Chemical Vapor Deposition (CVD) reactors can be categorized into several types based on different parameters such as operating conditions, physical characteristics of the vapor, and substrate heating methods. The primary classification includes Atmospheric Pressure CVD (APCVD), Low Pressure CVD (LPCVD), Ultrahigh Vacuum CVD (UHVCVD), Plasma-Enhanced CVD (PECVD), Metal-Organic CVD (MOCVD), and others like Laser CVD (LCVD) and Photochemical CVD (PCVD). Each type has distinct operational characteristics and applications, making them suitable for specific industrial and research needs.
Key Points Explained:
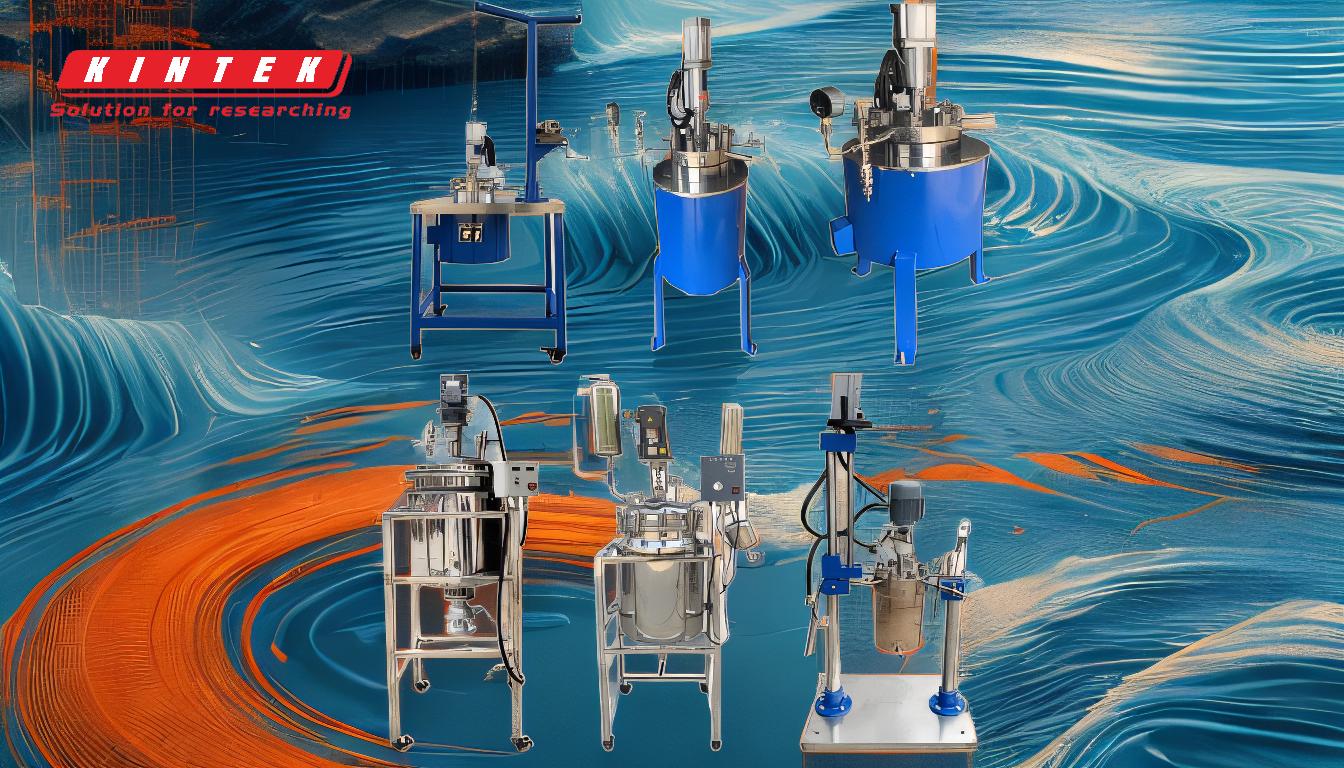
-
Classification by Operating Conditions:
- Atmospheric Pressure CVD (APCVD): Operates at atmospheric pressure, suitable for large-scale production due to simpler equipment requirements.
- Low Pressure CVD (LPCVD): Operates at reduced pressures, providing better film uniformity and step coverage, commonly used in semiconductor manufacturing.
- Ultrahigh Vacuum CVD (UHVCVD): Operates at extremely low pressures, ideal for high-purity film deposition with minimal contamination.
- Sub-atmospheric CVD (SACVD): Operates at pressures slightly below atmospheric, balancing between APCVD and LPCVD in terms of film quality and deposition rate.
-
Classification by Physical Characteristics of Vapor:
- Aerosol-Assisted CVD (AACVD): Uses aerosols to deliver precursors, enabling the deposition of complex materials.
- Direct Liquid Injection CVD (DLICVD): Involves injecting liquid precursors directly into the reactor, allowing precise control over precursor delivery and composition.
-
Classification by Substrate Heating:
- Hot Wall CVD: The entire reactor chamber is heated, providing uniform temperature distribution but potentially leading to unwanted reactions on chamber walls.
- Cold Wall CVD: Only the substrate is heated, reducing unwanted reactions on chamber walls and improving film purity.
-
Other Specialized CVD Types:
- Plasma-Enhanced CVD (PECVD): Utilizes plasma to enhance chemical reactions, allowing deposition at lower temperatures, beneficial for temperature-sensitive substrates.
- Metal-Organic CVD (MOCVD): Uses metal-organic precursors, commonly used for depositing compound semiconductors like GaN and InP.
- Laser CVD (LCVD): Employs laser beams to locally heat the substrate, enabling precise and localized deposition.
- Photochemical CVD (PCVD): Uses ultraviolet light to initiate chemical reactions, suitable for depositing films at low temperatures.
- Chemical Vapor Infiltration (CVI): Specifically used for infiltrating porous substrates to create composite materials.
- Chemical Beam Epitaxy (CBE): A variation of CVD used for high-precision epitaxial growth of semiconductor layers.
-
Additional Variants:
- Atomic Layer Deposition (ALD): A precise form of CVD where films are deposited one atomic layer at a time, providing excellent thickness control and conformality.
- Hybrid Physical-Chemical Vapor Deposition (HPCVD): Combines physical and chemical vapor deposition techniques, offering unique material properties.
Each type of CVD reactor has its own set of advantages and limitations, making them suitable for specific applications ranging from microelectronics to advanced materials science. Understanding these classifications helps in selecting the appropriate CVD process for a given material and application.
Summary Table:
Classification | Types | Key Characteristics |
---|---|---|
By Operating Conditions | APCVD, LPCVD, UHVCVD, SACVD | Pressure levels, film quality, and deposition rates vary. |
By Physical Characteristics | AACVD, DLICVD | Uses aerosols or liquid precursors for precise material deposition. |
By Substrate Heating | Hot Wall CVD, Cold Wall CVD | Heating methods impact temperature uniformity and film purity. |
Specialized CVD Types | PECVD, MOCVD, LCVD, PCVD, CVI, CBE | Unique techniques for specific applications like low-temperature deposition or epitaxy. |
Additional Variants | ALD, HPCVD | Advanced methods for atomic-level precision and hybrid material properties. |
Need help selecting the right CVD reactor for your application? Contact our experts today!