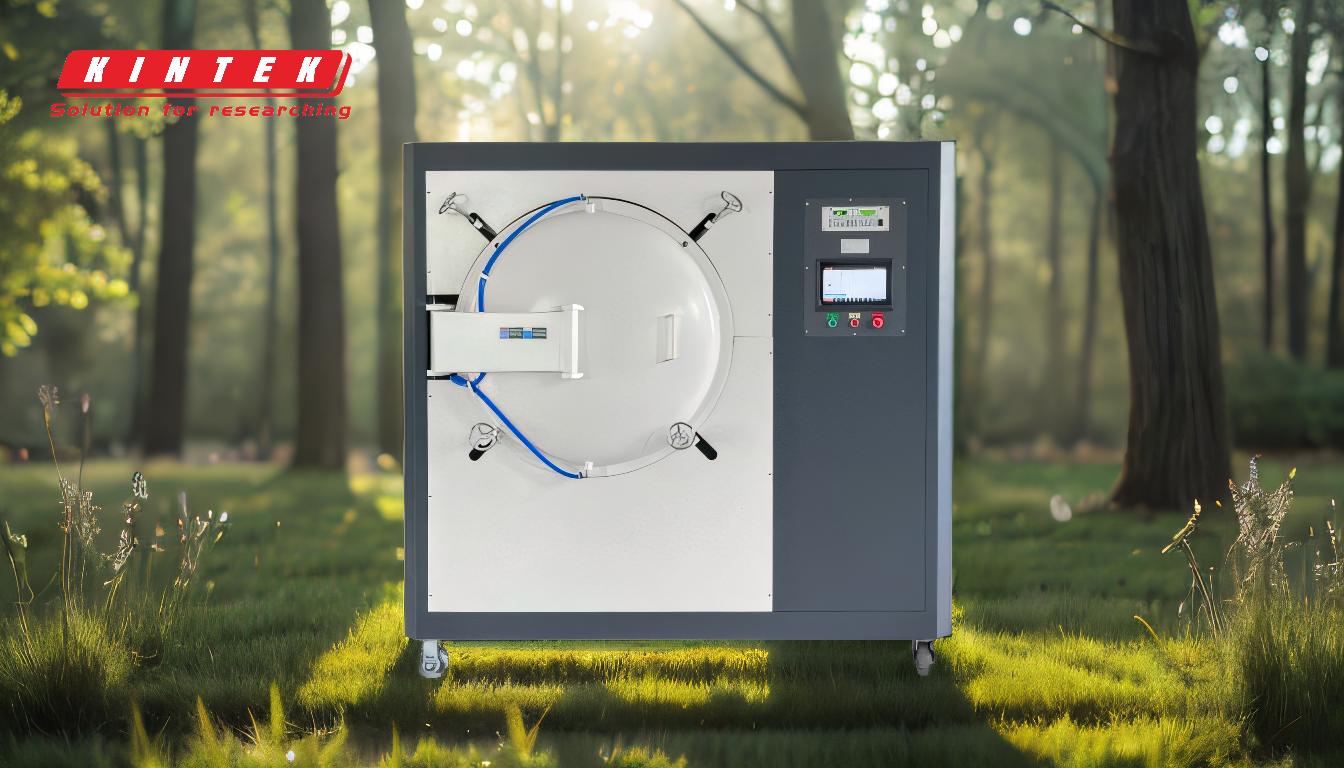
-
Definition and Purpose of Arc Melting
- Arc melting is an electrothermal metallurgical process that uses electric energy to create an electric arc, which generates enough heat to melt metals.
- The primary purpose is to melt metals, such as scrap steel, while preserving their chemical properties. This makes it ideal for recycling and refining metals without introducing impurities.
-
Components of an Arc Melting Furnace
- The main component is the electric welder, which converts standard voltages (220V or 380V) into low voltage and high current.
- The furnace includes electrodes (positive and negative poles) and a chamber where the material to be melted is placed.
- The arc is created by the instantaneous short circuit between the electrodes or between an electrode and the material.
-
How the Electric Arc is Generated
- The electric arc is a self-sustaining discharge phenomenon, meaning it maintains stable combustion without extinguishing.
- It is triggered by the short circuit between the positive and negative poles, which ionizes the air or gas between them, creating a plasma state.
- This plasma arc reaches temperatures high enough to melt most metals, typically ranging from 3,000°C to 20,000°C.
-
Process of Melting Metals
- Once the arc is established, it transfers heat to the charged material (e.g., scrap steel) placed in the furnace.
- The intense heat causes the metal to melt, forming a molten pool.
- The molten metal can then be poured into molds or further processed for refining.
-
Advantages of Arc Melting
- Energy Efficiency: The direct application of heat to the material minimizes energy loss.
- Precision: The process allows for controlled melting, ensuring the metal's chemical composition remains unchanged.
- Versatility: It can handle a wide range of metals and alloys, making it suitable for various industrial applications.
- Scalability: Arc melting furnaces can be designed for small-scale laboratory use or large-scale industrial operations.
-
Applications of Arc Melting
- Metal Recycling: Commonly used to melt scrap steel and other metals for recycling purposes.
- Alloy Production: Ideal for creating alloys with precise chemical compositions.
- Research and Development: Used in laboratories to study the properties of metals and develop new materials.
- Industrial Manufacturing: Employed in industries such as automotive, aerospace, and construction for producing high-quality metal components.
-
Safety and Operational Considerations
- The high temperatures and electrical currents involved require robust safety measures, including protective gear and proper insulation.
- The furnace must be operated in a controlled environment to prevent accidents and ensure consistent performance.
- Regular maintenance of the electrodes and other components is essential to maintain efficiency and prevent breakdowns.
By understanding these key points, equipment and consumable purchasers can make informed decisions about the suitability of arc melting technology for their specific needs, ensuring optimal performance and cost-effectiveness.
Summary Table:
Aspect | Details |
---|---|
Definition | Electrothermal process using an electric arc to melt metals. |
Key Components | Electric welder, electrodes, and a melting chamber. |
Temperature Range | 3,000°C to 20,000°C. |
Advantages | Energy efficiency, precision, versatility, and scalability. |
Applications | Metal recycling, alloy production, R&D, and industrial manufacturing. |
Safety Considerations | Requires protective gear, insulation, and regular maintenance. |
Ready to optimize your metal processing with arc melting? Contact our experts today for tailored solutions!