Physical Vapor Deposition (PVD) plating is a sophisticated process used to apply thin, durable coatings to various substrates. It involves transforming a solid material into a vapor state, which then condenses onto a target surface to form a thin film. This process is carried out under vacuum conditions to ensure purity and precision. PVD plating is widely used in industries such as electronics, automotive, and aerospace due to its ability to produce coatings with excellent adhesion, hardness, and corrosion resistance.
Key Points Explained:
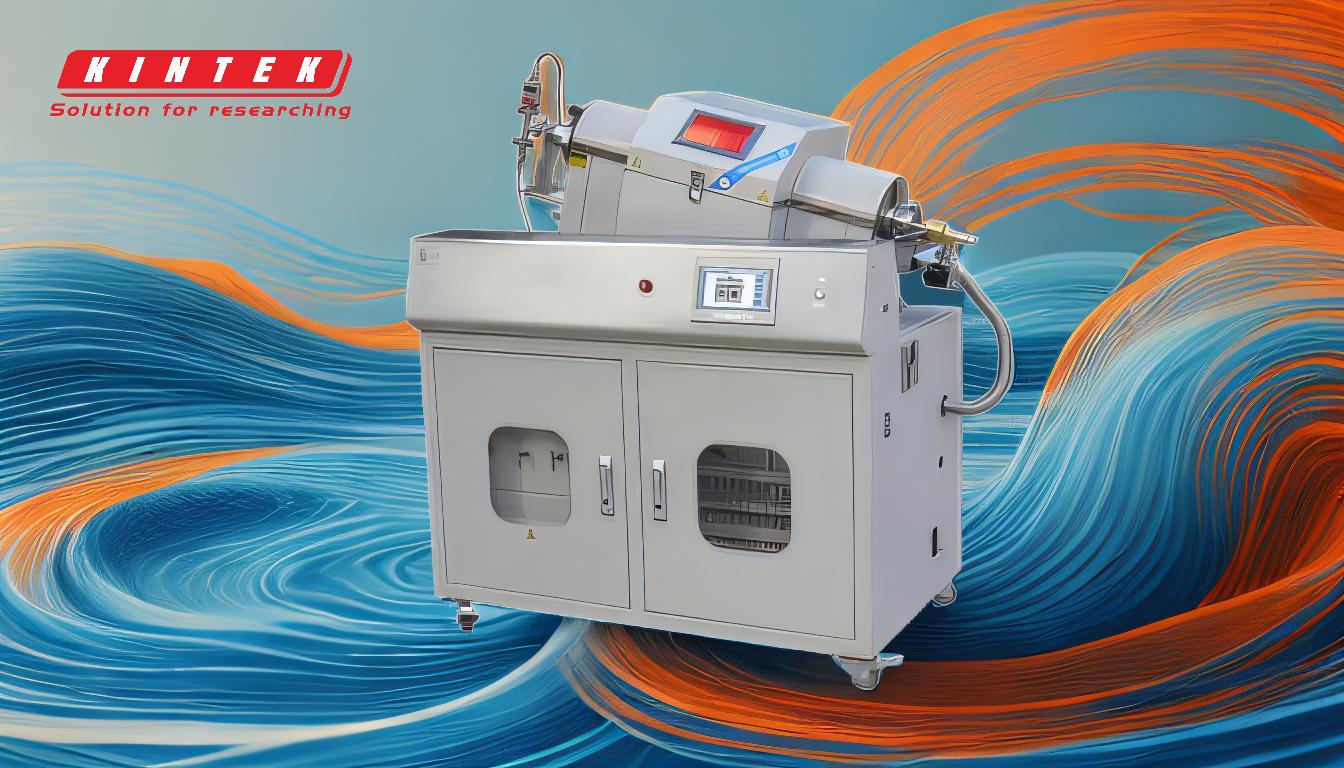
-
Vacuum Environment:
- PVD plating is performed in a vacuum to eliminate contaminants and ensure a clean deposition process. The vacuum environment prevents oxidation and other chemical reactions that could interfere with the coating's quality.
-
Material Vaporization:
- The solid material to be deposited is vaporized using high-energy sources such as high-power electricity, lasers, or plasma. This step is crucial as it converts the solid material into a gaseous state, allowing it to be transported to the substrate.
-
Introduction of Reactive Gas:
- A reactive gas, such as nitrogen or oxygen, is introduced into the vacuum chamber. This gas reacts with the vaporized material to form a compound. The choice of reactive gas depends on the desired properties of the final coating.
-
Deposition onto Substrate:
- The vaporized material, now in a reactive state, is directed towards the substrate. The atoms or molecules of the vaporized material adhere to the substrate surface, forming a thin, uniform coating. This step is critical for achieving the desired thickness and properties of the coating.
-
Formation of Thin Film:
- The deposited material forms a thin film on the substrate. This film can be a single layer or multiple layers, depending on the application requirements. The film's properties, such as hardness, adhesion, and corrosion resistance, are determined by the materials used and the deposition conditions.
-
High-Temperature Conditions:
- The entire process is typically carried out at high temperatures to ensure proper adhesion and uniformity of the coating. High temperatures also facilitate the reaction between the vaporized material and the reactive gas, leading to the formation of a stable compound.
-
Applications of PVD Plating:
- PVD plating is used in various industries for applications such as decorative coatings, wear-resistant coatings, and corrosion-resistant coatings. It is particularly valued for its ability to produce coatings with high hardness, excellent adhesion, and superior durability.
In summary, PVD plating is a complex but highly effective process for applying thin, durable coatings to various substrates. It involves vaporizing a solid material, reacting it with a gas, and depositing the resulting compound onto a substrate under vacuum and high-temperature conditions. This process is essential for producing high-quality coatings used in numerous industrial applications.
Summary Table:
Step | Description |
---|---|
Vacuum Environment | Eliminates contaminants and prevents oxidation for a clean deposition process. |
Material Vaporization | Solid material is vaporized using high-energy sources like electricity or lasers. |
Reactive Gas Introduction | A reactive gas (e.g., nitrogen) reacts with the vaporized material to form a compound. |
Deposition onto Substrate | Vaporized material adheres to the substrate, forming a thin, uniform coating. |
Thin Film Formation | Deposited material forms a thin film with desired properties like hardness. |
High-Temperature Conditions | Ensures proper adhesion and uniformity of the coating. |
Applications | Used in electronics, automotive, and aerospace for durable, high-quality coatings. |
Discover how PVD plating can enhance your products—contact our experts today!