Sintering temperature plays a critical role in determining the mechanical properties of materials, particularly ceramics and metals. Optimal sintering temperatures, such as 1500℃ for zirconia, maximize strength by promoting densification and minimizing porosity. Deviations from this temperature can lead to grain growth, reduced strength, and compromised mechanical integrity. The sintering process enhances properties like strength, hardness, and wear resistance by fostering particle bonding and densification. However, excessive temperatures can cause undesirable microstructural changes, such as increased grain size and porosity, which degrade performance. Understanding the relationship between sintering temperature and mechanical properties is essential for producing high-quality, durable components.
Key Points Explained:
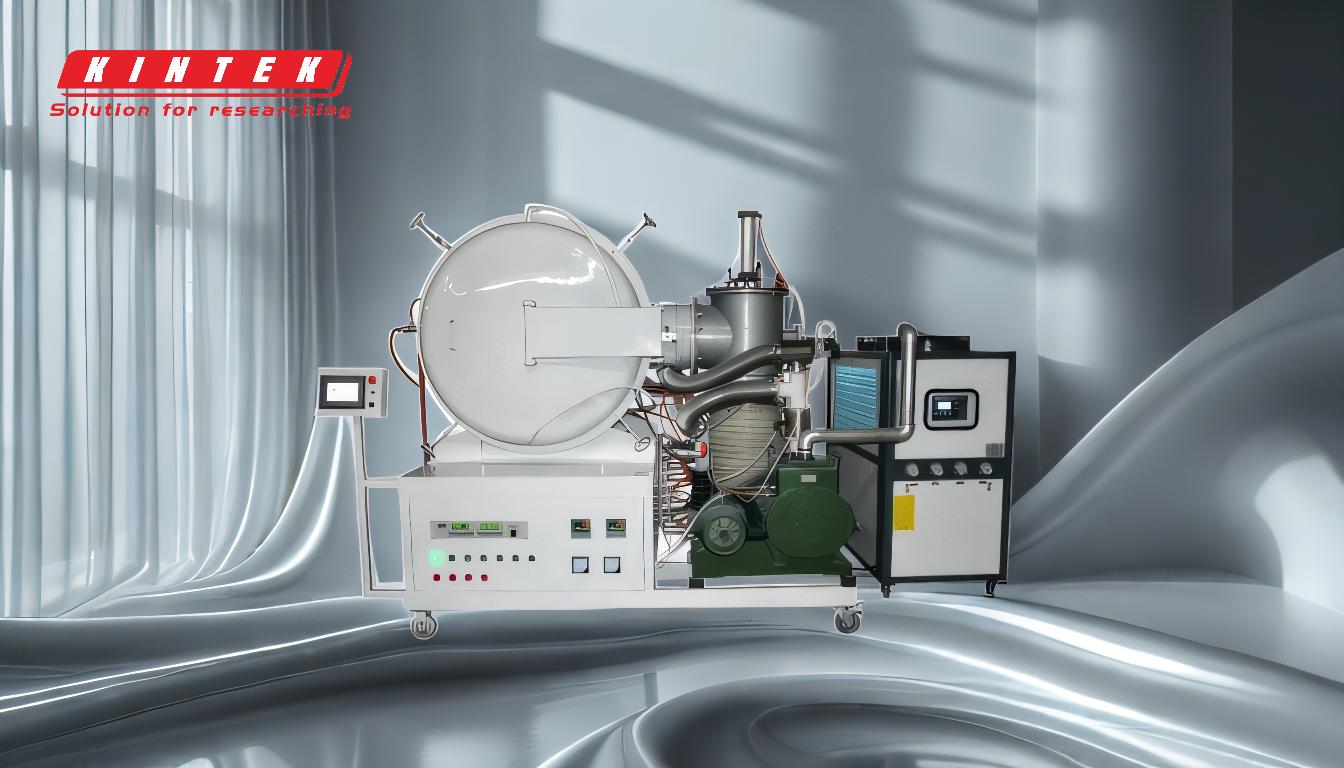
-
Optimal Sintering Temperature:
- For materials like zirconia, sintering at around 1500℃ maximizes strength by achieving full densification and minimizing porosity.
- Deviating from this temperature by as little as 150℃ can lead to significant reductions in strength due to grain growth and microstructural changes.
-
Impact of Temperature Deviations:
- Higher Temperatures: Excessive sintering temperatures can cause grain growth, leading to larger grains and increased porosity. This weakens the material by creating stress concentration points and reducing overall density.
- Lower Temperatures: Insufficient sintering temperatures may result in incomplete densification, leaving residual porosity and weak interparticle bonds, which compromise mechanical properties.
-
Microstructural Changes:
- Sintering temperature directly influences grain size, pore size, and grain boundary distribution. These microstructural features determine the material's strength, hardness, and durability.
- Controlled heating and diffusion mechanisms during sintering promote the formation of a dense and cohesive structure, enhancing mechanical integrity.
-
Mechanical Properties Enhanced by Sintering:
- Strength: Sintering bonds particles together, reducing porosity and increasing material strength.
- Hardness: Densification during sintering improves hardness by eliminating weak points in the microstructure.
- Wear Resistance: A dense, uniform structure resulting from proper sintering enhances wear resistance by reducing surface defects and improving cohesion.
-
Environmental and Manufacturing Benefits:
- Sintering is energy-efficient compared to melting, making it an environmentally friendly option.
- The process allows for precise control over material properties, ensuring consistent and high-quality products.
-
Practical Implications for Material Selection:
- Understanding the sintering temperature's impact on mechanical properties is crucial for selecting the right material and process parameters for specific applications.
- For example, in the case of zirconia, maintaining the sintering temperature within a narrow range is essential to achieve the desired strength and durability.
By carefully controlling sintering temperature, manufacturers can optimize the mechanical properties of materials, ensuring they meet the performance requirements for various industrial applications.
Summary Table:
Aspect | Impact of Sintering Temperature |
---|---|
Optimal Temperature | 1500℃ for zirconia maximizes strength by promoting densification and minimizing porosity. |
Higher Temperatures | Causes grain growth, increased porosity, and reduced strength. |
Lower Temperatures | Leads to incomplete densification, weak interparticle bonds, and compromised mechanical properties. |
Mechanical Properties | Enhances strength, hardness, and wear resistance through particle bonding and densification. |
Environmental Benefits | Energy-efficient process compared to melting, ensuring consistent and high-quality products. |
Optimize your material's mechanical properties with precise sintering—contact our experts today for tailored solutions!