When comparing argon and nitrogen cooling in vacuum furnaces, it's essential to consider their cooling efficiency, cost, and impact on the quality of treated parts. Both gases are commonly used in vacuum furnaces for cooling, but they have distinct properties that influence their performance and suitability for different applications. Below, we delve into the key aspects of argon and nitrogen cooling, providing a comprehensive comparison to help equipment or consumable purchasers make informed decisions.
Key Points Explained:
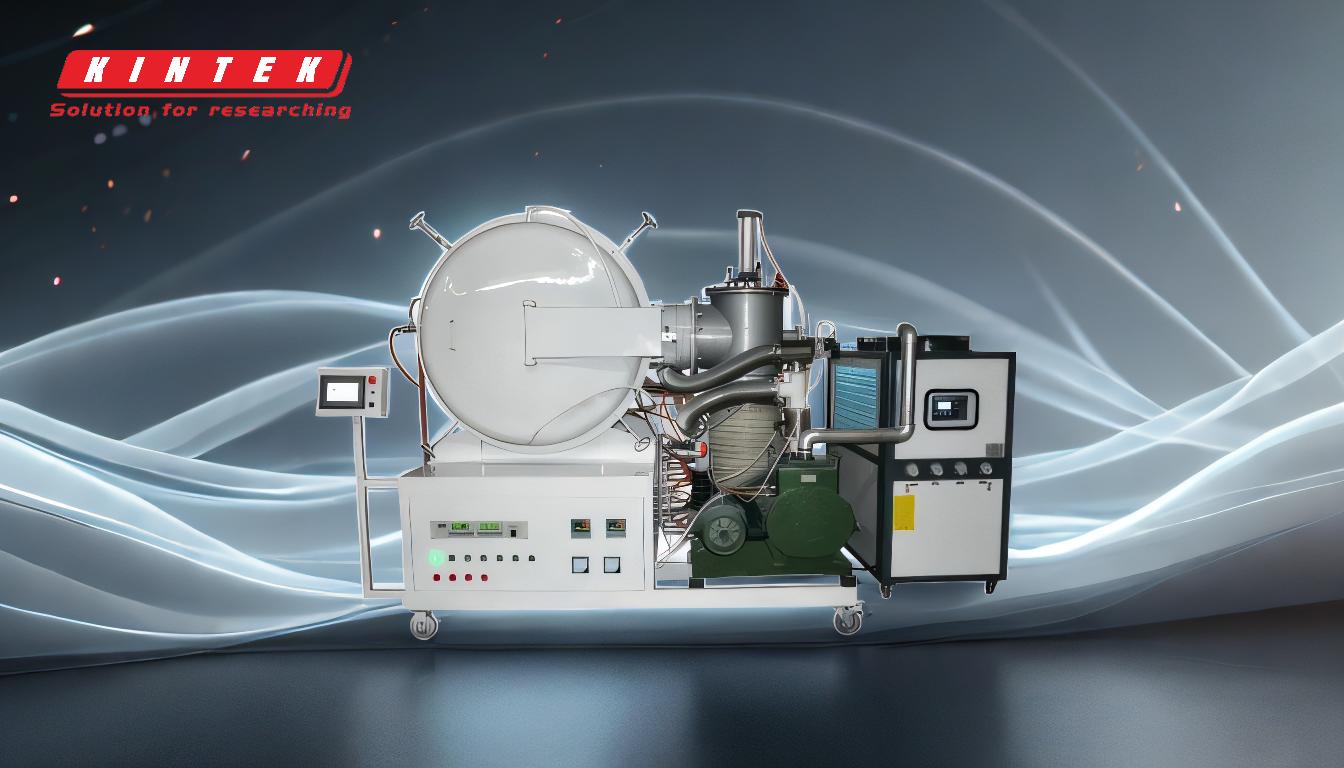
-
Cooling Efficiency:
- Argon: Argon is an inert gas, which means it does not react with the materials being treated. This property makes it highly effective for cooling sensitive materials that require a non-reactive environment. Argon's cooling efficiency is also influenced by its thermal conductivity, which is lower than nitrogen. This can result in slower cooling rates, which might be desirable for certain heat treatment processes where controlled cooling is necessary to prevent material distortion or cracking.
- Nitrogen: Nitrogen, on the other hand, has a higher thermal conductivity compared to argon, allowing for faster cooling rates. This can be advantageous for processes that require rapid cooling to achieve specific material properties. However, nitrogen is not entirely inert and can react with certain materials at high temperatures, potentially leading to surface oxidation or nitriding, which might affect the quality of the treated parts.
-
Cost Considerations:
- Argon: Argon is generally more expensive than nitrogen. Its higher cost is due to its lower abundance in the atmosphere and the more complex extraction process. For operations where cost is a significant factor, the use of argon might be limited to applications where its inert properties are absolutely necessary.
- Nitrogen: Nitrogen is more cost-effective and widely available, making it a popular choice for many vacuum furnace applications. Its lower cost and higher cooling efficiency make it suitable for a broader range of processes, especially where rapid cooling is required.
-
Impact on Material Quality:
- Argon: The inert nature of argon ensures that the surface of treated parts remains clean and free from contamination. This is particularly important for high-precision components where surface integrity is critical. Argon's slower cooling rate can also help in reducing thermal stresses, leading to better dimensional stability and fewer defects in the final product.
- Nitrogen: While nitrogen offers faster cooling, its potential reactivity with certain materials can lead to surface oxidation or nitriding. This might necessitate additional post-treatment processes to restore the surface quality, adding to the overall cost and complexity of the operation. However, for materials that are not sensitive to nitrogen, it can be an effective and economical cooling medium.
-
Application Suitability:
- Argon: Ideal for applications involving sensitive materials such as titanium, zirconium, and certain high-temperature alloys where maintaining a non-reactive environment is crucial. It is also preferred for processes requiring controlled cooling to achieve specific microstructures.
- Nitrogen: Suitable for a wide range of materials, especially those that are not prone to oxidation or nitriding. It is commonly used in processes like hardening, annealing, and brazing, where rapid cooling is beneficial.
-
Operational Considerations:
- Argon: Requires careful handling and storage due to its higher cost and the need to maintain purity. The slower cooling rate might also necessitate longer processing times, impacting overall productivity.
- Nitrogen: Easier to handle and more cost-effective, making it a practical choice for many industrial applications. Its faster cooling rate can enhance throughput, but care must be taken to avoid adverse reactions with sensitive materials.
In conclusion, the choice between argon and nitrogen cooling in vacuum furnaces depends on the specific requirements of the heat treatment process, the materials being treated, and cost considerations. Argon offers superior inertness and controlled cooling, making it ideal for sensitive applications, while nitrogen provides a cost-effective and efficient cooling solution for a broader range of materials and processes. Understanding these differences allows purchasers to select the most appropriate cooling medium for their vacuum furnace operations.
Summary Table:
Aspect | Argon | Nitrogen |
---|---|---|
Cooling Efficiency | Slower cooling due to lower thermal conductivity; ideal for controlled cooling. | Faster cooling due to higher thermal conductivity; suitable for rapid cooling. |
Cost | More expensive due to lower abundance and complex extraction. | Cost-effective and widely available. |
Material Quality | Maintains surface integrity; reduces thermal stress and defects. | May cause oxidation or nitriding; requires post-treatment for sensitive materials. |
Application Suitability | Ideal for sensitive materials like titanium and high-temperature alloys. | Suitable for hardening, annealing, and brazing; not ideal for sensitive materials. |
Operational Considerations | Requires careful handling and storage; slower cooling impacts productivity. | Easier to handle; faster cooling enhances throughput. |
Need help choosing the right cooling gas for your vacuum furnace? Contact our experts today for personalized advice!