Microwave plasma generation involves using microwave energy to ionize gas molecules, creating a plasma state. This process typically occurs in a microwave cavity or waveguide where the gas is exposed to high-frequency electromagnetic waves. The microwaves provide enough energy to strip electrons from gas atoms, forming a plasma composed of free electrons, ions, and neutral particles. The efficiency of plasma generation depends on factors such as microwave frequency, power, gas pressure, and the type of gas used. This technology is widely used in applications like semiconductor manufacturing, surface treatment, and plasma chemistry due to its ability to produce stable and controllable plasma.
Key Points Explained:
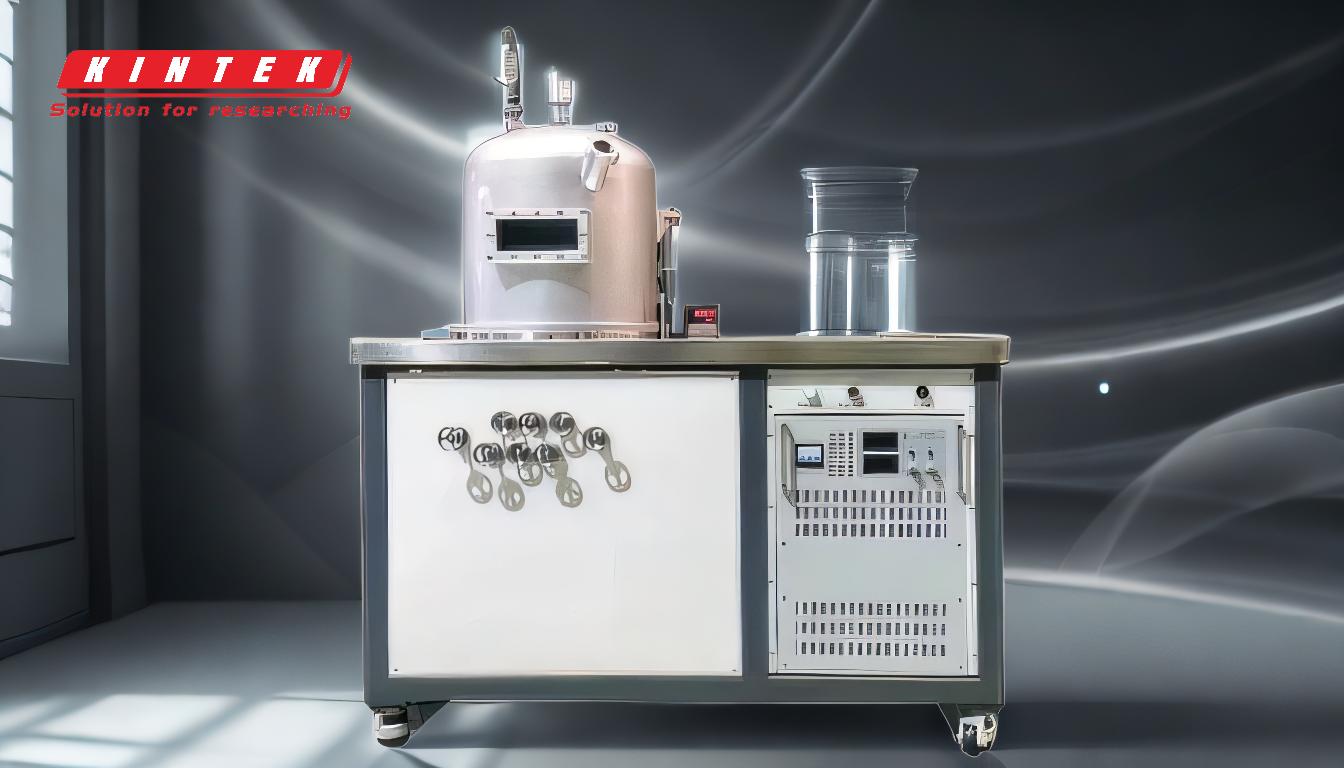
-
Microwave Energy and Plasma Formation:
- Microwaves are electromagnetic waves with frequencies typically ranging from 300 MHz to 300 GHz.
- When microwaves interact with a gas, they transfer energy to the gas molecules, causing them to vibrate and collide.
- If the energy transferred is sufficient, it can ionize the gas, stripping electrons from atoms and creating a plasma.
-
Microwave Cavity or Waveguide:
- A microwave cavity or waveguide is used to contain and direct the microwave energy.
- The cavity is designed to resonate at the microwave frequency, maximizing the energy transfer to the gas.
- The gas is introduced into the cavity, where it is exposed to the intense microwave field.
-
Ionization Process:
- The ionization process begins when the microwave energy exceeds the ionization energy of the gas molecules.
- Free electrons are accelerated by the microwave field, gaining enough energy to ionize other gas molecules through collisions.
- This chain reaction leads to the formation of a plasma, which is a mixture of free electrons, ions, and neutral particles.
-
Factors Affecting Plasma Generation:
- Microwave Frequency: Higher frequencies can provide more energy per photon, which can enhance ionization.
- Microwave Power: Higher power levels increase the energy available for ionization, leading to more intense plasma.
- Gas Pressure: Optimal pressure is necessary for efficient energy transfer; too low or too high pressure can hinder plasma formation.
- Type of Gas: Different gases have different ionization energies, affecting the ease of plasma generation.
-
Applications of Microwave Plasma:
- Semiconductor Manufacturing: Used for etching and deposition processes.
- Surface Treatment: Enhances surface properties like adhesion and wettability.
- Plasma Chemistry: Facilitates chemical reactions that are difficult to achieve with conventional methods.
-
Advantages of Microwave Plasma:
- Stability: Microwave plasma is generally more stable than other types of plasma.
- Control: The process parameters can be precisely controlled, allowing for consistent results.
- Efficiency: High energy transfer efficiency makes it suitable for industrial applications.
By understanding these key points, one can appreciate the complexity and utility of microwave plasma generation in various high-tech applications.
Summary Table:
Key Aspect | Details |
---|---|
Microwave Energy | Frequencies range from 300 MHz to 300 GHz, transferring energy to gas molecules. |
Microwave Cavity/Waveguide | Contains and directs microwave energy, resonating at specific frequencies. |
Ionization Process | Microwaves strip electrons from gas atoms, creating free electrons and ions. |
Key Factors | Frequency, power, gas pressure, and gas type influence plasma generation. |
Applications | Semiconductor manufacturing, surface treatment, and plasma chemistry. |
Advantages | High stability, precise control, and energy efficiency. |
Discover how microwave plasma generation can transform your processes—contact our experts today!