Induction heating is a highly efficient method of heating conductive materials, offering advantages such as rapid heating, precise temperature control, and reduced energy loss compared to traditional heating methods. Its efficiency is influenced by factors like material properties, system design, and operating conditions. Induction heating systems are more efficient than open-hearth furnaces, with advancements in semiconductor technology and coil design further improving their performance. The method generates heat directly within the material, minimizing heat loss and enabling targeted heating at specific depths. Overall, induction heating is a cost-effective and energy-efficient solution for various industrial applications.
Key Points Explained:
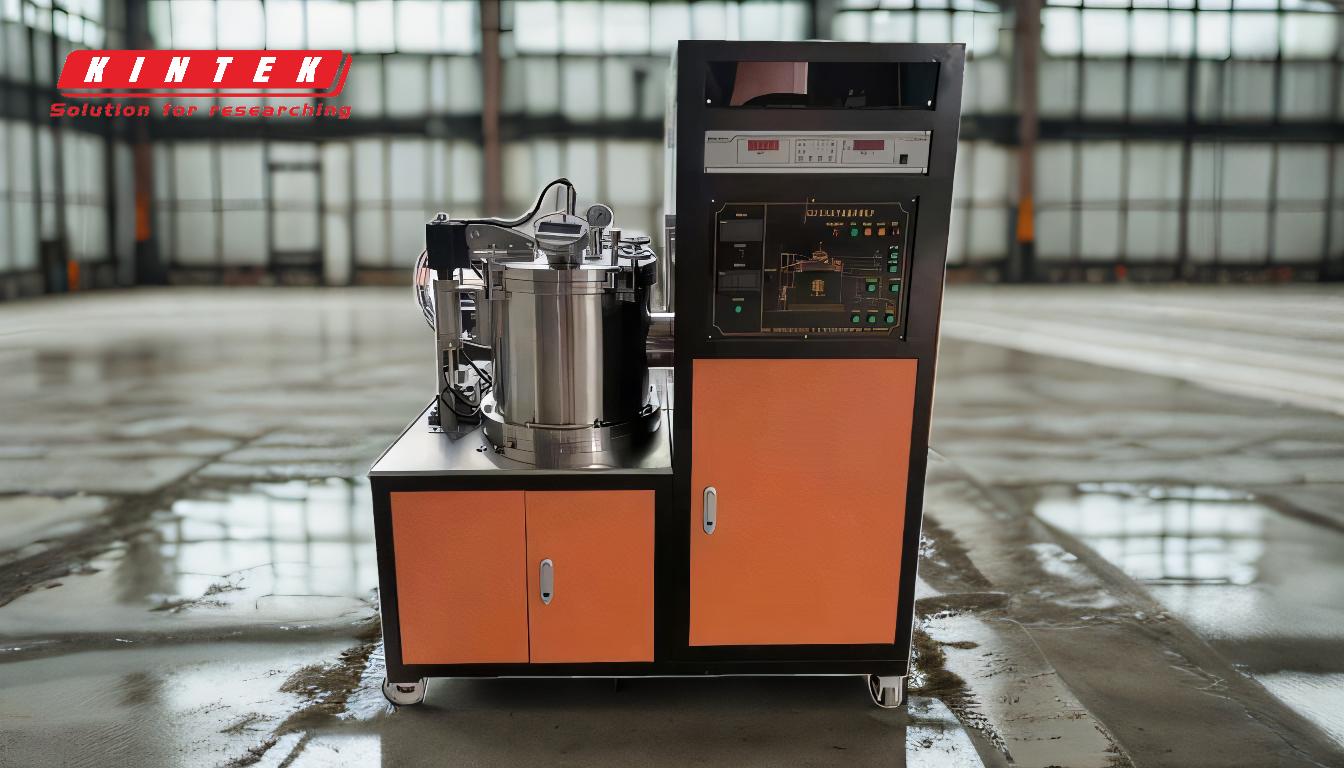
-
Efficiency Compared to Traditional Methods:
- Induction heating systems are more efficient than traditional open-hearth furnaces. They use high-voltage coils to produce frequencies between 50 Hz and 10,000 Hz, enabling rapid heating and higher thermal efficiency.
- This results in better yields, less burning loss, reduced metal melting time, and superior steel production.
- Unlike gas furnaces, electric furnaces, and salt baths, which rely on heat transfer through convection and radiation, induction heating generates heat directly within the material, reducing energy loss.
-
Factors Influencing Efficiency:
- Material Properties: The type of material, size, thickness, and resistivity significantly impact heating efficiency. Conductive materials with higher resistivity heat faster, while smaller and thinner materials require less energy.
- Frequency of Alternating Current: Higher frequencies result in shallower heating depths, allowing for precise control over the heating process.
- Inductor Coil Design: Special coil shapes and designs can enhance efficiency by optimizing the magnetic field and heat distribution.
- Power Supply Capacity: The system must account for the material's specific heat, mass, required temperature rise, and heat loss due to conduction, convection, and radiation.
-
Advancements in Technology:
- Improvements in semiconductor technology are expected to further enhance the efficiency of induction heating systems.
- Innovations in coil design and power supply systems aim to increase both performance and reliability.
-
Applications and Benefits:
- Induction heating is characterized by its speed, cost-effectiveness, compact size, and minimal space requirements.
- It is widely used in metal melting, forging, and heat treatment processes, offering precise temperature control and reduced energy consumption.
- The method is particularly advantageous for applications requiring rapid and localized heating, such as in the automotive and aerospace industries.
-
Energy Efficiency and Environmental Impact:
- Induction heating minimizes heat loss by generating heat directly within the material, making it more energy-efficient than methods relying on external heat sources.
- The reduced burning loss and shorter processing times contribute to lower energy consumption and a smaller environmental footprint.
-
Challenges and Considerations:
- The efficiency of induction heating depends on the specific application and the degree of temperature variation required.
- Factors like the presence of impurities, slags, and oxidants in the material can affect the heating process and overall efficiency.
- Proper system design, including the selection of appropriate frequencies and coil configurations, is crucial for maximizing efficiency.
In summary, induction heating is a highly efficient and versatile method for heating conductive materials, offering significant advantages over traditional heating techniques. Its efficiency is influenced by material properties, system design, and technological advancements, making it a preferred choice for various industrial applications.
Summary Table:
Aspect | Induction Heating | Traditional Methods |
---|---|---|
Heating Mechanism | Heat generated directly within the material | Relies on convection and radiation |
Efficiency | Higher thermal efficiency, less energy loss | Lower efficiency due to external heat transfer |
Speed | Rapid heating, shorter processing times | Slower heating process |
Precision | Precise temperature control and localized heating | Limited precision and control |
Energy Consumption | Reduced energy consumption, lower environmental impact | Higher energy consumption |
Applications | Ideal for metal melting, forging, heat treatment, automotive, and aerospace industries | Suitable for general-purpose heating |
Ready to enhance your industrial heating process? Contact us today to learn more about induction heating solutions!