Induction furnaces are capable of reaching extremely high temperatures, typically ranging from 1600°C to 2000°C, depending on the design, size, and inductive coupling efficiency. Smaller induction furnaces generally max out around 1600°C, while larger or more advanced systems can achieve temperatures up to 2000°C or more. The specific temperature achieved depends on factors such as the power input, coil design, and the materials being melted. These high temperatures make induction furnaces suitable for melting a wide range of metals, including steel, iron, and other high-melting-point alloys.
Key Points Explained:
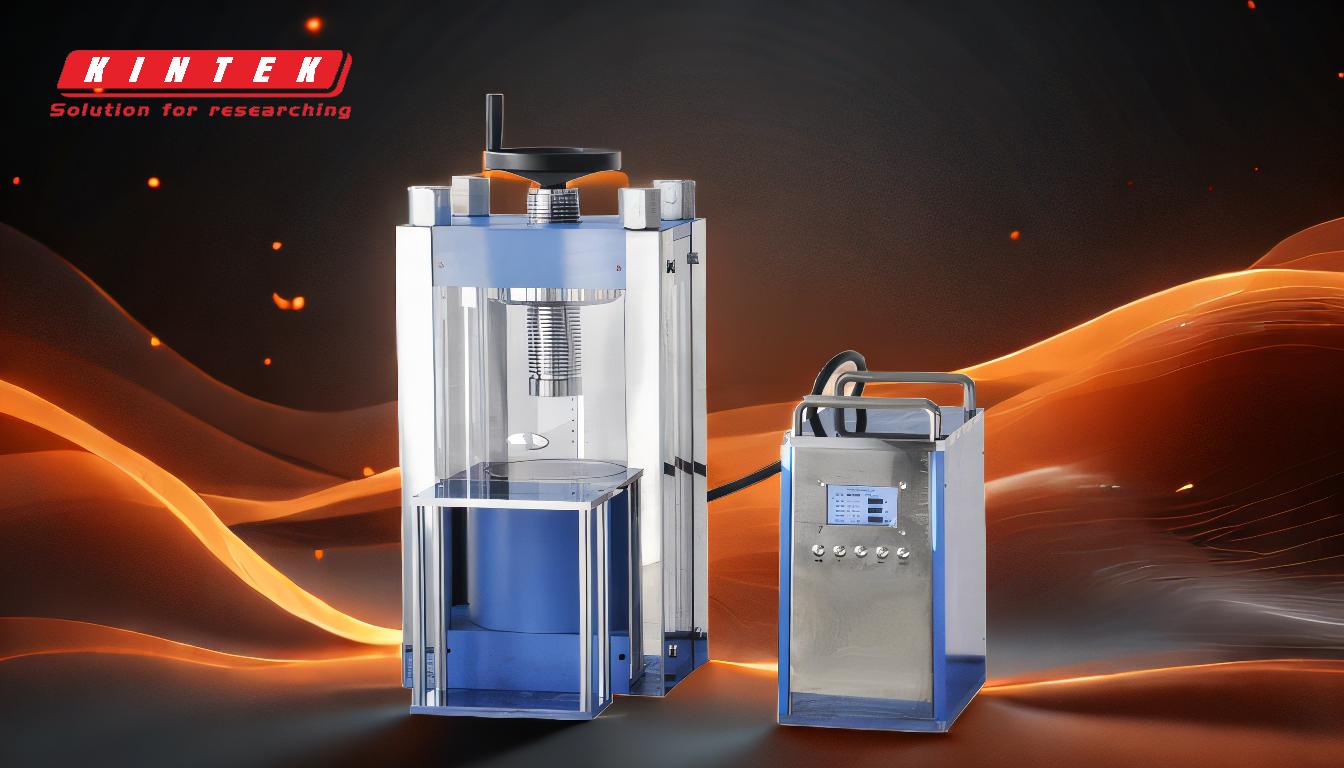
-
Temperature Range of Induction Furnaces:
- Induction furnaces can reach temperatures between 1600°C and 2000°C.
- Smaller furnaces typically max out at 1600°C (2900°F), while larger or more advanced systems can achieve 2000°C or higher.
- The exact temperature depends on the furnace design, power input, and the materials being processed.
-
Factors Influencing Maximum Temperature:
- Inductive Coupling: The efficiency of energy transfer between the induction coil and the charge materials plays a critical role. Better coupling allows for higher temperatures.
- Power Input: Higher power input enables the furnace to reach and sustain higher temperatures.
- Coil Design: The design and quality of the induction coil affect heat generation and distribution.
- Material Properties: The type of material being melted (e.g., steel, iron, or other alloys) influences the required temperature and the furnace's ability to achieve it.
-
Applications of High-Temperature Induction Furnaces:
- Induction furnaces are widely used in industries requiring high-temperature melting, such as:
- Steel and iron production.
- Melting of non-ferrous metals like copper, aluminum, and their alloys.
- Specialized applications in aerospace, automotive, and electronics manufacturing.
- Induction furnaces are widely used in industries requiring high-temperature melting, such as:
-
Advantages of Induction Furnaces at High Temperatures:
- Precision: Induction furnaces provide precise temperature control, which is critical for producing high-quality metals.
- Efficiency: They offer high energy efficiency due to direct heating of the charge materials.
- Cleanliness: Induction melting produces fewer impurities compared to traditional methods like arc furnaces.
-
Limitations and Considerations:
- Size Constraints: Smaller furnaces may not achieve the highest temperatures due to power and design limitations.
- Material Compatibility: Not all materials can withstand the extreme temperatures of induction furnaces, so refractory materials must be carefully selected.
- Cost: High-power induction furnaces capable of reaching 2000°C or more can be expensive to operate and maintain.
-
Comparison with Other Furnace Types:
- Induction furnaces generally outperform traditional furnaces (e.g., cupola or reverberatory furnaces) in terms of temperature control and efficiency.
- However, they may require higher initial investment and more specialized maintenance.
In summary, induction furnaces are versatile and powerful tools capable of reaching temperatures up to 2000°C, making them ideal for high-temperature melting applications. Their performance depends on factors like inductive coupling, power input, and material properties, and they offer significant advantages in precision, efficiency, and cleanliness. However, their limitations, such as size constraints and operational costs, should also be considered when selecting a furnace for specific applications.
Summary Table:
Aspect | Details |
---|---|
Temperature Range | 1600°C to 2000°C (smaller furnaces max at 1600°C, larger ones reach 2000°C+) |
Key Influencing Factors | Inductive coupling, power input, coil design, material properties |
Applications | Steel/iron production, non-ferrous metal melting, aerospace, automotive |
Advantages | Precision, energy efficiency, cleanliness |
Limitations | Size constraints, material compatibility, operational costs |
Need a high-temperature induction furnace for your application? Contact us today to find the perfect solution!