An induction furnace operates by using electromagnetic induction to generate heat within a conductive metal, which is then melted. The process involves an induction coil that carries an alternating current, creating a magnetic field. This magnetic field induces eddy currents in the metal, which generate heat through resistance (Joule heating). In ferromagnetic materials, additional heat is produced by magnetic hysteresis. The furnace consists of a nonconductive crucible to hold the metal, surrounded by a copper coil. The alternating current is typically converted from standard power frequency to a higher frequency to improve efficiency. The entire system is designed to ensure that the metal is heated uniformly and efficiently without direct contact between the coil and the metal.
Key Points Explained:
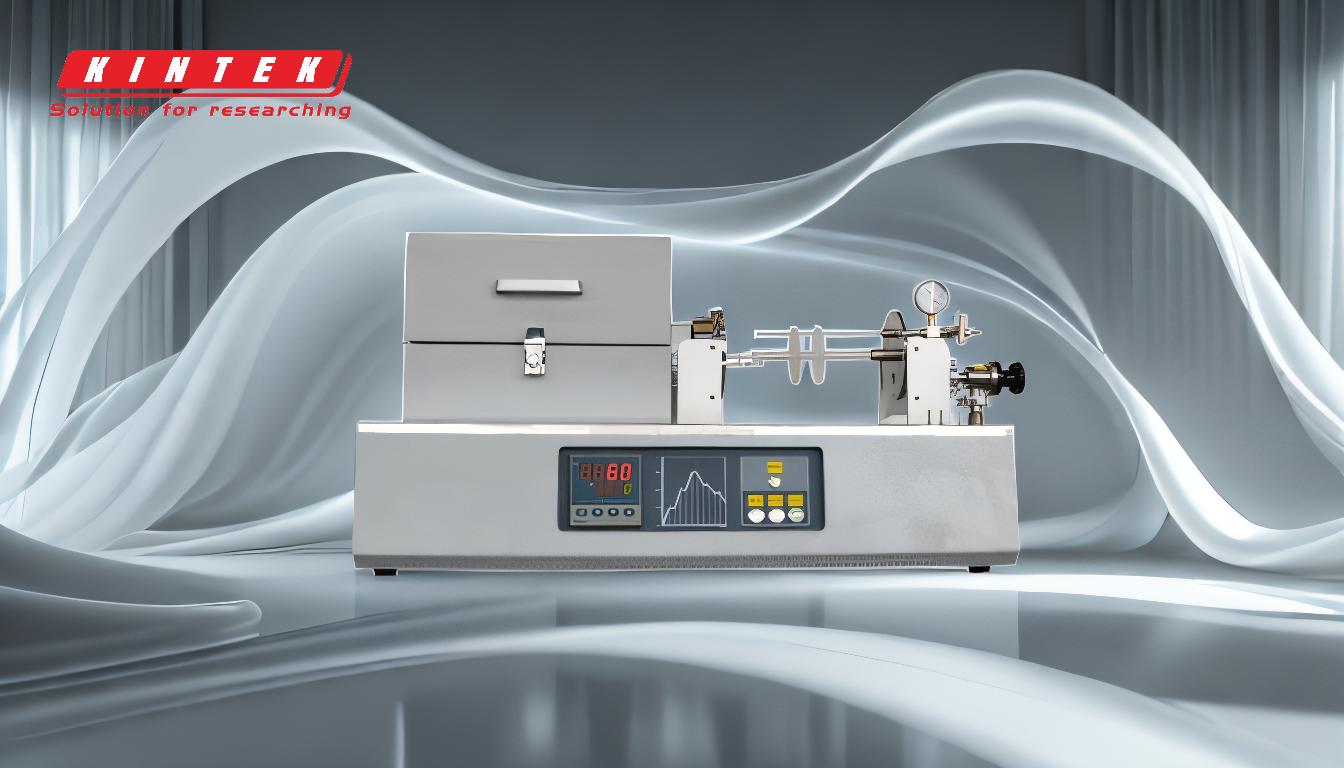
-
Electromagnetic Induction:
- The core principle behind an induction furnace is electromagnetic induction. When an alternating current flows through the induction coil, it generates a magnetic field. This magnetic field penetrates the metal placed inside the crucible, inducing eddy currents within the metal.
-
Eddy Currents and Joule Heating:
- The eddy currents induced in the metal flow in closed loops and encounter resistance, which generates heat due to the Joule effect. This heat is what melts the metal. The amount of heat generated depends on the resistance of the metal and the strength of the eddy currents.
-
Magnetic Hysteresis (for Ferromagnetic Materials):
- In ferromagnetic materials like iron, additional heating occurs due to magnetic hysteresis. As the magnetic field alternates, the magnetic domains within the material constantly realign, which generates heat. This phenomenon contributes to the overall heating process, especially in metals that are magnetic.
-
Induction Coil and Crucible:
- The induction coil is typically made of copper, which is an excellent conductor of electricity. The coil is wound around a nonconductive crucible that holds the metal to be melted. The crucible is designed to withstand high temperatures and is often made of materials like ceramic or graphite.
-
Power Supply and Frequency Conversion:
- The power supply for an induction furnace converts standard power frequency (50 Hz or 60 Hz) into a higher frequency (300 Hz to 1000 Hz). This is done by first converting the alternating current (AC) into direct current (DC) and then back into AC at the desired frequency. Higher frequencies improve the efficiency of the induction process by increasing the rate at which the magnetic field changes, thus inducing stronger eddy currents.
-
Cooling System:
- The induction coil generates a significant amount of heat and must be cooled to prevent damage. This is typically achieved using a water-cooling system, where water circulates through channels in the coil to absorb and dissipate the heat.
-
Non-Contact Heating:
- One of the significant advantages of induction furnaces is that the heating process is non-contact. The induction coil does not touch the metal, which reduces contamination and allows for precise control over the heating process. This is particularly important in applications where purity and consistency are critical, such as in the production of high-quality alloys.
-
Uniform Heating:
- The induction process ensures that the metal is heated uniformly. The eddy currents are distributed throughout the metal, leading to consistent heating and melting. This uniformity is crucial for achieving the desired metallurgical properties in the final product.
-
Applications of Induction Furnaces:
- Induction furnaces are widely used in the metalworking industry for melting and refining metals such as steel, iron, copper, aluminum, and precious metals. They are also used in foundries for casting and in the production of high-purity materials for specialized applications.
-
Advantages Over Other Furnace Types:
- Induction furnaces offer several advantages over traditional furnaces, such as faster heating rates, better energy efficiency, and the ability to produce cleaner melts with minimal oxidation. They also allow for precise temperature control, which is essential for producing high-quality metal products.
By understanding these key points, one can appreciate the sophisticated engineering and physics behind the operation of an induction furnace. This technology has revolutionized the metalworking industry by providing a clean, efficient, and precise method for melting and refining metals.
Summary Table:
Key Aspect | Description |
---|---|
Electromagnetic Induction | Alternating current creates a magnetic field, inducing eddy currents in the metal. |
Eddy Currents & Joule Heating | Eddy currents generate heat through resistance, melting the metal. |
Magnetic Hysteresis | Additional heat in ferromagnetic materials due to magnetic domain realignment. |
Induction Coil & Crucible | Copper coil surrounds a nonconductive crucible for high-temperature melting. |
Power Supply | Converts standard frequency to higher frequencies for improved efficiency. |
Cooling System | Water-cooling system prevents coil overheating. |
Non-Contact Heating | No direct contact between coil and metal, reducing contamination. |
Uniform Heating | Ensures consistent melting for high-quality metallurgical properties. |
Applications | Used for melting steel, iron, copper, aluminum, and precious metals. |
Advantages | Faster heating, energy efficiency, precise temperature control, and cleaner melts. |
Discover how an induction furnace can revolutionize your metalworking process—contact us today for expert advice!