Pressure plays a critical role in deposition processes, particularly in plasma-based techniques like PECVD and sputter deposition. It directly influences the deposition rate, film quality, and microstructure by controlling gas density, mean free path, and ion energy distribution. Higher pressure increases reaction gas concentration and deposition rates but can reduce step coverage and introduce defects due to decreased mean free paths and enhanced plasma polymerization. Conversely, low pressure may lead to lower film density and defects like needle formations. Optimal pressure selection is essential to balance deposition efficiency and film quality, ensuring high-density, defect-free films with desired microstructural properties.
Key Points Explained:
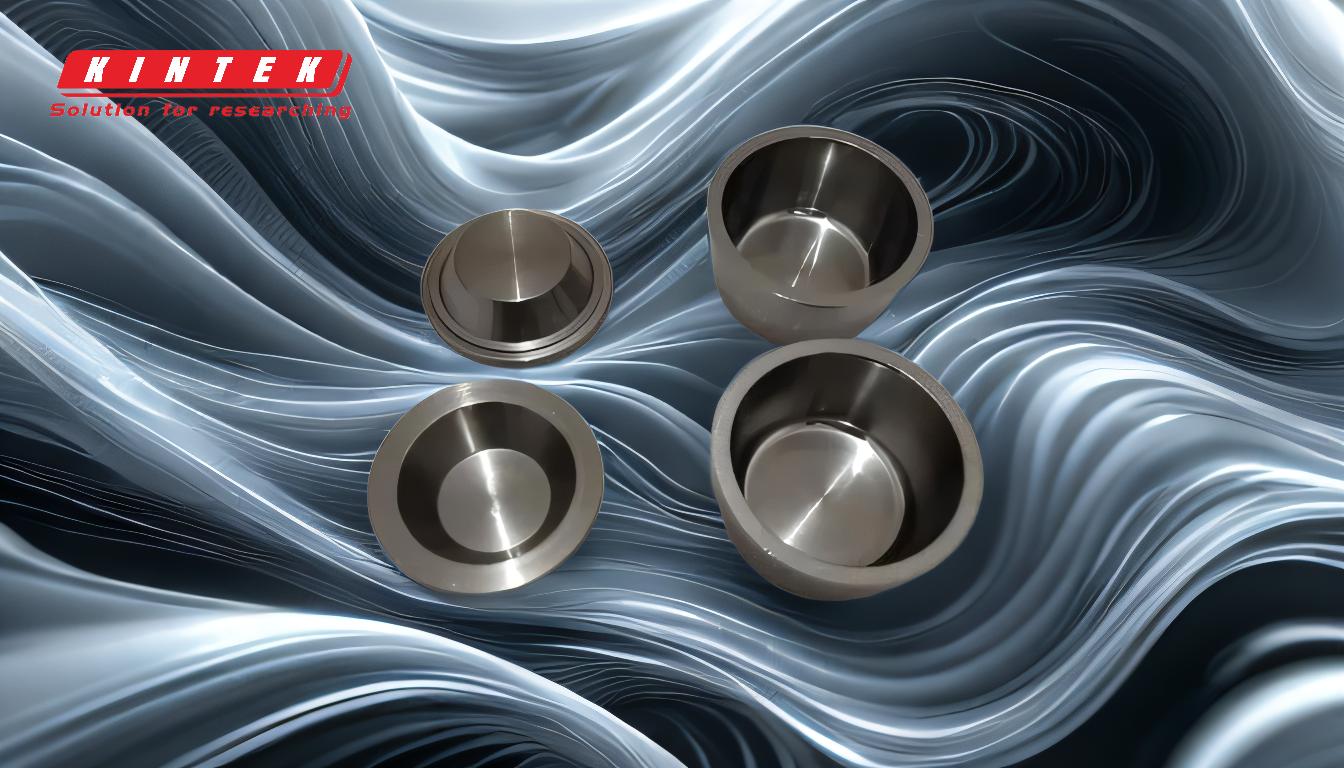
-
Effect of Pressure on Deposition Rate:
- Higher Pressure: Increases the concentration of reaction gases in the plasma, leading to a higher deposition rate. This is because more reactive species are available to participate in the deposition process.
- Lower Pressure: Reduces the availability of reaction gases, slowing down the deposition rate. This can also affect the deposition mechanism, leading to issues like reduced film density.
-
Impact on Mean Free Path:
- Higher Pressure: Decreases the mean free path of particles, which is the average distance a particle travels before colliding with another. A shorter mean free path can hinder the ability of the deposited film to cover steps or complex geometries evenly.
- Lower Pressure: Increases the mean free path, allowing particles to travel further before collisions. This can improve step coverage but may also reduce film density if the pressure is too low.
-
Film Quality and Defects:
- Higher Pressure: Can enhance plasma polymerization, leading to irregular growth networks and increased defects. This is due to the higher collision frequency and energy transfer between particles.
- Lower Pressure: May result in lower film density and the formation of needle-like defects. This occurs because the reduced pressure affects the deposition mechanism, leading to less dense and more porous films.
-
Microstructure and Ion Bombardment:
- Higher Pressure: Increases the kinetic energy of ions arriving at the substrate, which can alter the orientation of the microstructure. This can lead to increased ion bombardment, affecting the mobility rate of adsorbed atoms and potentially leading to a more disordered film structure.
- Lower Pressure: Reduces ion bombardment, which can result in a more ordered microstructure but may also reduce the overall film quality if the pressure is too low.
-
Optimal Pressure Selection:
- Balancing Act: Selecting the appropriate pressure is crucial for maximizing ion concentration and ensuring high-quality film deposition. The optimal pressure depends on the specific deposition process and desired film properties.
- Process-Specific Considerations: For techniques like PECVD and sputter deposition, pressure must be carefully controlled to achieve the desired balance between deposition rate, film quality, and microstructure.
-
Practical Implications for Equipment and Consumable Purchasers:
- System Design: Ensure that the deposition system can accurately control and maintain the desired pressure range. This may involve selecting systems with robust pressure control mechanisms.
- Material Selection: Choose consumables and materials that are compatible with the expected pressure ranges to avoid issues like contamination or premature wear.
- Process Optimization: Work closely with process engineers to optimize pressure settings for specific applications, ensuring that the deposition process meets the required film quality and performance criteria.
By understanding these key points, equipment and consumable purchasers can make informed decisions that enhance the efficiency and quality of deposition processes, ultimately leading to better-performing films and products.
Summary Table:
Aspect | Higher Pressure Effects | Lower Pressure Effects |
---|---|---|
Deposition Rate | Increases due to higher reaction gas concentration | Decreases due to reduced availability of reaction gases |
Mean Free Path | Decreases, reducing step coverage | Increases, improving step coverage but may reduce film density |
Film Quality & Defects | Enhances plasma polymerization, leading to irregular growth networks and defects | May result in lower film density and needle-like defects |
Microstructure | Increases ion bombardment, altering microstructure orientation | Reduces ion bombardment, potentially leading to a more ordered microstructure |
Optimal Pressure | Balancing pressure is crucial for high-quality film deposition and desired microstructure | Process-specific considerations are essential for achieving optimal results |
Need help optimizing your deposition process? Contact our experts today for tailored solutions!