Pressing machines are versatile tools used in various industries to shape, mold, or compress materials into desired forms. They operate by applying controlled force to a workpiece, often using hydraulic, mechanical, or pneumatic systems. The process involves placing the material between two dies or molds, which are then pressed together under high pressure to achieve the desired shape or density. The machine's operation can be adjusted for factors like pressure, speed, and temperature, depending on the material and application. Pressing machines are widely used in manufacturing, construction, and material processing industries.
Key Points Explained:
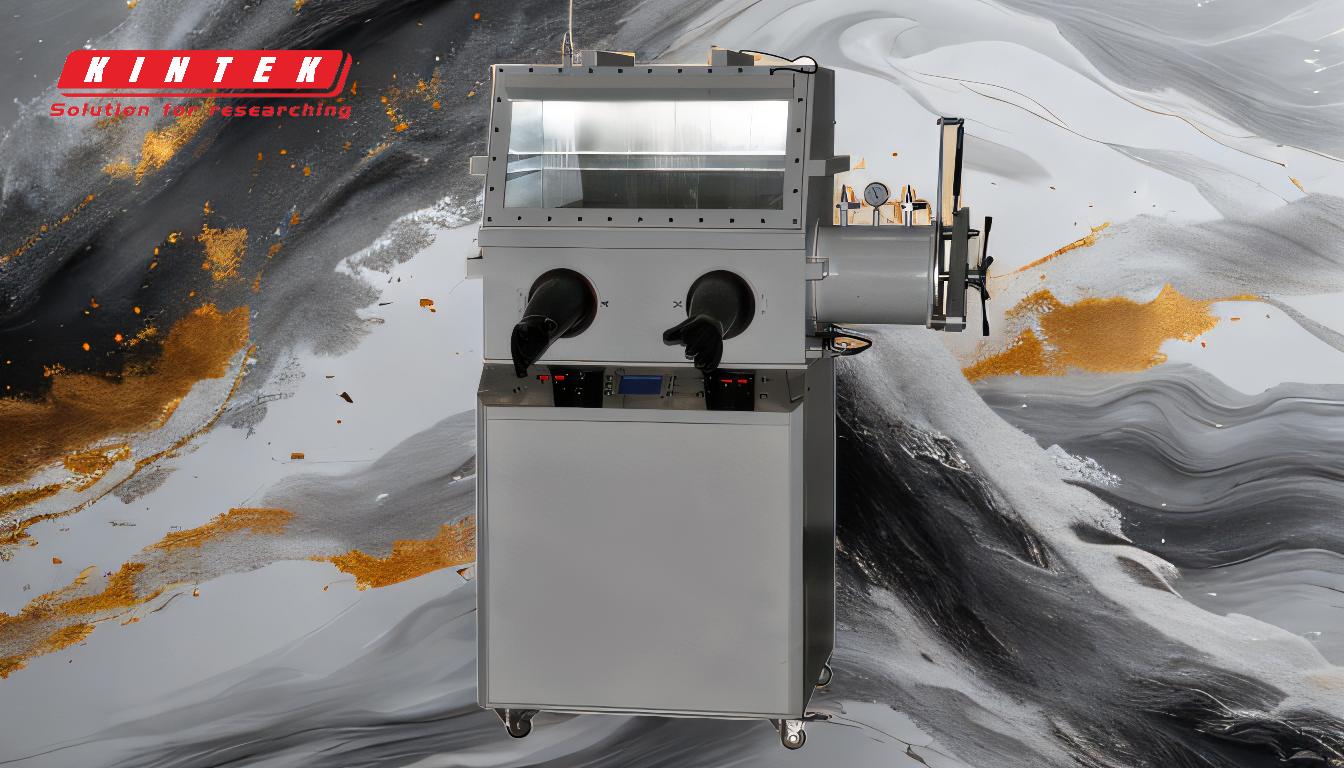
-
Types of Pressing Machines:
- Hydraulic Presses: These machines use hydraulic cylinders to generate force. They are ideal for applications requiring high pressure and precision, such as metal forming and plastic molding.
- Mechanical Presses: These rely on mechanical mechanisms, like flywheels and crankshafts, to apply force. They are commonly used in stamping and forging operations.
- Pneumatic Presses: These use compressed air to generate force, making them suitable for lighter applications like assembly and riveting.
-
Working Principle:
- The material to be processed is placed between two dies or molds.
- The machine applies force to compress or shape the material. The force can be adjusted based on the material's properties and the desired outcome.
- Hydraulic presses use fluid pressure to move a piston, while mechanical presses convert rotational motion into linear force. Pneumatic presses use air pressure to achieve the same.
-
Key Components:
- Frame: Provides structural support and stability.
- Ram or Platen: The moving part that applies force to the material.
- Dies or Molds: Custom-designed tools that shape the material.
- Control System: Regulates pressure, speed, and other parameters.
-
Applications:
- Manufacturing: Used in stamping, forging, and molding processes.
- Construction: Compacting materials like concrete or asphalt.
- Material Processing: Densifying powders or forming composite materials.
-
Advantages:
- High precision and repeatability.
- Ability to handle a wide range of materials and shapes.
- Adjustable parameters for customized results.
-
Considerations for Purchasers:
- Capacity: Ensure the machine can handle the required force and material size.
- Versatility: Look for machines that can accommodate multiple applications.
- Ease of Maintenance: Choose models with accessible components and reliable support.
By understanding these key points, purchasers can make informed decisions when selecting a pressing machine for their specific needs.
Summary Table:
Aspect | Details |
---|---|
Types | Hydraulic, Mechanical, Pneumatic |
Working Principle | Applies force via hydraulic fluid, mechanical mechanisms, or compressed air |
Key Components | Frame, Ram/Platen, Dies/Molds, Control System |
Applications | Manufacturing, Construction, Material Processing |
Advantages | High precision, versatility, adjustable parameters |
Considerations | Capacity, versatility, ease of maintenance |
Ready to find the perfect pressing machine for your needs? Contact us today for expert guidance!