Sintering temperature is typically much lower than the melting temperature of the material being sintered. This is because sintering relies on the application of heat and pressure to fuse particles together without reaching the point of liquefaction. By operating below the melting point, sintering preserves the structural integrity of the material, saves energy, and allows for greater control over the final product. This distinction is crucial for materials with high melting points, as sintering provides a more energy-efficient and practical alternative to melting.
Key Points Explained:
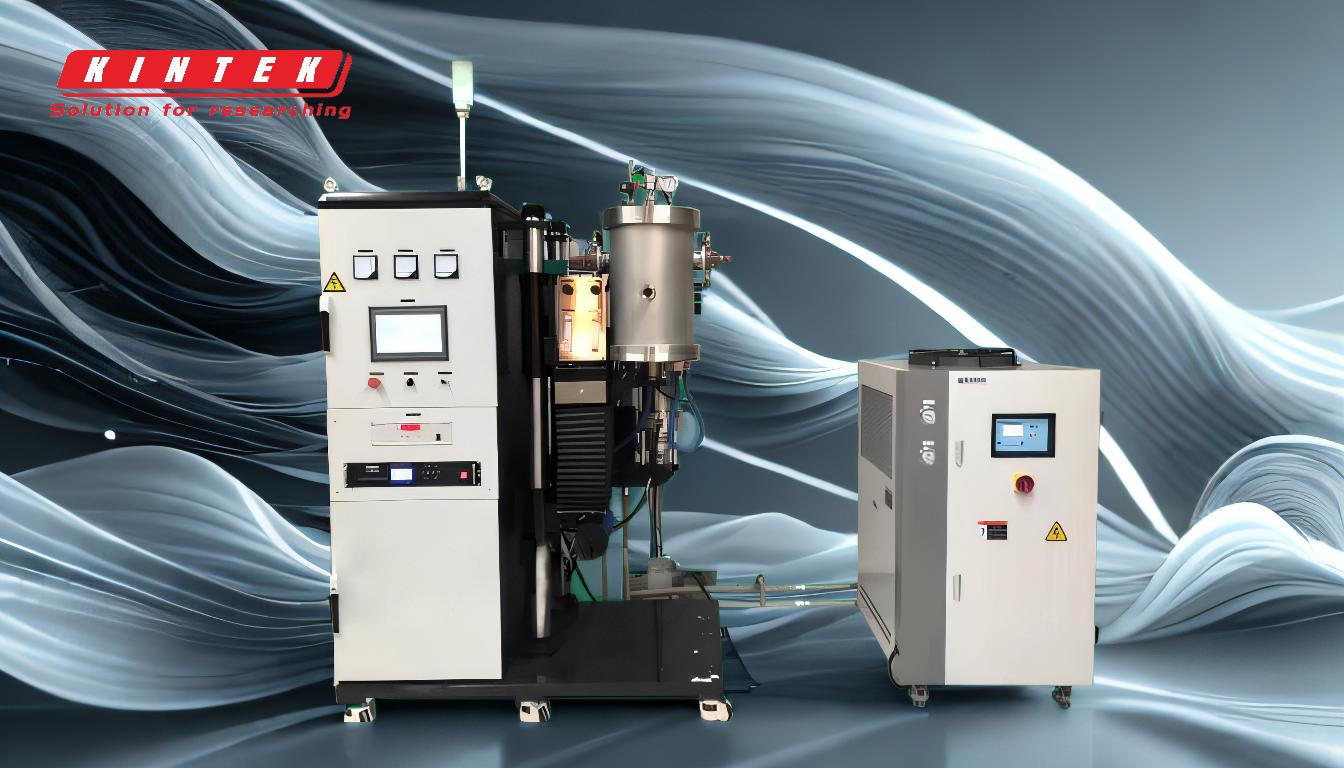
-
Sintering Temperature is Below Melting Temperature:
- Sintering occurs at temperatures significantly lower than the melting point of the material. This is a fundamental characteristic of the sintering process, as it avoids liquefaction while still enabling particle fusion.
- For example, if a metal has a melting point of 1500°C, sintering might be conducted at 1200°C or lower, depending on the material and process requirements.
-
Energy Efficiency:
- Since sintering operates at lower temperatures, it consumes less energy compared to melting, which requires heating the material to its full melting point.
- This makes sintering a more sustainable and cost-effective method, especially for materials with high melting points.
-
Preservation of Structural Integrity:
- By avoiding liquefaction, sintering prevents the material from losing its shape or structural properties. This is particularly important for creating complex shapes or maintaining specific material characteristics.
- For instance, in powder metallurgy, sintering allows for the creation of strong, durable components without compromising their design.
-
Role of Pressure in Sintering:
- Sintering combines heat with pressure to facilitate particle bonding. The application of pressure compensates for the lower temperature, ensuring effective fusion without the need for melting.
- This combination of heat and pressure is what distinguishes sintering from other processes like melting or casting.
-
Control Over Final Product:
- Operating below the melting point provides greater control over the microstructure and properties of the final product. This is crucial for applications requiring precise material characteristics, such as in aerospace or medical devices.
- For example, sintering can be fine-tuned to achieve specific densities, porosities, or mechanical properties.
-
Practical Applications:
- Sintering is widely used in industries where high melting points or material integrity are critical. Examples include ceramic manufacturing, metal powder processing, and composite material production.
- Its ability to work with high-melting-point materials, such as tungsten or ceramics, makes it indispensable in advanced manufacturing.
-
Comparison with Melting:
- Melting requires temperatures above the material's melting point, leading to complete liquefaction. This process is energy-intensive and often results in loss of structural control.
- In contrast, sintering offers a more controlled and efficient alternative, particularly for materials that are difficult or impractical to melt.
By understanding the relationship between sintering temperature and melting temperature, manufacturers can optimize their processes for energy efficiency, material integrity, and product quality. This distinction is key to leveraging sintering as a versatile and effective manufacturing technique.
Summary Table:
Key Aspect | Details |
---|---|
Temperature Range | Sintering occurs below melting point, e.g., 1200°C vs. 1500°C for metals. |
Energy Efficiency | Lower temperatures reduce energy consumption compared to melting. |
Structural Integrity | Avoids liquefaction, preserving shape and material properties. |
Role of Pressure | Combines heat and pressure for effective particle bonding. |
Control Over Final Product | Enables fine-tuning of density, porosity, and mechanical properties. |
Applications | Used in ceramics, metal powders, and composites for high-melting materials. |
Comparison with Melting | More energy-efficient and practical for materials with high melting points. |
Want to optimize your sintering process? Contact our experts today for tailored solutions!