Furnace brazing is a precise and controlled process used to join metal components by melting a filler metal (brazing alloy) into the joint without melting the base metals. It is commonly performed in a vacuum brazing furnace to ensure a clean, oxide-free environment, which is critical for achieving strong and reliable joints. The process involves several key steps, including cleaning and preparation of parts, assembly and fixturing, heating in a controlled environment, and post-brazing treatments. The vacuum environment eliminates the need for flux, prevents oxidation, and ensures high-quality results, especially for materials like stainless steel, titanium, and superalloys.
Key Points Explained:
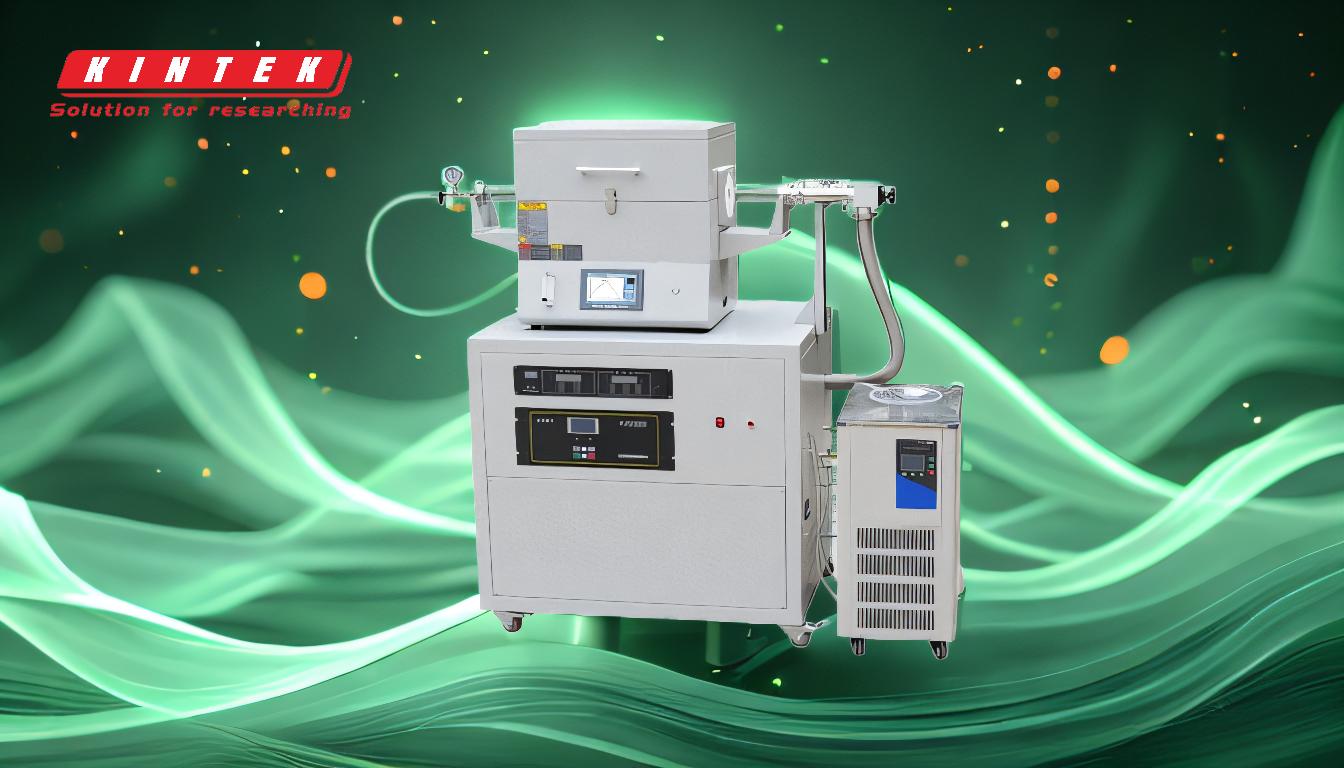
-
Cleaning and Preparation of Parts
- Before brazing, the metal surfaces must be thoroughly cleaned to remove contaminants such as oil, grease, and oxides.
- Cleaning methods include ultrasonic cleaning, vapor degreasing, or chemical etching.
- Proper cleaning ensures optimal wetting and flow of the filler metal, which is essential for strong joint formation.
-
Assembly and Fixturing
- The cleaned parts are assembled and fixtured to maintain precise alignment and spacing during the brazing process.
- Proper joint design and gap width are critical to allow capillary action, which draws the molten filler metal into the joint.
- Fixtures or clamps are often used to hold the parts in place and prevent movement during heating.
-
Heating in a Vacuum Environment
- The assembled parts are placed in a vacuum brazing furnace, where the chamber is evacuated to remove oxygen and other reactive gases.
- The vacuum environment prevents oxidation and eliminates the need for flux, ensuring clean and high-quality joints.
- The furnace is heated to a temperature above the melting point of the filler metal but below the melting point of the base metals.
- The temperature is carefully controlled to ensure uniform heating and proper melting of the filler metal.
-
Cooling and Inspection
- After brazing, the furnace is cooled slowly to room temperature to minimize thermal stress and distortion in the parts.
- The cooling process may involve cycling inert gases like argon into the chamber to prevent oxidation during cooling.
- Once cooled, the parts are removed from the furnace and inspected for quality, including joint integrity and surface finish.
-
Post-Brazing Treatments
- Depending on the application, post-brazing treatments such as heat treatment, machining, or surface finishing may be performed.
- These treatments enhance the mechanical properties, dimensional accuracy, and appearance of the brazed assembly.
-
Advantages of Vacuum Brazing
- The vacuum environment ensures a clean, oxide-free joint, which is particularly important for materials that are prone to oxidation, such as stainless steel, titanium, and superalloys.
- The process is highly repeatable and suitable for complex or delicate assemblies.
- It eliminates the need for flux, reducing the risk of contamination and simplifying post-brazing cleaning.
-
Applications of Furnace Brazing
- Furnace brazing is widely used in industries such as aerospace, automotive, medical devices, and electronics.
- It is ideal for joining components that require high strength, precision, and reliability, such as heat exchangers, turbine blades, and sensors.
By following these steps and leveraging the capabilities of a vacuum brazing furnace, manufacturers can achieve strong, durable, and high-quality brazed joints for a wide range of applications.
Summary Table:
Step | Description |
---|---|
Cleaning and Preparation | Remove contaminants like oil, grease, and oxides using ultrasonic or chemical methods. |
Assembly and Fixturing | Align parts precisely and use fixtures to maintain spacing for capillary action. |
Heating in Vacuum | Heat in a vacuum brazing furnace to prevent oxidation and ensure clean joints. |
Cooling and Inspection | Cool slowly to minimize stress; inspect joints for integrity and surface finish. |
Post-Brazing Treatments | Perform heat treatment, machining, or finishing to enhance properties. |
Advantages | Clean, oxide-free joints; no flux required; ideal for oxidation-prone materials. |
Applications | Aerospace, automotive, medical devices, and electronics industries. |
Discover how furnace brazing can enhance your manufacturing process—contact our experts today!