Induction furnaces are primarily categorized into two main types: coreless induction furnaces and channel (core-type) induction furnaces. These types are designed to meet specific industrial needs, with coreless furnaces being more versatile for a wide range of applications, including steelmaking, while channel furnaces are typically used for melting low melting point alloys or as holding and superheating units for higher melting point alloys like cast iron. Both types are known for their efficiency in melting and alloying metals with minimal melt losses, though they offer limited refining capabilities.
Key Points Explained:
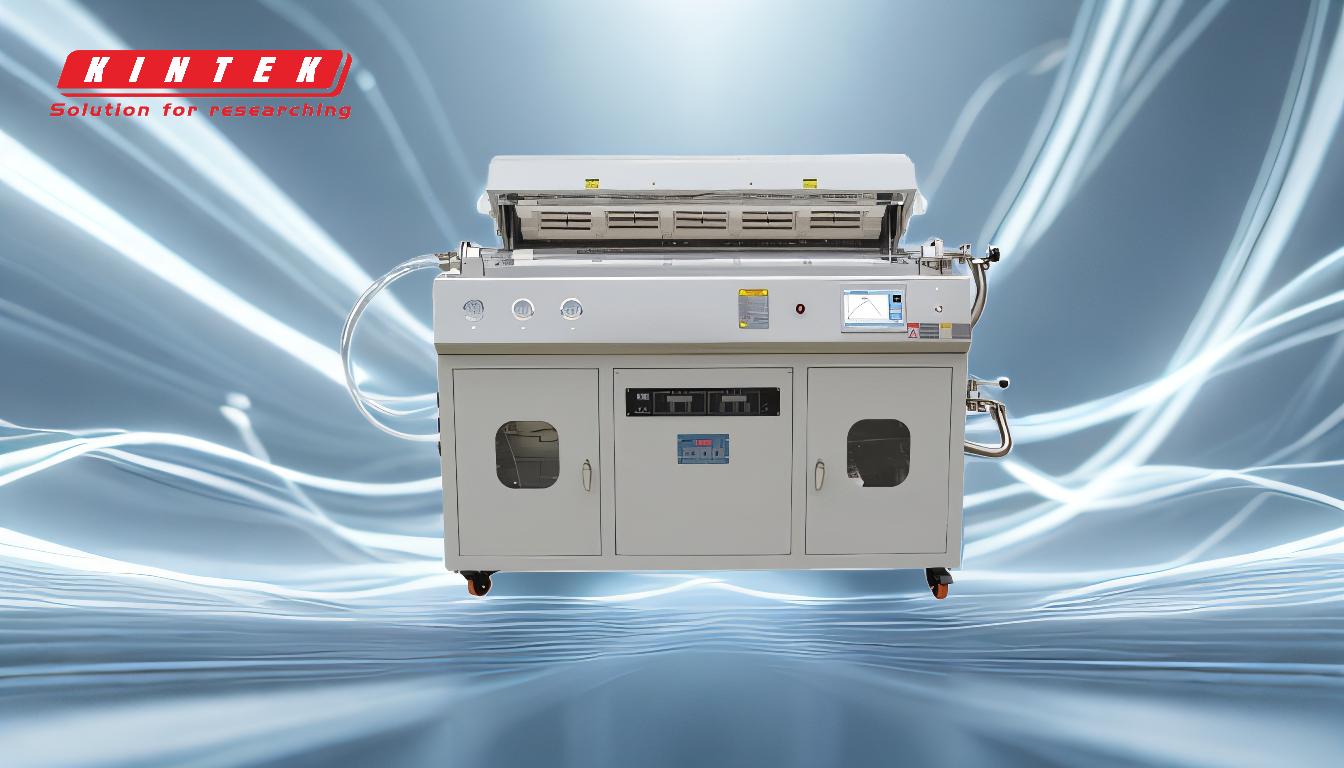
-
Coreless Induction Furnace:
- Design and Functionality: Coreless induction furnaces do not have a core, which allows for a more uniform heating process. They are highly versatile and can be used for melting a wide range of metals, including steel, iron, and non-ferrous metals.
- Applications: These furnaces are commonly used in steelmaking, foundries, and for the production of alloys. Their ability to handle a broad spectrum of materials makes them indispensable in industries requiring flexibility.
- Advantages: Coreless furnaces offer rapid heating, precise temperature control, and are capable of handling large volumes of metal. They are also relatively easy to maintain and operate.
-
Channel (Core-Type) Induction Furnace:
- Design and Functionality: Channel induction furnaces feature a core, typically made of iron, which surrounds a channel filled with molten metal. This design allows for efficient heat transfer and is particularly suited for continuous melting processes.
- Applications: These furnaces are ideal for melting low melting point alloys and are often used as holding and superheating units for higher melting point alloys like cast iron. They are also used in applications where a steady supply of molten metal is required.
- Advantages: Channel furnaces are known for their energy efficiency and ability to maintain a consistent temperature. They are also capable of handling large volumes of metal with minimal melt losses.
-
IGBT Induction Furnace:
- Technology: The (igbt induction furnace)[/topic/igbt-induction-furnace] utilizes Insulated Gate Bipolar Transistor (IGBT) technology, which offers significant advantages in terms of energy efficiency and control. IGBT technology allows for precise control of the heating process, reducing energy consumption and improving overall furnace performance.
- Applications: IGBT induction furnaces are used in various industries, including metal processing, where precise temperature control and energy efficiency are critical. They are particularly beneficial in applications requiring high-frequency induction heating.
- Advantages: The use of IGBT technology results in lower operating costs, improved power factor, and reduced electromagnetic interference. These furnaces are also more compact and require less maintenance compared to traditional induction furnaces.
-
Comparison and Selection Criteria:
- Material Type: The choice between coreless and channel induction furnaces often depends on the type of material being processed. Coreless furnaces are more suitable for a wide range of metals, while channel furnaces are better for specific alloys.
- Production Volume: For high-volume production, coreless furnaces are generally preferred due to their ability to handle larger quantities of metal. Channel furnaces are more suited for continuous or steady-state operations.
- Energy Efficiency: Both types of furnaces are energy-efficient, but IGBT induction furnaces offer additional savings due to their advanced control systems.
- Maintenance and Operation: Coreless furnaces are easier to maintain and operate, making them a popular choice for many industries. Channel furnaces, while efficient, may require more specialized maintenance.
In conclusion, the selection of the appropriate type of induction furnace depends on the specific requirements of the application, including the type of material, production volume, and desired energy efficiency. Both coreless and channel induction furnaces offer unique advantages, and the integration of IGBT technology further enhances their performance and efficiency.
Summary Table:
Type | Design | Applications | Advantages |
---|---|---|---|
Coreless Induction | No core; uniform heating process | Steelmaking, foundries, alloy production | Rapid heating, precise temperature control, easy maintenance |
Channel (Core-Type) | Core with molten metal channel; efficient heat transfer | Low melting point alloys, holding/superheating units for cast iron | Energy efficiency, consistent temperature, minimal melt losses |
IGBT Induction | Uses IGBT technology for precise control | Metal processing, high-frequency induction heating | Lower operating costs, improved power factor, reduced maintenance |
Need help choosing the right induction furnace for your needs? Contact our experts today!