Sintering is a critical process in materials science, where powdered materials are heated to a temperature below their melting point to form a solid mass. Pressure plays a significant role in enhancing the sintering process by reducing porosity, decreasing sintering time, and improving the mechanical properties of the final product. By applying pressure, particles are rearranged more efficiently, leading to better densification and stronger bonds between particles. This is particularly useful for materials that are difficult to sinter under normal conditions. The interplay between pressure, temperature, and other factors like particle size and composition determines the overall effectiveness of the sintering process.
Key Points Explained:
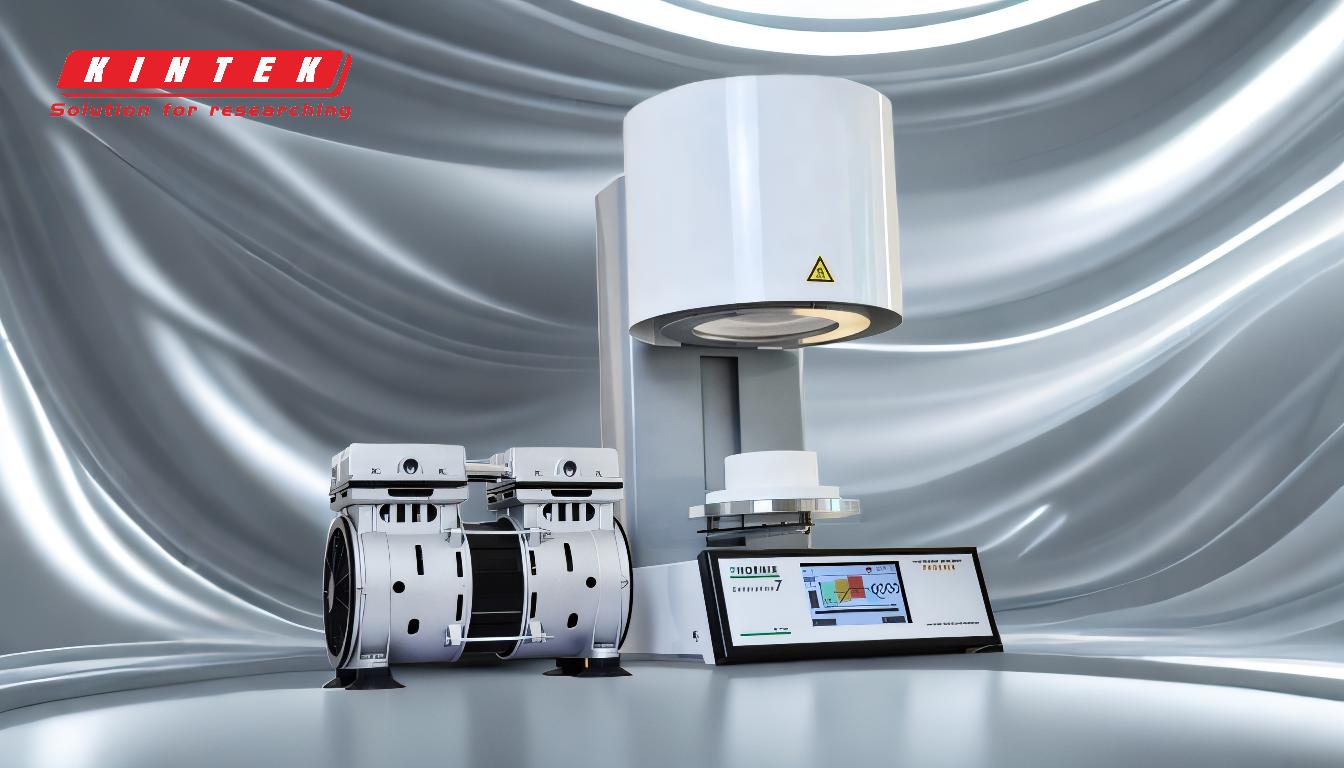
-
Role of Pressure in Sintering:
- Driving Force for Fusion: Pressure acts as an additional driving force during sintering, particularly in techniques like hot pressing. This is especially beneficial for materials that are challenging to sinter under standard conditions.
- Reduction in Porosity: Applying pressure helps to eliminate voids and pores within the material, leading to a denser and more compact final product.
- Decreased Sintering Time: Pressure accelerates the sintering process by enhancing particle rearrangement and bonding, reducing the overall time required to achieve the desired material properties.
-
Interaction Between Pressure and Temperature:
- Enhanced Densification: Higher temperatures combined with applied pressure can significantly increase the compaction of the material. This is because pressure aids in the rearrangement of particles, while temperature facilitates the diffusion processes necessary for sintering.
- Control of Liquid Phase: In some sintering processes, a liquid phase may form. Pressure helps in controlling the amount and distribution of this liquid phase, which is crucial for achieving the desired material properties.
-
Impact on Mechanical Properties:
- Improved Tensile Strength: The application of pressure during sintering can lead to a more homogeneous microstructure, which in turn enhances the tensile strength of the material.
- Increased Bending Fatigue Strength: Materials sintered under pressure exhibit better resistance to cyclic loading, making them suitable for applications requiring high durability.
- Higher Impact Energy: The densification achieved through pressure application results in materials with higher impact energy, making them more resistant to fracture.
-
Process Parameters and Their Optimization:
- Sintering Temperature: The temperature must be carefully controlled to ensure that the material does not melt but is sufficiently heated to allow particle bonding. Pressure can lower the required sintering temperature, making the process more energy-efficient.
- Heating Rate: A controlled heating rate is essential to avoid thermal stresses and ensure uniform densification. Pressure can help in maintaining a consistent heating rate by promoting even particle rearrangement.
- Particle Size and Composition: Smaller particles and homogeneous compositions sinter more effectively under pressure, as they have a higher surface area and fewer defects, leading to better densification.
-
Techniques Utilizing Pressure:
- Hot Pressing: This technique involves applying pressure and heat simultaneously, which is particularly effective for materials that are difficult to sinter. It results in high-density products with superior mechanical properties.
- Spark Plasma Sintering (SPS): SPS uses electrical currents and pressure to achieve rapid sintering. The combination of these factors allows for the production of materials with fine microstructures and enhanced properties.
-
Practical Considerations in Industrial Sintering:
- Air Volume and Vacuum Control: In industrial settings, controlling the air volume and vacuum levels is crucial for effective sintering. Pressure application can help in maintaining optimal conditions for sintering, especially in large-scale operations.
- Layer Thickness and Machine Speed: The thickness of the material layer and the speed of the sintering machine must be optimized to ensure that the material is sintered uniformly. Pressure aids in achieving consistent layer thickness and speed, leading to better-quality products.
In summary, pressure is a vital factor in the sintering process, influencing the densification, mechanical properties, and overall efficiency of the process. By understanding and optimizing the interplay between pressure, temperature, and other parameters, manufacturers can produce high-quality sintered materials tailored to specific applications.
Summary Table:
Aspect | Impact of Pressure |
---|---|
Porosity Reduction | Eliminates voids and pores, resulting in denser materials. |
Sintering Time | Accelerates particle rearrangement, reducing overall processing time. |
Mechanical Properties | Improves tensile strength, bending fatigue strength, and impact energy. |
Temperature Efficiency | Lowers required sintering temperature, saving energy. |
Techniques | Hot pressing and Spark Plasma Sintering (SPS) utilize pressure for superior results. |
Discover how pressure can optimize your sintering process—contact our experts today!