Thermal evaporation is a fundamental physical vapor deposition (PVD) technique used to create thin films on substrates. It involves heating a target material in a vacuum chamber until it reaches its evaporation point, producing vapor that travels through the vacuum and condenses on a substrate, forming a thin film. This process is widely used in industries such as electronics, optics, and solar energy for depositing metals like silver and aluminum. The method relies on resistive heating elements, such as boats or coils, to generate the necessary thermal energy. Thermal evaporation is valued for its simplicity, cost-effectiveness, and ability to produce high-purity films.
Key Points Explained:
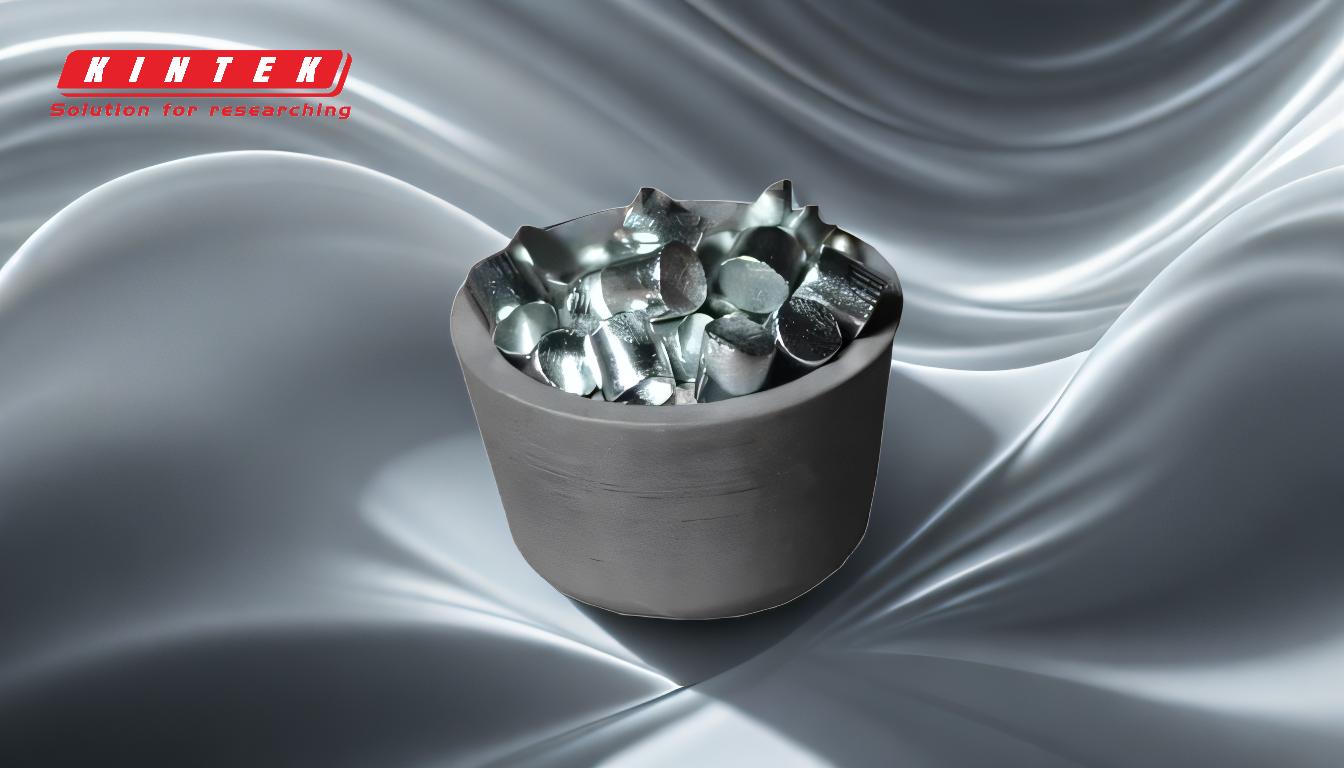
-
Basic Principle of Thermal Evaporation:
- Thermal evaporation operates on the principle of heating a target material until it vaporizes. The vaporized atoms or molecules then travel through a vacuum and deposit onto a substrate, forming a thin film.
- This process is driven by the generation of vapor pressure, which occurs when the material is heated to its evaporation temperature.
-
Components of the Thermal Evaporation System:
- Vacuum Chamber: The process occurs in a vacuum environment to minimize contamination and allow the vaporized material to travel unimpeded to the substrate.
- Evaporation Source: The target material is placed in an evaporation source, such as a boat, coil, or basket, made of materials like tungsten or molybdenum that can withstand high temperatures.
- Heating Element: A resistive heating element, such as a tungsten filament or boat, is used to heat the target material. Electric current passes through the element, generating heat through electrical resistance.
- Substrate: The surface onto which the thin film is deposited, typically positioned above the evaporation source.
-
Process Steps:
- Heating the Material: The target material is heated using a resistive heating element until it reaches its evaporation temperature. This causes the material to melt and then vaporize.
- Vaporization and Transport: The vaporized atoms or molecules travel through the vacuum chamber toward the substrate. The vacuum ensures minimal collisions with other particles, allowing for a direct and efficient deposition.
- Deposition and Film Formation: The vapor condenses on the substrate, forming a thin, uniform film. The thickness and properties of the film can be controlled by adjusting parameters such as heating temperature, evaporation rate, and substrate position.
-
Types of Thermal Evaporation:
- Resistive Evaporation: The most common method, where a resistive heating element (e.g., a boat or coil) is used to heat the target material.
- Electron Beam Evaporation: A more advanced technique where an electron beam is directed at the target material, providing localized heating and allowing for the evaporation of high-melting-point materials.
-
Applications of Thermal Evaporation:
- OLEDs and Thin Film Transistors: Used to deposit metals like aluminum and silver for electronic devices.
- Solar Cells: Applied in the production of thin-film solar cells to create conductive layers.
- Optical Coatings: Utilized for creating reflective and anti-reflective coatings on lenses and mirrors.
-
Advantages of Thermal Evaporation:
- Simplicity: The process is straightforward and easy to implement.
- Cost-Effectiveness: Requires relatively simple and inexpensive equipment compared to other PVD methods.
- High Purity: Produces films with high purity due to the vacuum environment and minimal contamination.
- Versatility: Can be used with a wide range of materials, including metals, alloys, and some compounds.
-
Limitations of Thermal Evaporation:
- Material Limitations: Not suitable for materials with extremely high melting points or those that decompose before evaporating.
- Uniformity Challenges: Achieving uniform film thickness can be difficult, especially for large or complex substrates.
- Limited Adhesion: The adhesion of the deposited film to the substrate may be weaker compared to other deposition methods.
-
Key Parameters to Control:
- Vacuum Pressure: Maintaining a high vacuum is critical to ensure efficient transport of vaporized material and minimize contamination.
- Heating Rate: Controlling the rate of heating helps achieve consistent evaporation and film quality.
- Substrate Temperature: The temperature of the substrate can influence the film's microstructure and adhesion properties.
By understanding these key points, equipment and consumable purchasers can make informed decisions about the suitability of thermal evaporation for their specific applications, as well as the necessary equipment and materials required for the process.
Summary Table:
Aspect | Details |
---|---|
Basic Principle | Heating a target material until it vaporizes and deposits onto a substrate. |
Key Components | Vacuum chamber, evaporation source, heating element, substrate. |
Process Steps | Heating, vaporization, transport, deposition. |
Types | Resistive evaporation, electron beam evaporation. |
Applications | OLEDs, solar cells, optical coatings. |
Advantages | Simplicity, cost-effectiveness, high purity, versatility. |
Limitations | Material limitations, uniformity challenges, limited adhesion. |
Key Parameters | Vacuum pressure, heating rate, substrate temperature. |
Discover how thermal evaporation can enhance your thin film processes—contact our experts today!