Temperature is a critical factor in the sintering process, as it directly influences the diffusion mechanisms that drive particle bonding, grain growth, and densification. Sintering involves heating compacted powder particles to temperatures below their melting point, allowing atoms to diffuse across boundaries and fuse particles together. The precise control of temperature, often achieved through advanced methods like AI-based controllers or PID modes in sintering furnaces, ensures efficient and consistent results. High temperatures enhance diffusion rates, but exceeding the material's melting point can lead to undesirable liquefaction. Understanding the relationship between temperature and sintering is essential for optimizing material properties and achieving desired outcomes.
Key Points Explained:
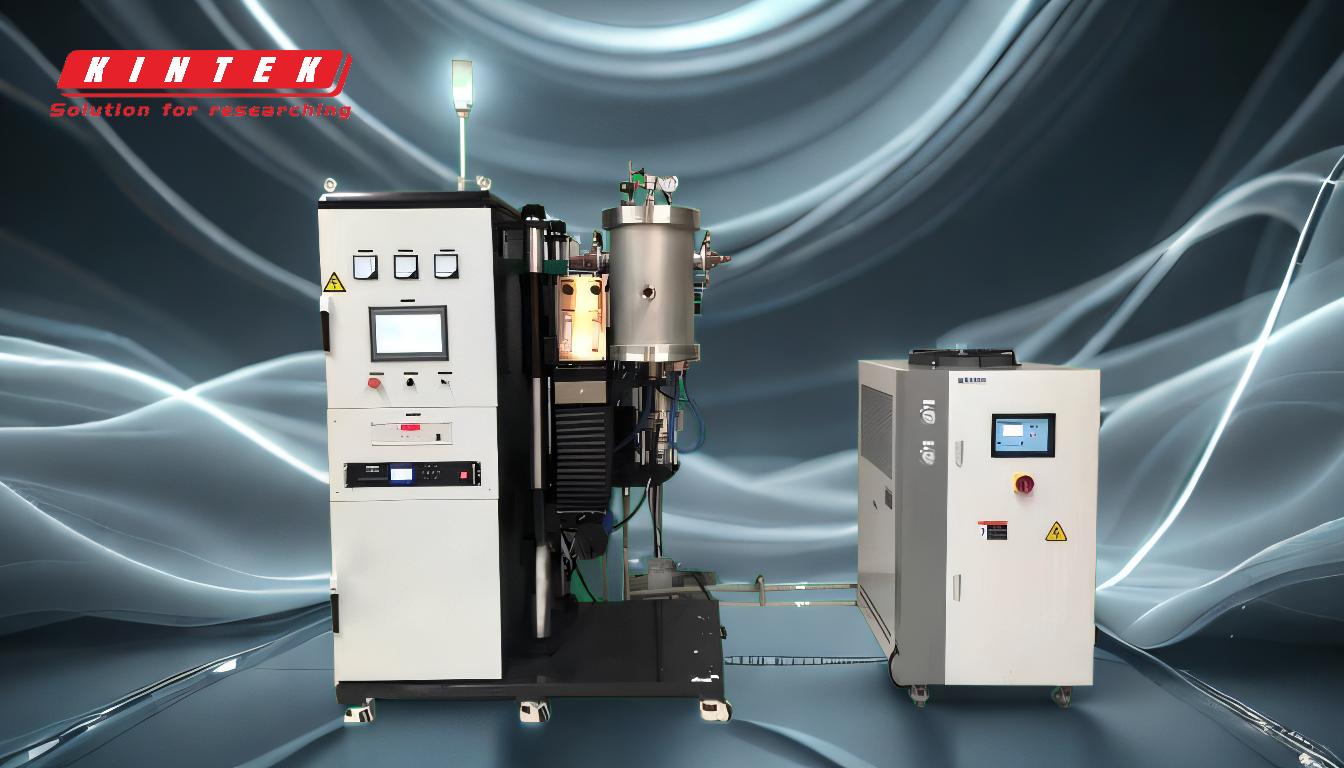
-
Role of Temperature in Sintering:
- Temperature is the primary driver of atomic diffusion during sintering. It must be high enough to enable grain boundary diffusion and bulk diffusion, which are essential for particle bonding and densification.
- However, the temperature must remain below the material's melting point to prevent liquefaction, which would compromise the structural integrity of the sintered product.
-
Temperature's Impact on Diffusion Mechanisms:
- Grain Boundary Diffusion: At lower temperatures, diffusion primarily occurs along grain boundaries, leading to initial particle bonding.
- Bulk Diffusion: As temperature increases, bulk diffusion becomes more dominant, allowing atoms to move through the entire particle structure, promoting densification and grain growth.
- The rate of diffusion increases exponentially with temperature, making precise control critical for achieving uniform material properties.
-
High-Temperature Effects:
- High temperatures in a sintering furnace accelerate the diffusion process, enabling faster bonding and densification.
- Temperatures can reach several thousand degrees Celsius, depending on the material and desired outcome. For example, ceramics and metals often require different temperature ranges to achieve optimal sintering.
-
Temperature Control Methods:
- AI-Based Controllers: Modern sintering furnaces use AI-based systems to maintain precise temperature control across all zones, ensuring uniformity and efficiency. This technology also contributes to energy savings.
- PID Mode: In vacuum sintering furnaces, PID (Proportional-Integral-Derivative) controllers automate the heating and cooling processes. Once the program is set, the furnace operates without manual intervention, ensuring consistent results.
-
Material-Specific Considerations:
- Different materials have unique sintering temperature ranges. For instance, ceramics typically require higher temperatures than metals due to their higher melting points.
- The particle size, composition, and distribution of the powder also influence the optimal sintering temperature. Smaller particles, for example, sinter at lower temperatures due to their higher surface energy.
-
Sintering Environment:
- The sintering environment, such as vacuum or controlled atmosphere, can affect temperature requirements. Vacuum sintering, for example, often requires precise temperature control to prevent oxidation or contamination.
- The environment also influences the cooling rate, which can impact the final microstructure and mechanical properties of the sintered material.
-
Practical Implications for Equipment Purchasers:
- When selecting a sintering furnace, consider the temperature range, control precision, and automation capabilities. AI-based controllers and PID systems are ideal for achieving consistent and efficient sintering.
- Evaluate the furnace's ability to handle the specific materials and temperature requirements of your application. For example, high-temperature furnaces are essential for sintering ceramics, while lower-temperature models may suffice for certain metals.
By understanding how temperature affects sintering and the technologies available for precise control, purchasers can make informed decisions when selecting equipment. This ensures optimal material properties, process efficiency, and cost-effectiveness in sintering applications.
Summary Table:
Aspect | Impact of Temperature |
---|---|
Role in Sintering | Drives atomic diffusion for particle bonding and densification. |
Diffusion Mechanisms | Grain boundary diffusion at lower temps; bulk diffusion dominates at higher temps. |
High-Temperature Effects | Accelerates diffusion but must stay below melting point to avoid liquefaction. |
Control Methods | AI-based controllers and PID modes ensure precise and consistent temperature regulation. |
Material-Specific Needs | Ceramics require higher temps; metals vary based on composition and particle size. |
Sintering Environment | Vacuum or controlled atmospheres influence temperature requirements and cooling rates. |
Ready to optimize your sintering process? Contact us today for expert advice on selecting the right sintering furnace!