Induction heating on a stove works by using electromagnetic induction to generate heat directly in the cookware. An induction coil beneath the stove's surface carries an alternating current, creating a rapidly changing magnetic field. When a ferromagnetic cookware (like iron or steel) is placed on the stove, the magnetic field induces eddy currents within the cookware. These currents encounter resistance in the metal, generating heat through the Joule effect. This heat is then transferred to the food through conduction. Induction cooking is efficient, fast, and safe, as the cooktop itself remains relatively cool, and only the cookware heats up. However, it requires cookware with magnetic properties, making non-ferrous materials like aluminum or copper unsuitable unless they have a magnetic base.
Key Points Explained:
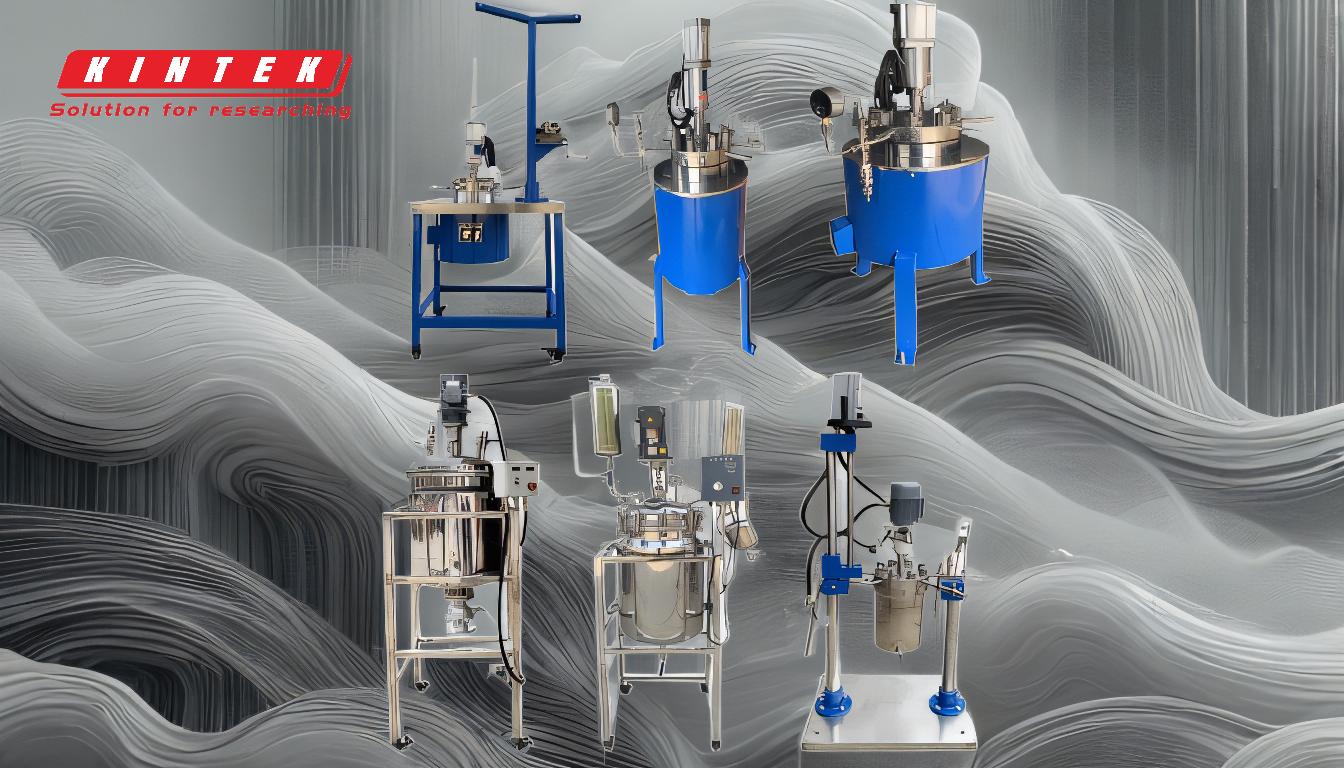
-
Electromagnetic Induction:
- Induction heating relies on the principle of electromagnetic induction, where a changing magnetic field induces an electric current in a conductor.
- In an induction stove, an alternating current flows through a coil beneath the cooking surface, creating a rapidly oscillating magnetic field.
-
Eddy Currents:
- When a ferromagnetic cookware (such as iron or steel) is placed on the stove, the magnetic field induces eddy currents within the cookware.
- These eddy currents are loops of electrical current that flow within the metal due to the changing magnetic field.
-
Joule Heating:
- As the eddy currents flow through the metal, they encounter resistance, which generates heat through the Joule effect (also known as resistive heating).
- The heat is produced directly within the cookware, making the process highly efficient.
-
Heat Transfer:
- The heat generated in the cookware is then transferred to the food through conduction.
- Since the heat is generated directly in the cookware, the cooking surface remains relatively cool, reducing the risk of burns and making the stove safer to use.
-
Cookware Requirements:
- Induction stoves require cookware made from ferromagnetic materials, such as cast iron or certain types of stainless steel.
- Non-ferrous materials like aluminum or copper are generally unsuitable unless they have a magnetic base layer.
-
Advantages of Induction Cooking:
- Efficiency: Induction cooking is more energy-efficient than traditional gas or electric stoves because heat is generated directly in the cookware.
- Speed: Induction stoves can heat cookware very quickly, reducing cooking times.
- Safety: The cooking surface remains cool, reducing the risk of burns, and the stove automatically turns off when cookware is removed.
-
Disadvantages of Induction Cooking:
- Cookware Compatibility: Not all cookware is compatible with induction stoves, which may require users to invest in new pots and pans.
- Cost: Induction stoves are generally more expensive than traditional stoves, although the cost is offset by energy savings over time.
-
Applications Beyond Cooking:
- Induction heating is not limited to cooking; it is also used in industrial applications such as metal melting, forging, and heat treatment.
- The principles of electromagnetic induction and Joule heating are applied in various fields, including manufacturing and materials processing.
-
Physics Behind Induction Heating:
- The process involves two key physical phenomena: electromagnetic induction (generating eddy currents) and the Joule effect (converting electrical energy into heat).
- These principles are governed by Maxwell’s equations, which describe how electric and magnetic fields interact.
-
Future of Induction Heating:
- As technology advances, induction heating is becoming more accessible and affordable for home use.
- Innovations in induction cookware and stove design are likely to improve the user experience and expand the adoption of this efficient cooking method.
In summary, induction heating on a stove is a highly efficient and safe method of cooking that relies on electromagnetic induction to generate heat directly in ferromagnetic cookware. The process involves creating eddy currents within the cookware, which produce heat through resistive heating. This heat is then transferred to the food, making induction cooking fast, efficient, and safe. However, it requires compatible cookware and can be more expensive upfront compared to traditional cooking methods.
Summary Table:
Key Aspect | Details |
---|---|
Principle | Electromagnetic induction generates heat directly in ferromagnetic cookware. |
Heat Generation | Eddy currents in cookware produce heat through the Joule effect. |
Heat Transfer | Heat is transferred to food via conduction; cooktop remains cool. |
Cookware Requirements | Requires ferromagnetic materials like iron or steel. |
Advantages | Fast, energy-efficient, and safe cooking. |
Disadvantages | Requires compatible cookware; higher upfront cost. |
Applications | Used in cooking and industrial processes like metal melting. |
Ready to upgrade to an induction stove? Contact us today to learn more!