Physical vapor deposition (PVD) is a versatile technology used to deposit thin films onto substrates through physical processes rather than chemical reactions. Based on the references, PVD can be categorized into several methods, with the most common being sputtering, evaporation, and ion plating. These methods are further divided into subcategories, such as magnetron sputtering, thermal evaporation, electron-beam evaporation, and pulsed laser deposition. Each method has unique mechanisms and applications, making PVD a critical process in industries like semiconductor manufacturing, optics, and coatings. Below, the key types of PVD are explained in detail.
Key Points Explained:
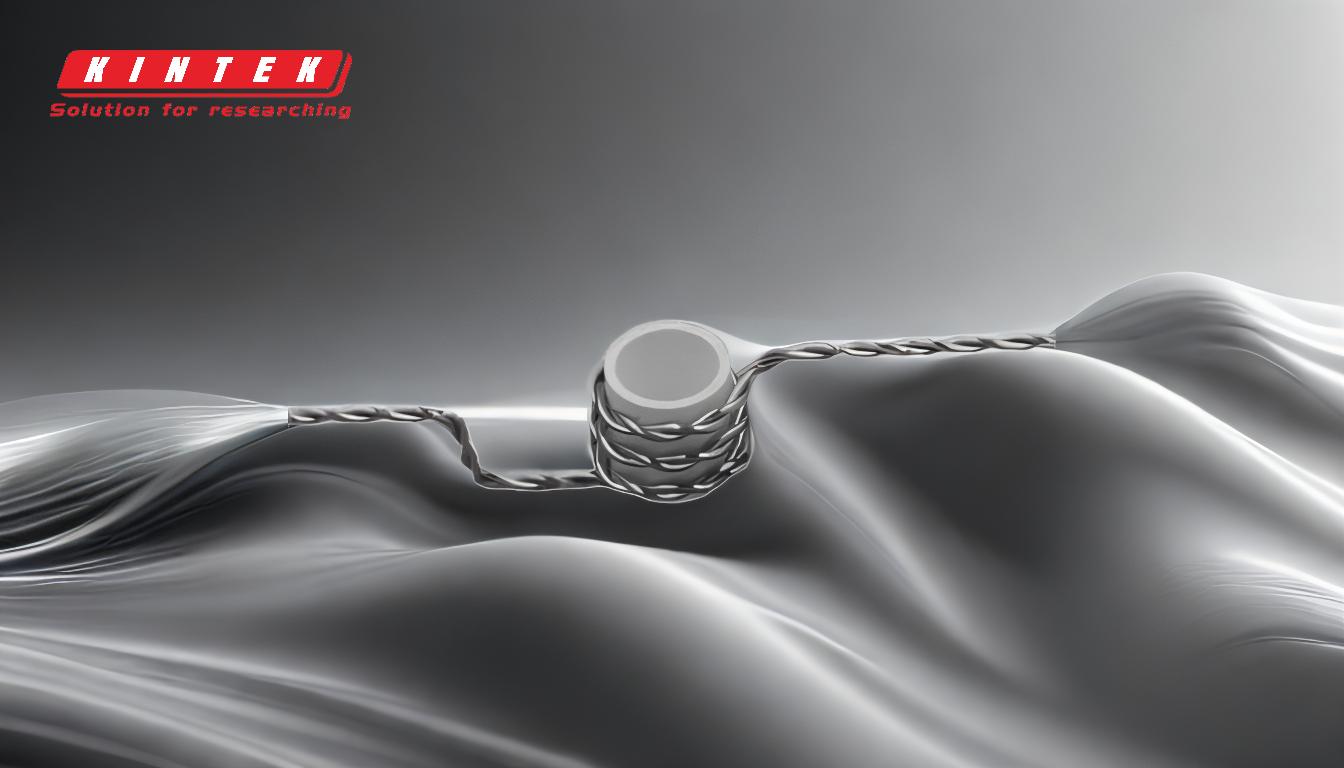
-
Sputtering
- Sputtering is one of the most widely used PVD methods, involving the ejection of atoms from a target material by bombarding it with high-energy ions.
-
Subtypes of Sputtering:
- Magnetron Sputtering: Uses magnetic fields to enhance the efficiency of the sputtering process, commonly used for depositing thin films in electronics and optics.
- Ion Beam Sputtering: Employs a focused ion beam to sputter material, offering precise control over film thickness and composition.
- Reactive Sputtering: Involves introducing reactive gases (e.g., oxygen) during the process to form compound films like oxides or nitrides.
- Gas Flow Sputtering: Utilizes a flowing gas to transport sputtered material to the substrate, often used for high-quality coatings.
-
Evaporation
- Evaporation methods involve heating a material until it vaporizes, and the vapor then condenses onto the substrate to form a thin film.
-
Subtypes of Evaporation:
- Thermal Evaporation: Uses resistive heating to vaporize the source material, suitable for depositing metals and simple compounds.
- Electron-Beam (E-Beam) Evaporation: Employs a focused electron beam to heat and vaporize the material, ideal for high-melting-point materials and precise film deposition.
- Pulsed Laser Deposition (PLD): A specialized form of evaporation where a laser vaporizes the target material, producing highly directed and ionized vapors for high-quality films.
-
Ion Plating
- Ion plating combines sputtering and evaporation with ionization of the vaporized material, enhancing film adhesion and density.
- This method is particularly useful for creating wear-resistant and corrosion-resistant coatings.
-
Molecular Beam Epitaxy (MBE)
- MBE is a highly controlled form of PVD used to grow single-crystal films layer by layer, primarily in semiconductor and nanotechnology applications.
-
Other PVD Methods
- Activated Reactive Evaporation (ARE): Combines evaporation with reactive gases to deposit compound films.
- Ionized Cluster Beam Deposition (ICBD): Uses ionized clusters of atoms to deposit films with improved properties.
- Laser Surface Alloying: A specialized PVD method for modifying surface properties using laser-induced vaporization.
In summary, PVD encompasses a variety of methods, each with distinct mechanisms and applications. The primary categories are sputtering, evaporation, and ion plating, with numerous subcategories tailored to specific industrial needs. Understanding these types helps in selecting the appropriate PVD technique for achieving desired film properties.
Summary Table:
PVD Method | Key Features | Applications |
---|---|---|
Sputtering | Ejects atoms from a target using high-energy ions; subtypes include magnetron, ion beam, reactive, and gas flow sputtering. | Electronics, optics, high-quality coatings. |
Evaporation | Vaporizes material via heating; subtypes include thermal, e-beam, and pulsed laser deposition. | Metals, high-melting-point materials, precise film deposition. |
Ion Plating | Combines sputtering and evaporation with ionization for enhanced film properties. | Wear-resistant and corrosion-resistant coatings. |
Molecular Beam Epitaxy (MBE) | Grows single-crystal films layer by layer with high precision. | Semiconductors, nanotechnology. |
Other PVD Methods | Includes ARE, ICBD, and laser surface alloying for specialized applications. | Compound films, improved film properties, surface modification. |
Need help selecting the right PVD method for your application? Contact our experts today!