Sintering temperature plays a critical role in determining the hardness of a material, as it directly influences the microstructure, density, and grain size of the sintered product. Optimal sintering temperatures, such as 1500℃ for zirconia, maximize material strength and hardness by achieving full densification and controlled grain growth. Deviations from this temperature, either too high or too low, can lead to defects like excessive grain growth or insufficient densification, which degrade hardness and other mechanical properties. Understanding the relationship between sintering temperature and hardness is essential for achieving desired material performance in ceramics and metals.
Key Points Explained:
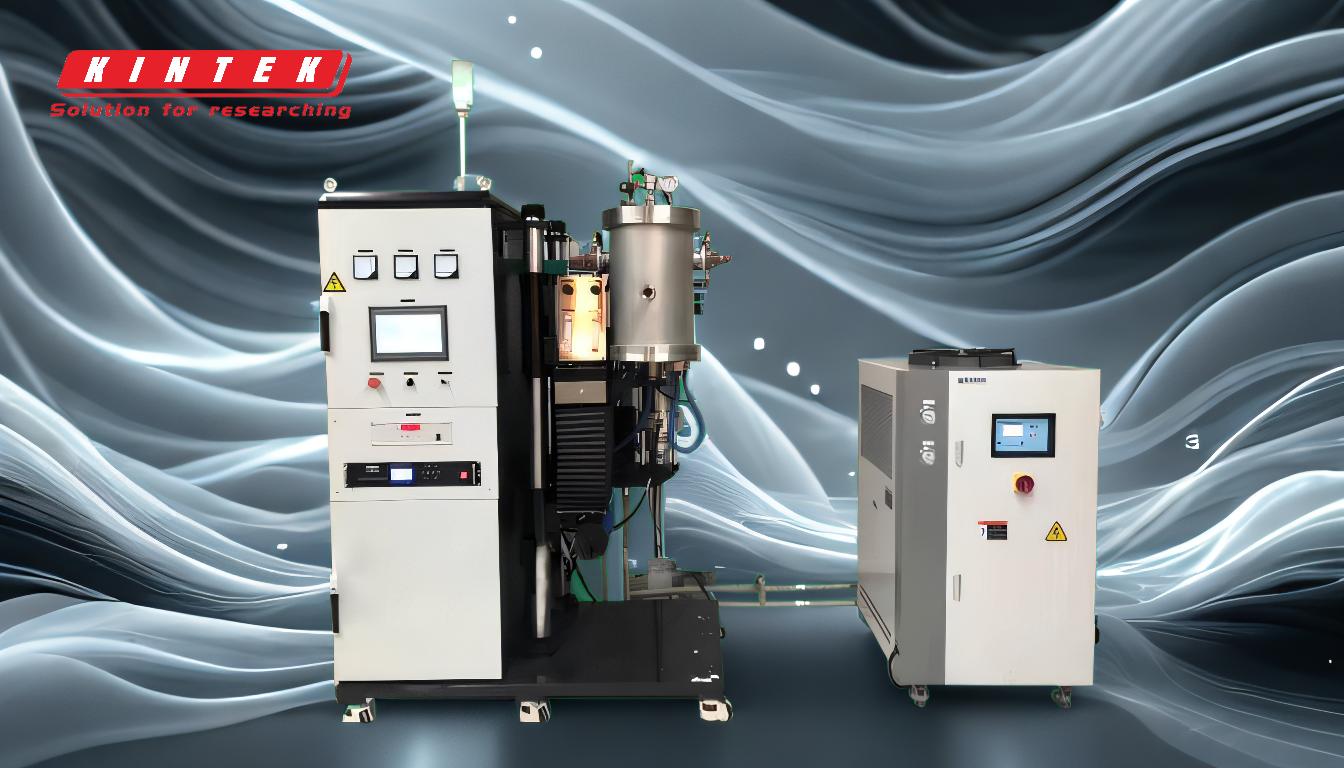
-
Sintering Temperature and Material Density:
- Sintering is a thermal process that bonds particles together, reducing porosity and increasing density.
- Higher sintering temperatures generally promote densification by enhancing particle diffusion and bonding.
- However, excessively high temperatures can lead to over-sintering, causing defects like exaggerated grain growth, which reduces hardness.
-
Optimal Sintering Temperature:
- For materials like zirconia, an optimal sintering temperature (e.g., 1500℃) maximizes strength and hardness.
- At this temperature, the material achieves full densification without significant grain growth, balancing density and microstructure.
- Deviations from this temperature, even by 150℃, can result in reduced hardness due to either incomplete densification or excessive grain growth.
-
Grain Growth and Hardness:
- Grain growth occurs when sintering temperatures are too high, leading to larger grains that weaken the material.
- Larger grains reduce hardness because they create fewer grain boundaries, which are critical for resisting deformation and crack propagation.
- Controlled sintering prevents excessive grain growth, maintaining a fine-grained microstructure that enhances hardness.
-
Porosity and Hardness:
- Low sintering temperatures or insufficient heating times can leave residual porosity in the material.
- Porosity acts as stress concentrators, reducing the material's ability to withstand external forces and lowering hardness.
- High sintering temperatures, when properly controlled, minimize porosity, leading to higher hardness.
-
Trade-offs in Sintering Parameters:
- Balancing sintering temperature and time is crucial to achieving optimal hardness.
- High temperatures and long sintering times can degrade properties if not carefully managed, while low temperatures may fail to achieve full densification.
- The goal is to find the right combination of temperature and time to maximize hardness without introducing defects.
-
Material-Specific Considerations:
- Different materials have unique optimal sintering temperatures. For example, zirconia performs best at around 1500℃, while other ceramics or metals may require different conditions.
- Understanding the specific sintering behavior of the material is essential for tailoring the process to achieve the desired hardness.
-
Practical Implications for Equipment and Consumable Purchasers:
- Purchasers should ensure that sintering equipment can precisely control temperature and time to achieve optimal results.
- Consumables, such as sintering furnaces, should be selected based on their ability to maintain consistent and accurate temperatures.
- Quality control measures, such as monitoring grain size and porosity, should be implemented to verify that the sintering process produces materials with the desired hardness.
By carefully controlling sintering temperature and understanding its effects on microstructure, density, and grain size, manufacturers can optimize the hardness of sintered materials, ensuring they meet performance requirements for various applications.
Summary Table:
Key Factor | Impact on Hardness |
---|---|
Optimal Sintering Temperature | Maximizes strength and hardness (e.g., 1500℃ for zirconia) by balancing density and grain size. |
High Temperature Risks | Excessive grain growth reduces hardness by weakening grain boundaries. |
Low Temperature Risks | Insufficient densification leaves porosity, lowering hardness. |
Grain Size | Fine-grained microstructures enhance hardness by resisting deformation and cracking. |
Porosity | Minimizing porosity through controlled sintering improves hardness. |
Material-Specific Needs | Different materials require unique sintering temperatures for optimal hardness. |
Want to achieve the perfect hardness for your materials? Contact our experts today for tailored sintering solutions!