Sputtering is a plasma-based deposition process where energetic ions are accelerated towards a target, causing atoms to be ejected from the surface and deposited onto a substrate. Plasma formation in sputtering involves the creation of a confined magnetic field that traps electrons, increasing ionization of sputtering gases. The plasma glow observed during the process results from the recombination of positively charged ions with free electrons, releasing energy as light. Key factors influencing plasma formation include magnetic field configuration, ion energy, and collision dynamics within the target material. Understanding these mechanisms is crucial for optimizing sputtering processes in thin-film deposition.
Key Points Explained:
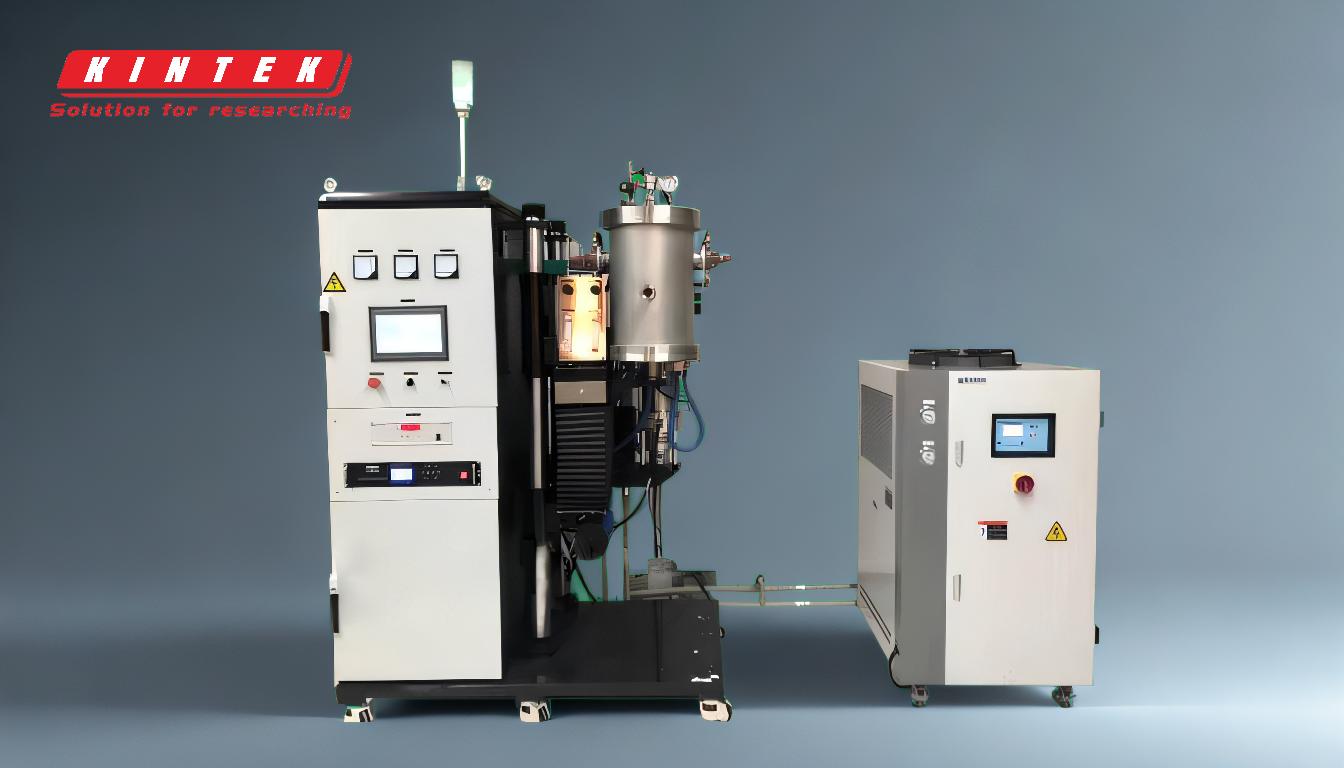
-
Plasma Confinement and Magnetic Fields:
- Plasma confinement is achieved using a permanent magnet structure mounted behind the target surface. This creates a closed-loop annular magnetic field that traps electrons, reshaping their trajectories into circular paths. This confinement increases the probability of ionization of sputtering gases, enhancing plasma density and stability.
-
Ion Bombardment and Sputtering Mechanism:
- Energetic ions are accelerated towards the target surface, initiating a linear collision cascade within the target material. When the energy of recoiling atoms exceeds the surface binding energy of the target, atoms are ejected (sputtered) from the surface. These ejected atoms travel toward the substrate, forming a thin film.
-
Plasma Glow and Recombination:
- The visible plasma glow in sputtering is produced when free electrons recombine with positively charged ions, transitioning to a lower energy state. The excess energy is released as light, creating the characteristic glow observed during the process.
-
Operating Parameters and Plasma Properties:
- Key parameters influencing plasma formation and sputtering efficiency include:
- Particle densities (ion and electron concentrations).
- Discharge current composition.
- Electron and ion energy distributions.
- Deposition rate and ionized flux fraction.
- These parameters are critical for controlling the quality and properties of the deposited film.
- Key parameters influencing plasma formation and sputtering efficiency include:
-
Discharge Maintenance Processes:
- The plasma is sustained through processes such as:
- Electron heating: Energy transfer to electrons to maintain ionization.
- Secondary electron creation: Electrons emitted from the target surface due to ion bombardment.
- Ohmic heating: Resistance heating within the plasma.
- Sputter processes: Continuous ejection of target material to sustain the deposition process.
- The plasma is sustained through processes such as:
-
Role of Thin Targets in Sputtering:
- If the target material is thin, collision cascades can reach the backside of the target. Atoms ejected from the backside escape the surface binding energy "in transmission," contributing to the sputtering process. This phenomenon is particularly relevant in applications requiring precise control over film thickness and composition.
By understanding these key points, equipment and consumable purchasers can better evaluate the requirements for sputtering systems, ensuring optimal performance and film quality in their applications.
Summary Table:
Key Aspect | Description |
---|---|
Plasma Confinement | Magnetic fields trap electrons, enhancing ionization and plasma stability. |
Ion Bombardment | Energetic ions eject target atoms, forming a thin film on the substrate. |
Plasma Glow | Recombination of ions and electrons releases energy as visible light. |
Operating Parameters | Particle densities, discharge current, and energy distributions control quality. |
Discharge Maintenance | Electron heating, secondary electron creation, and sputter processes sustain plasma. |
Thin Targets Role | Thin targets enable precise control over film thickness and composition. |
Ready to optimize your sputtering process? Contact our experts today for tailored solutions!