Metal laser sintering (MLS) is a sophisticated additive manufacturing process that uses a high-powered laser to fuse metal powder particles layer by layer to create a solid, three-dimensional object. This process is widely used in industries such as aerospace, automotive, and medical devices due to its ability to produce complex geometries with high precision and material efficiency. The process involves several key steps, including powder preparation, laser sintering, and post-processing, each of which plays a critical role in achieving the final product's desired properties.
Key Points Explained:
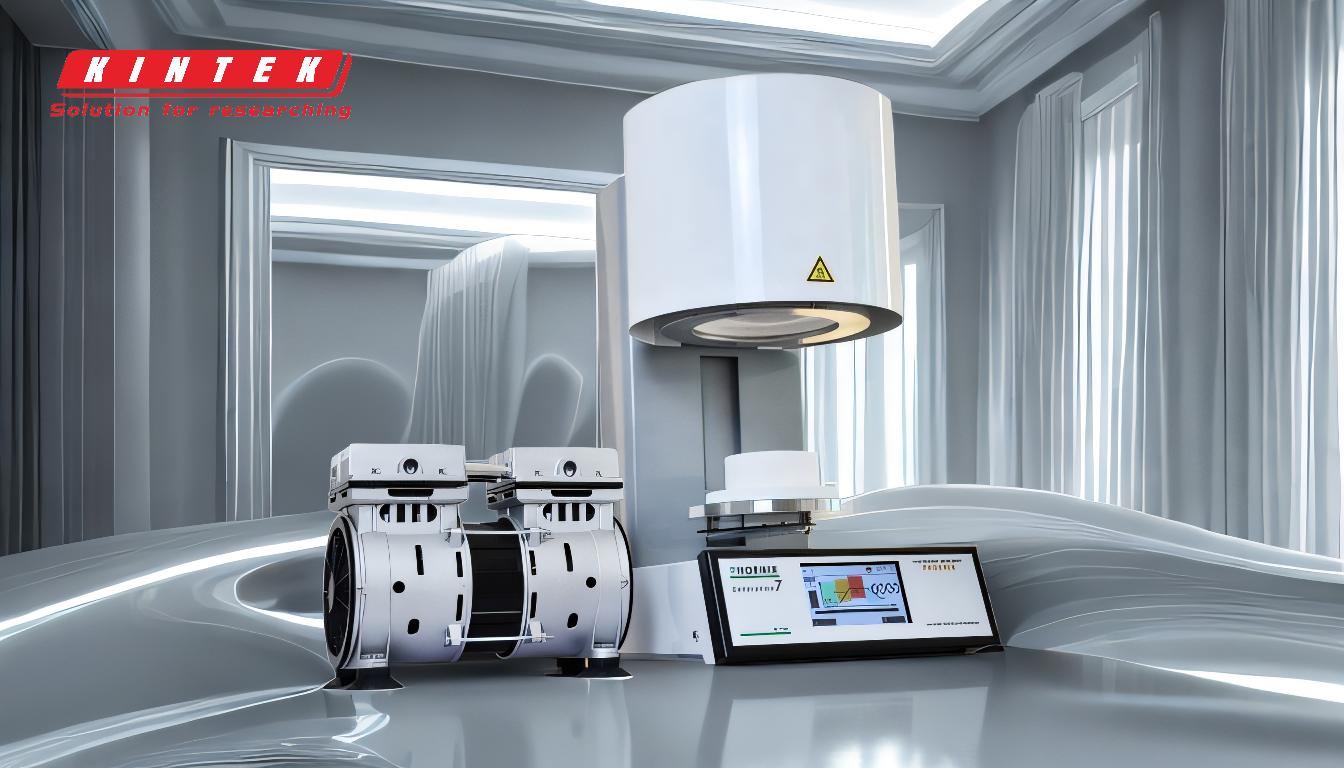
-
Powder Preparation:
- Material Selection: The process begins with the selection of appropriate metal powders. Common materials include titanium, aluminum, stainless steel, and nickel-based alloys. The choice of material depends on the desired properties of the final product, such as strength, durability, and thermal resistance.
- Powder Blending: The metal powders are often blended with alloying elements and additives to enhance specific properties. This blending ensures a homogeneous mixture that will result in a uniform final product.
-
Laser Sintering Process:
- Layer Deposition: A thin layer of the metal powder is spread evenly across the build platform. The thickness of this layer is typically in the range of 20-100 microns, depending on the desired resolution and the specific application.
- Laser Melting: A high-powered laser beam is directed onto the powder bed, selectively melting the powder particles according to the digital 3D model of the part. The laser's energy is precisely controlled to ensure that the metal particles fuse together without causing excessive thermal distortion.
- Layer Bonding: As each layer is sintered, it bonds with the previously sintered layers below it. This layer-by-layer approach allows for the creation of complex geometries and internal structures that would be difficult or impossible to achieve with traditional manufacturing methods.
-
Controlled Atmosphere:
- Inert Gas Environment: The sintering process typically takes place in a controlled atmosphere, often filled with inert gases like argon or nitrogen. This environment prevents oxidation and contamination of the metal, ensuring the integrity and quality of the final product.
- Temperature Control: The sintering furnace maintains a precise temperature, usually just below the melting point of the metal, to facilitate atomic diffusion and bonding between the particles without causing them to fully melt.
-
Post-Processing:
- Removal of Excess Powder: After the sintering process is complete, the excess powder that was not fused by the laser is removed. This powder can often be recycled and reused in subsequent builds.
- Heat Treatment: Depending on the material and the desired properties, the sintered part may undergo additional heat treatment processes such as annealing or stress relieving to enhance its mechanical properties.
- Surface Finishing: The final step often involves surface finishing processes such as machining, polishing, or coating to achieve the desired surface quality and dimensional accuracy.
-
Advantages and Applications:
- Complex Geometries: MLS allows for the creation of parts with complex internal structures and intricate details that are not feasible with traditional manufacturing methods.
- Material Efficiency: The process is highly material-efficient, as it only uses the amount of powder needed to build the part, minimizing waste.
- Customization and Prototyping: MLS is particularly valuable for rapid prototyping and custom manufacturing, enabling quick iteration and customization of designs.
- Industry Applications: The technology is widely used in industries that require high-performance components, such as aerospace for lightweight structures, automotive for custom parts, and medical devices for patient-specific implants.
In summary, metal laser sintering is a versatile and precise manufacturing process that leverages the power of lasers to fuse metal powders into complex, high-performance parts. The process involves careful preparation of materials, precise control of the sintering environment, and thorough post-processing to achieve the desired properties and finish. This technology continues to revolutionize manufacturing by enabling the production of parts that were previously impossible to create with traditional methods.
Summary Table:
Key Steps | Details |
---|---|
Powder Preparation | - Material selection (e.g., titanium, aluminum, stainless steel). |
- Powder blending for uniform properties. | |
Laser Sintering | - Layer deposition (20-100 microns). |
- Laser melting for precise fusion.
- Layer bonding for complex geometries. | | Controlled Atmosphere | - Inert gas environment (argon or nitrogen).
- Precise temperature control. | | Post-Processing | - Removal of excess powder.
- Heat treatment (annealing, stress relieving).
- Surface finishing (machining, polishing). | | Advantages | - Complex geometries.
- Material efficiency.
- Rapid prototyping and customization. | | Applications | - Aerospace, automotive, and medical devices. |
Ready to explore how metal laser sintering can transform your manufacturing process? Contact us today to learn more!