The atmosphere in a sintering furnace significantly influences the sintering process by controlling surface reactions and material properties. It can either protect the material from unwanted chemical reactions or facilitate specific surface modifications, depending on the desired outcome. Factors such as oxidation prevention, impurity control, and material purity are heavily dependent on the type of atmosphere used. For instance, a vacuum environment prevents oxidation and contamination, while reactive gases can enable deoxidization or decarburization. Proper atmosphere control ensures the stability, quality, and performance of the final product, making it a critical consideration in sintering applications.
Key Points Explained:
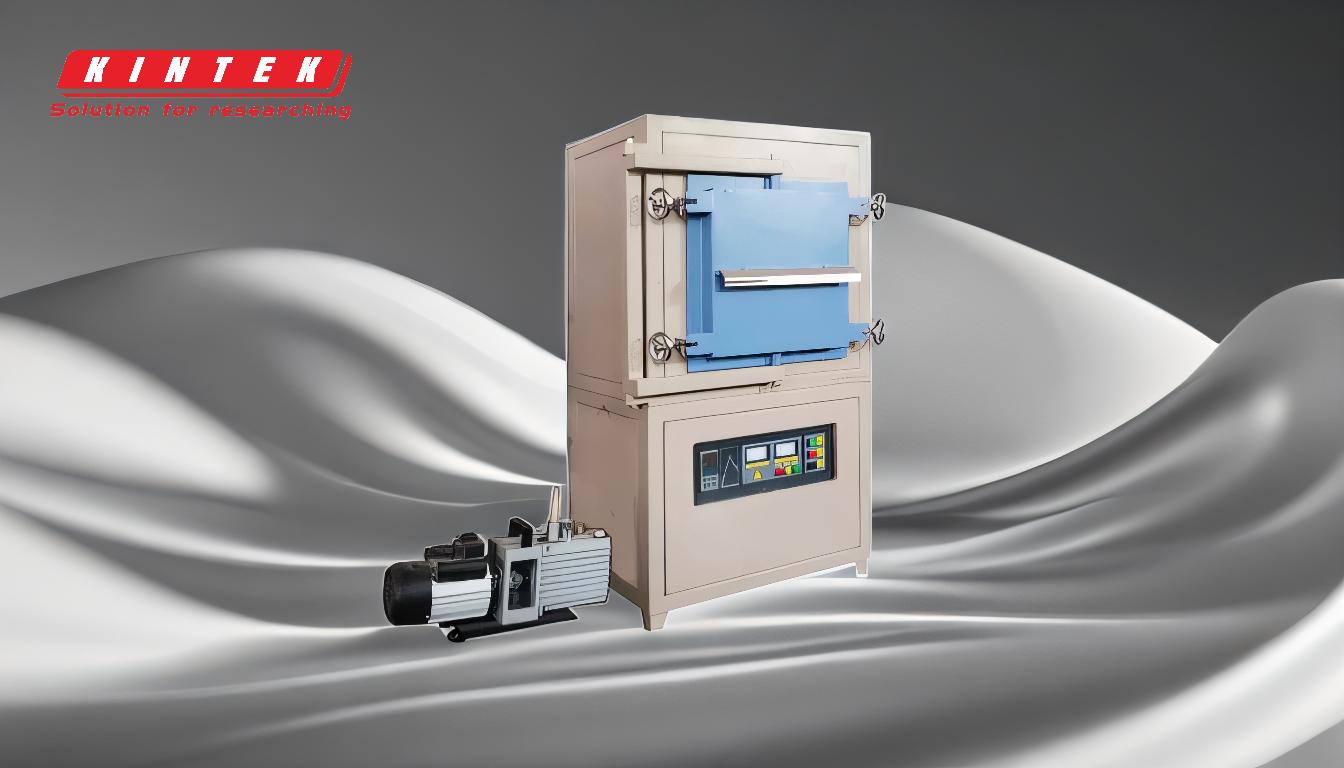
-
Role of Atmosphere in Sintering:
- The atmosphere in a sintering furnace plays a dual role: it can either protect the material from surface reactions (chemically inert) or enable specific surface changes (chemically reactive). This depends on the material and process requirements.
- For example, inert gases like argon or nitrogen are used to prevent oxidation, while reactive gases like hydrogen can facilitate deoxidization or decarburization.
-
Prevention of Oxidation and Contamination:
- A vacuum or inert atmosphere in a sintering furnace prevents oxidation reactions and impurity contamination. This is particularly important for materials that are sensitive to oxygen, such as metals and ceramics.
- By maintaining a controlled environment, the purity and performance of the material are significantly improved.
-
Material-Specific Atmosphere Requirements:
- Different materials require specific atmospheric conditions to achieve optimal sintering results. For instance:
- Metals like titanium or stainless steel often require inert or reducing atmospheres to prevent oxidation.
- Ceramics may need controlled oxygen levels to achieve the desired microstructure.
- Different materials require specific atmospheric conditions to achieve optimal sintering results. For instance:
-
Atmosphere Control in Dental Sintering:
- In dental sintering furnaces, atmosphere control is crucial for ensuring the stability and quality of dental restorations. The right atmosphere prevents defects and ensures consistent material properties, which are critical for biocompatibility and durability.
-
Regulation of Sintering Vectors:
- The sintering atmosphere is regulated to control various sintering vectors, such as deoxidization and decarburization. This is achieved by using specific gases tailored to the requirements of each equipment zone.
- For example, hydrogen is often used for deoxidization, while carbon-containing gases can be used for carburization processes.
-
Impact on Final Product Quality:
- Proper atmosphere control directly impacts the quality of the final sintered product. It ensures uniform density, improved mechanical properties, and enhanced thermal resistance.
- Inconsistent or improper atmosphere control can lead to defects such as porosity, cracking, or reduced strength.
By understanding and optimizing the sintering atmosphere, manufacturers can achieve superior material properties and ensure the reliability of their products. This makes atmosphere control a critical factor in the design and operation of sintering furnaces.
Summary Table:
Aspect | Details |
---|---|
Role of Atmosphere | Protects materials or enables surface modifications (inert/reactive gases). |
Oxidation Prevention | Vacuum or inert gases prevent oxidation and contamination. |
Material-Specific Needs | Metals (inert/reducing), ceramics (controlled oxygen). |
Dental Sintering | Ensures biocompatibility, durability, and defect-free restorations. |
Sintering Vectors | Regulates deoxidization, decarburization with specific gases. |
Final Product Quality | Improves density, mechanical properties, and thermal resistance. |
Discover how proper atmosphere control can enhance your sintering process—contact our experts today!