Pyrolysis oil, also known as bio-crude or bio-oil, is a synthetic fuel produced through the thermal decomposition of biomass or plastic waste in the absence of oxygen. The process involves heating the feedstock to high temperatures (typically around 500°C or 900°F) in a reactor, followed by rapid cooling to condense the vapors into liquid oil. The resulting oil has a high oxygen content and is distinct from traditional petroleum products. The process also generates non-condensable gases and solid residues, which can be recycled or treated to minimize environmental impact. Below, we break down the key steps and considerations in the production of pyrolysis oil.
Key Points Explained:
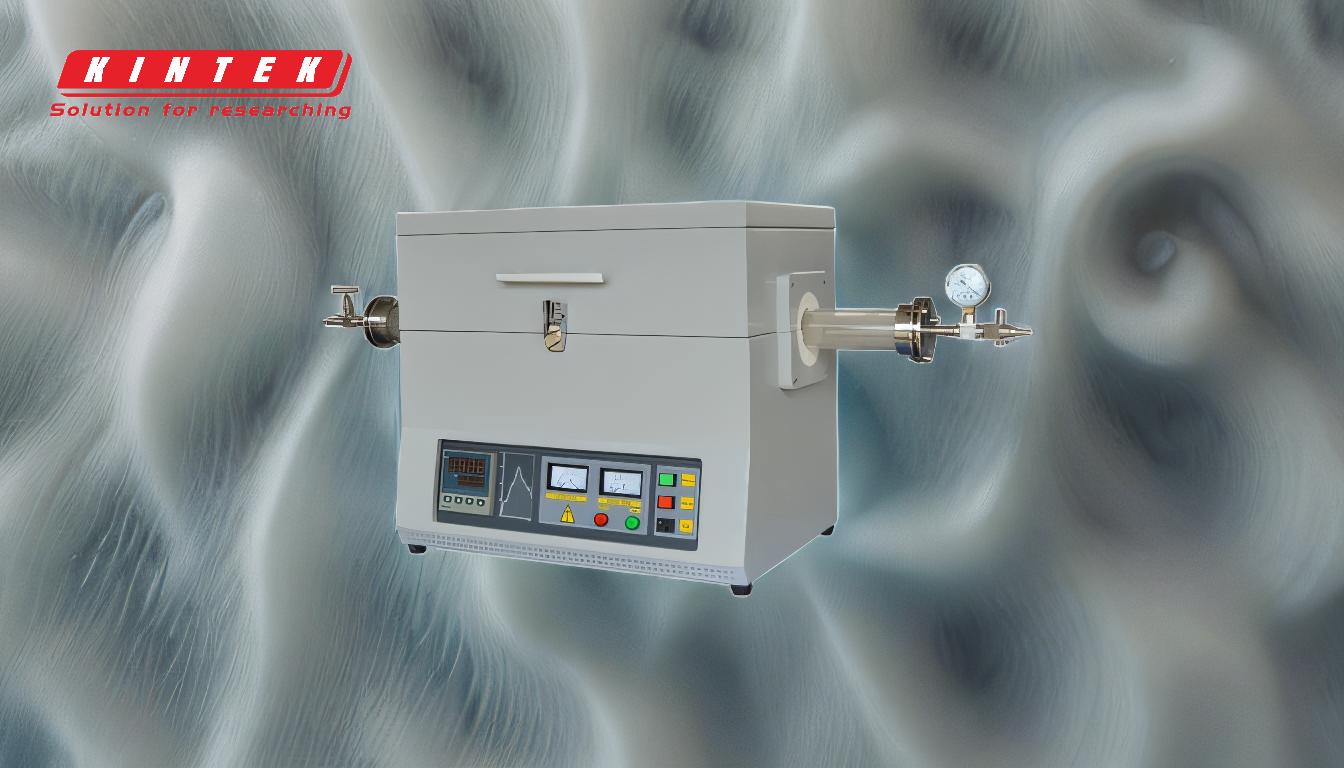
-
Feedstock Preparation
- The first step involves selecting and preparing the feedstock, which can be biomass (e.g., wood, agricultural residues) or plastic waste.
- For biomass, the feedstock is dried to reduce moisture content, as excess water can hinder the pyrolysis process.
- For plastic waste, the material is shredded, cleaned, and preprocessed to remove non-plastic impurities like metals or dirt.
- Proper feedstock preparation ensures efficient pyrolysis and higher-quality oil output.
-
Pyrolysis Reactor Setup
- The prepared feedstock is fed into a pyrolysis reactor, which operates in an oxygen-free environment to prevent combustion.
- The reactor is heated to temperatures ranging from 200°C to 900°C, depending on the feedstock and desired output.
- Heat sources can include coal, wood, natural gas, fuel oil, or electricity, depending on the availability and cost.
-
Thermal Decomposition
- Inside the reactor, the feedstock undergoes thermal decomposition, breaking down into smaller molecules.
- This process produces three main products:
- Pyrolysis oil (bio-oil): A liquid condensate formed by cooling the vapors.
- Non-condensable gases: Such as methane, ethane, propane, and butane, which can be recycled to heat the reactor.
- Solid residue (biochar): A carbon-rich material that settles at the bottom of the reactor.
-
Condensation and Liquefaction
- The vapors produced during pyrolysis are passed through cooling pipes and condensers, where they are liquefied into pyrolysis oil.
- The cooling process is critical to ensure the efficient conversion of vapors into liquid oil.
-
Distillation and Purification
- The raw pyrolysis oil may contain impurities and require further refining.
- Distillation involves heating the oil to separate it into different fractions based on boiling points.
- Purification steps may include filtration or chemical treatments to remove contaminants and improve oil quality.
-
Recycling and Environmental Considerations
- Non-condensable gases produced during pyrolysis are often recycled to provide heat for the reactor, improving energy efficiency.
- Smoke and exhaust gases are treated using dedusting systems and emission control technologies to minimize environmental pollution.
- Solid residues like biochar can be used as a soil amendment or for other industrial applications.
-
Storage and Dispatch
- The final pyrolysis oil is stored in tanks or containers for transportation and use.
- Proper storage conditions are essential to maintain the oil's stability and prevent degradation.
Summary of the Process:
Pyrolysis oil is made by heating biomass or plastic waste in an oxygen-free environment, causing thermal decomposition into vapors, gases, and solid residues. The vapors are condensed into liquid oil, which is then distilled and purified for use as fuel. The process is energy-efficient, as non-condensable gases are recycled to heat the reactor, and environmental impacts are minimized through emission control systems. This method offers a sustainable alternative to fossil fuels, utilizing renewable or waste materials to produce synthetic fuel.
Summary Table:
Step | Description |
---|---|
Feedstock Preparation | Select and prepare biomass or plastic waste; dry biomass or clean plastic. |
Pyrolysis Reactor Setup | Heat feedstock in an oxygen-free reactor (200°C–900°C) to prevent combustion. |
Thermal Decomposition | Break down feedstock into pyrolysis oil, non-condensable gases, and biochar. |
Condensation & Liquefaction | Cool vapors to condense into liquid pyrolysis oil. |
Distillation & Purification | Refine oil to remove impurities and improve quality. |
Recycling & Environmental | Recycle gases for heat; treat emissions; use biochar as soil amendment. |
Storage & Dispatch | Store purified oil in tanks for transportation and use. |
Discover how pyrolysis oil can transform waste into sustainable fuel—contact us today to learn more!