Hot forging and cold forging are two distinct metalworking processes with unique characteristics, advantages, and disadvantages. Hot forging involves shaping metal at high temperatures, typically above its recrystallization point, while cold forging is performed at or near room temperature. The choice between these methods depends on factors such as material properties, desired part complexity, production volume, and cost considerations. Below is a detailed comparison of the two processes, focusing on their differences, applications, and limitations.
Key Points Explained:
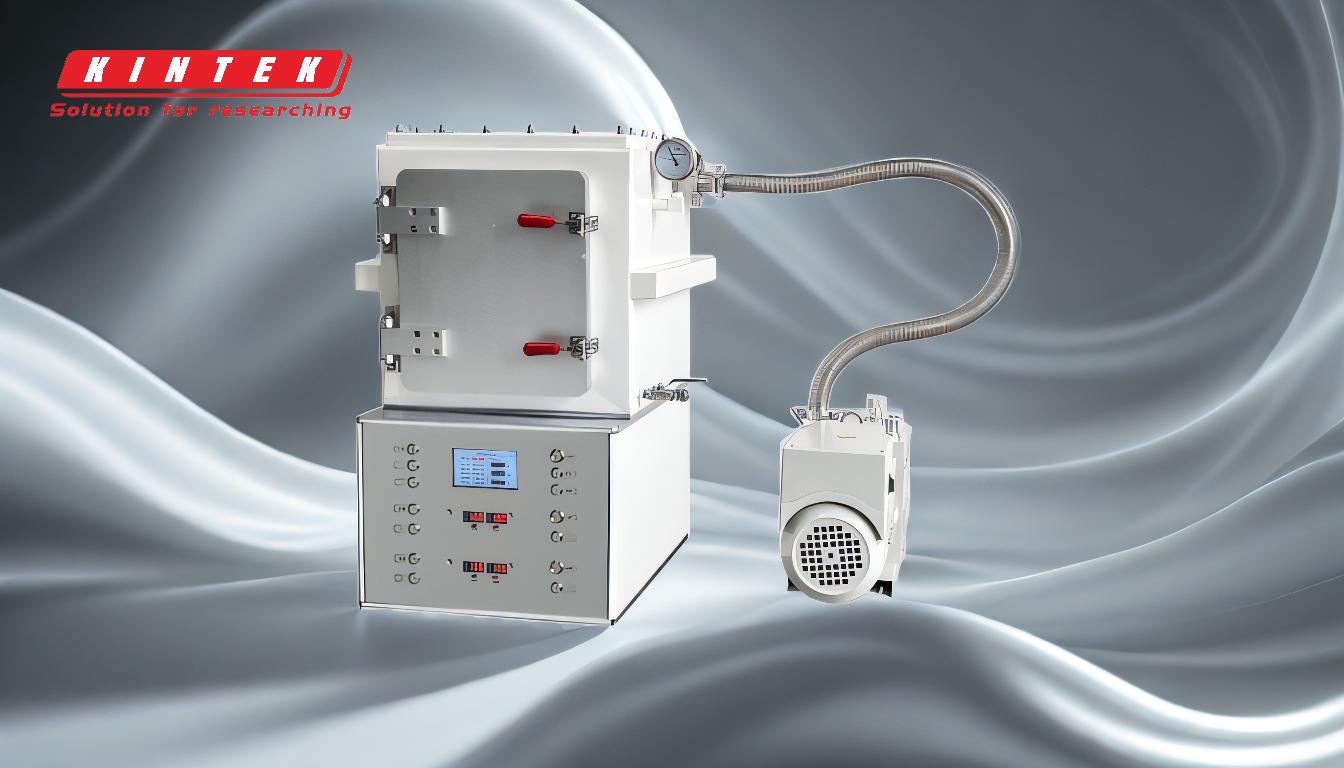
-
Temperature and Material Behavior:
- Hot Forging: Performed at temperatures above the metal's recrystallization point, typically between 950°C and 1250°C for steel. This high temperature reduces the metal's yield strength, making it easier to shape and deform. The process also refines the grain structure, improving mechanical properties like toughness and ductility.
- Cold Forging: Conducted at or near room temperature. The metal retains its high yield strength, requiring more force to deform. Cold forging enhances the material's strength through strain hardening but may reduce ductility.
-
Microstructure and Mechanical Properties:
- Hot Forging: Results in a refined and uniform grain structure due to recrystallization during the process. This improves the material's toughness and fatigue resistance, making it suitable for high-stress applications.
- Cold Forging: Leads to strain hardening, which increases the material's strength and hardness. However, the lack of recrystallization can result in residual stresses and reduced ductility, potentially requiring annealing to restore material properties.
-
Part Complexity and Precision:
- Hot Forging: Better suited for larger, less complex parts due to the metal's flow characteristics at high temperatures. Achieving tight tolerances is challenging, often necessitating secondary machining.
- Cold Forging: Capable of producing smaller, more intricate parts with higher precision and better surface finish. This reduces the need for additional machining, making it cost-effective for high-volume production.
-
Tooling and Die Costs:
- Hot Forging: Dies are subjected to extreme temperatures and wear, requiring frequent maintenance or replacement. This increases tooling costs, making hot forging less economical for small production runs.
- Cold Forging: Dies experience less thermal stress, resulting in longer tool life. However, the initial die design and manufacturing costs can be high, making it more suitable for large-scale production.
-
Material Suitability:
- Hot Forging: Ideal for metals with high deformation resistance, such as steel, titanium, and nickel alloys. It is also used for materials that are difficult to shape at lower temperatures.
- Cold Forging: Best suited for softer metals like aluminum, copper, and low-carbon steels, which can be easily deformed without excessive force.
-
Energy Consumption and Environmental Impact:
- Hot Forging: Requires significant energy to heat the metal to high temperatures, resulting in higher energy consumption and environmental impact.
- Cold Forging: More energy-efficient as it does not require heating, making it a greener alternative.
-
Applications:
- Hot Forging: Commonly used in industries requiring high-strength components, such as aerospace, automotive (e.g., crankshafts, connecting rods), and heavy machinery.
- Cold Forging: Preferred for producing fasteners, bolts, screws, and other small, high-precision components in the automotive and electronics industries.
-
Limitations:
- Hot Forging: Limited control over microstructure, higher secondary machining requirements, and inability to produce porous or multi-material parts. Die costs make it unsuitable for short production runs.
- Cold Forging: Restricted to softer metals and simpler geometries. Strain hardening may necessitate additional heat treatment to restore ductility.
In summary, hot forging and cold forging each have distinct advantages and limitations. Hot forging is ideal for large, high-strength components with refined grain structures, while cold forging excels in producing small, precise parts with minimal machining. The choice between the two depends on the specific requirements of the application, including material properties, part complexity, and production volume.
Summary Table:
Aspect | Hot Forging | Cold Forging |
---|---|---|
Temperature | Above recrystallization point (950°C–1250°C for steel) | At or near room temperature |
Material Behavior | Reduced yield strength, refined grain structure, improved toughness and ductility | High yield strength, strain hardening, increased strength, reduced ductility |
Part Complexity | Suitable for larger, less complex parts | Ideal for smaller, intricate parts with high precision |
Tooling Costs | Higher due to extreme temperatures and wear | Lower thermal stress, longer tool life, but high initial die costs |
Material Suitability | Steel, titanium, nickel alloys | Aluminum, copper, low-carbon steels |
Energy Consumption | High energy usage due to heating | Energy-efficient, no heating required |
Applications | Aerospace, automotive (crankshafts, connecting rods), heavy machinery | Fasteners, bolts, screws, automotive, electronics |
Limitations | Limited microstructure control, secondary machining, high die costs | Restricted to softer metals, strain hardening may require annealing |
Need help choosing the right forging process for your project? Contact our experts today!