Sintering temperature significantly impacts the porosity of sintered materials, particularly ceramics and metals. Higher sintering temperatures generally reduce porosity by enhancing particle diffusion mechanisms, such as boundary and lattice diffusion, which facilitate pore elimination. However, the relationship between temperature and porosity is influenced by factors such as the initial porosity of the green compact, sintering time, and material properties. While higher temperatures can lead to denser materials, excessively high temperatures or prolonged sintering times may cause defects or degrade material properties. Understanding this balance is crucial for achieving desired material characteristics like strength and durability.
Key Points Explained:
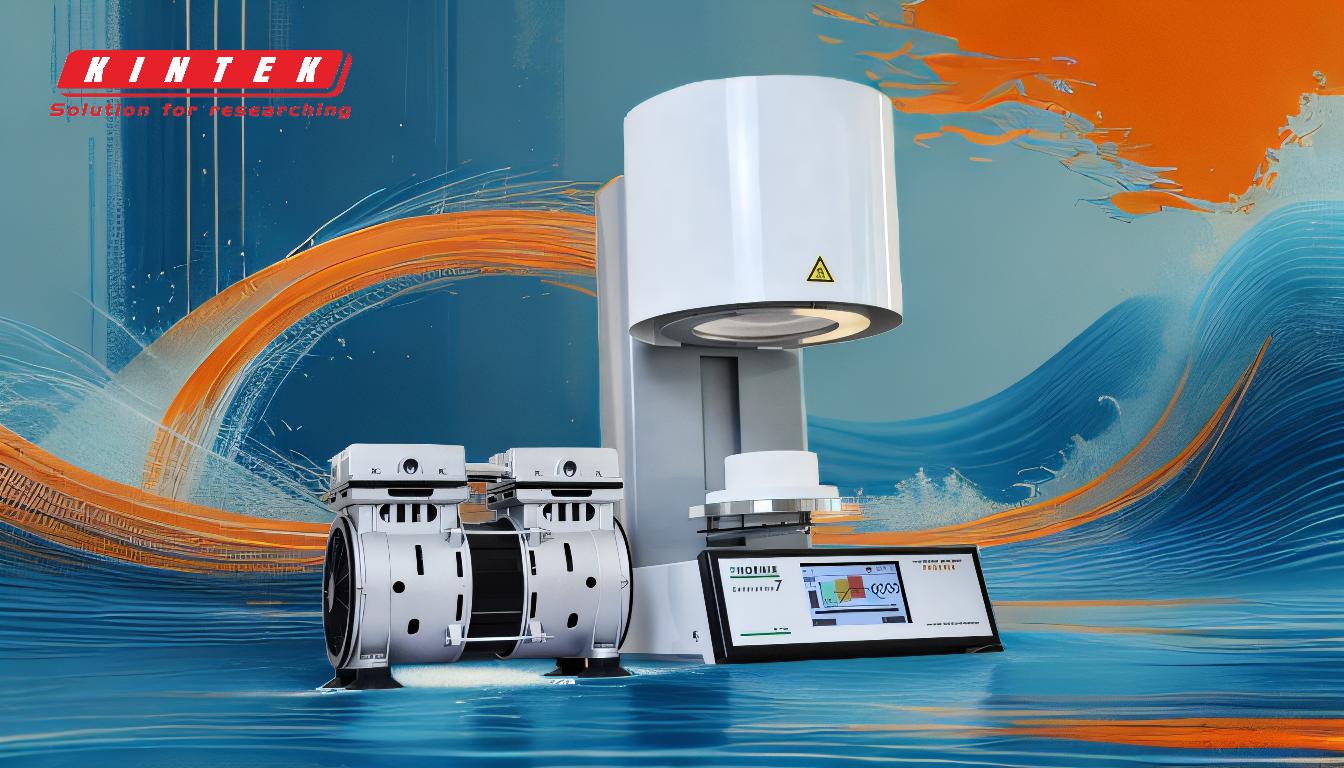
-
Mechanisms of Porosity Reduction During Sintering:
- Sintering reduces porosity through particle diffusion mechanisms, including boundary diffusion and lattice diffusion.
- At higher temperatures, these diffusion processes are accelerated, leading to faster pore elimination.
- In samples with uniform pore sizes and higher initial porosity, boundary diffusion distances are shorter, making pore elimination more efficient.
-
Role of Sintering Temperature:
- Higher sintering temperatures enhance particle mobility, promoting densification and reducing porosity.
- Pure oxide ceramics, which require solid-state diffusion, often need higher temperatures and longer sintering times to achieve low porosity.
- However, excessively high temperatures can lead to grain growth or defects, which may compromise material properties.
-
Influence of Initial Porosity:
- The initial porosity of the green compact plays a critical role in determining the final porosity after sintering.
- Materials with higher initial porosity tend to achieve greater densification during sintering, as there is more room for pore elimination.
-
Impact of Sintering Time:
- Longer sintering times allow more time for diffusion processes to occur, further reducing porosity.
- However, prolonged sintering at high temperatures can lead to over-sintering, causing grain growth or other defects.
-
Trade-offs in Sintering Parameters:
- Balancing sintering temperature and time is essential to achieve optimal material properties.
- Low sintering temperatures or insufficient heating times may result in incomplete densification and degraded properties.
- High sintering temperatures and long heating times can reduce porosity but may also introduce defects or weaken the material.
-
Practical Considerations for Material Selection:
- For materials like pure oxide ceramics, higher sintering temperatures and longer times are often necessary due to their reliance on solid-state diffusion.
- Applying external pressure during sintering (e.g., in hot pressing) can reduce sintering time and porosity, making it a useful technique for achieving dense materials efficiently.
By carefully controlling sintering temperature and time, manufacturers can tailor the porosity and density of sintered materials to meet specific performance requirements, ensuring optimal strength, durability, and other desired properties.
Summary Table:
Factor | Impact on Porosity |
---|---|
Sintering Temperature | Higher temperatures reduce porosity by enhancing particle diffusion mechanisms. |
Initial Porosity | Higher initial porosity allows greater densification during sintering. |
Sintering Time | Longer times reduce porosity but may cause defects if excessive. |
Material Properties | Pure oxide ceramics require higher temperatures and longer times for low porosity. |
External Pressure | Hot pressing reduces sintering time and porosity, enhancing efficiency. |
Need help optimizing sintering parameters for your materials? Contact our experts today!