Heat treatment significantly influences material selection by altering the mechanical properties of metallic alloys, such as hardness, strength, toughness, ductility, and elasticity. This process involves controlling the rate of diffusion and cooling within the metal's microstructure, which can tailor the material to specific applications. While iron and steel are the most commonly heat-treated materials, alloys of aluminum, copper, magnesium, nickel, and titanium can also undergo heat treatment to achieve desired properties. Understanding how heat treatment affects these materials helps in selecting the right alloy for specific engineering or manufacturing needs, ensuring optimal performance and durability.
Key Points Explained:
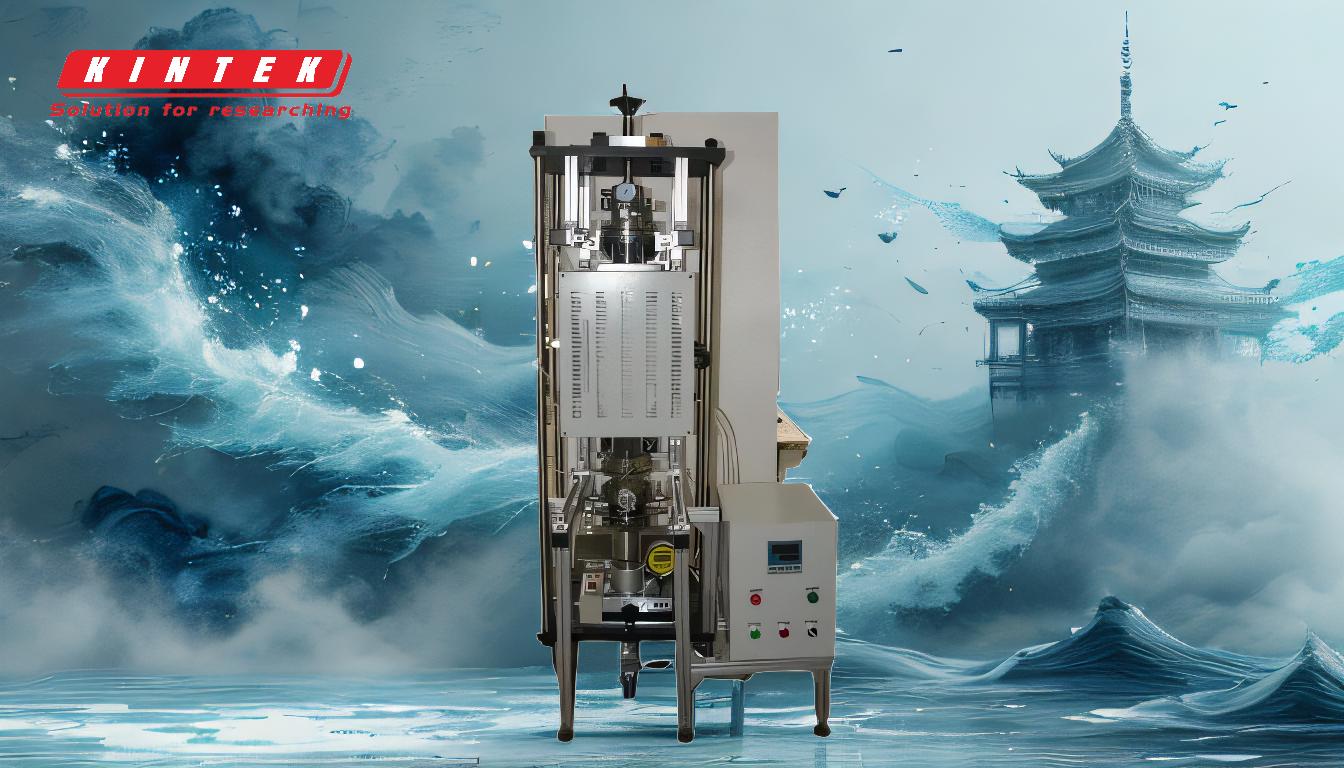
-
Impact on Mechanical Properties:
- Heat treatment modifies key mechanical properties of metallic alloys.
- Hardness: Increased hardness improves wear resistance, making the material suitable for cutting tools or gears.
- Strength: Enhanced strength allows the material to withstand higher loads, ideal for structural applications.
- Toughness: Improved toughness ensures the material can absorb energy without fracturing, critical for impact-resistant components.
- Ductility: Controlled ductility enables the material to deform without breaking, useful in forming or shaping processes.
- Elasticity: Adjusting elasticity ensures the material can return to its original shape after deformation, important for springs or flexible components.
- Heat treatment modifies key mechanical properties of metallic alloys.
-
Mechanism of Heat Treatment:
- Heat treatment works by altering the microstructure of the metal through controlled heating and cooling.
- Rate of Diffusion: Controlling diffusion allows for the redistribution of alloying elements, which influences properties like hardness and strength.
- Rate of Cooling: Faster cooling (quenching) typically increases hardness but may reduce ductility, while slower cooling (annealing) enhances ductility and reduces internal stresses.
- Heat treatment works by altering the microstructure of the metal through controlled heating and cooling.
-
Material Versatility:
- While iron and steel are the most commonly heat-treated materials, other alloys can also benefit from this process.
- Aluminum Alloys: Heat treatment improves strength and corrosion resistance, making them suitable for aerospace and automotive applications.
- Copper Alloys: Enhanced electrical conductivity and strength are achieved, useful in electrical components.
- Magnesium Alloys: Improved strength-to-weight ratio is critical for lightweight applications.
- Nickel Alloys: Increased resistance to high temperatures and corrosion is essential for aerospace and chemical industries.
- Titanium Alloys: Enhanced strength and biocompatibility make them ideal for medical implants and aerospace components.
- While iron and steel are the most commonly heat-treated materials, other alloys can also benefit from this process.
-
Application-Specific Selection:
- The choice of material and heat treatment process depends on the intended application.
- High-Strength Applications: Steel or titanium alloys are often selected and heat-treated for maximum strength.
- Corrosion Resistance: Aluminum or nickel alloys are preferred, with heat treatment enhancing their resistance to environmental factors.
- Lightweight Requirements: Magnesium alloys are chosen, and heat treatment ensures they meet strength and durability standards.
- The choice of material and heat treatment process depends on the intended application.
-
Trade-offs and Considerations:
- Heat treatment involves trade-offs between different properties.
- For example, increasing hardness through quenching may reduce ductility, requiring careful consideration of the application's needs.
- The cost of heat treatment and its impact on material availability must also be factored into the selection process.
- Heat treatment involves trade-offs between different properties.
By understanding how heat treatment affects material properties, engineers and purchasers can make informed decisions to select the most suitable alloy for their specific requirements, balancing performance, cost, and durability.
Summary Table:
Property | Impact of Heat Treatment |
---|---|
Hardness | Increases wear resistance, ideal for cutting tools and gears. |
Strength | Enhances load-bearing capacity, suitable for structural applications. |
Toughness | Improves energy absorption, critical for impact-resistant components. |
Ductility | Enables deformation without breaking, useful in forming processes. |
Elasticity | Ensures material returns to its original shape, important for springs and flexible parts. |
Material Types | Iron, steel, aluminum, copper, magnesium, nickel, and titanium alloys benefit from heat treatment. |
Applications | Aerospace, automotive, electrical, medical implants, and lightweight structures. |
Discover how heat treatment can optimize your material selection—contact our experts today!