PVD plating costs can vary significantly depending on whether you outsource the process or bring it in-house. Outsourcing to a coating service vendor can be expensive for small batches, with costs potentially around $20 per part or per batch. However, investing in PVD equipment and performing the process in-house can drastically reduce the cost per part over time. PVD plating is a versatile and durable coating method, offering benefits such as strong adhesion, high hardness, wear resistance, and corrosion resistance, making it a valuable investment for many industries.
Key Points Explained:
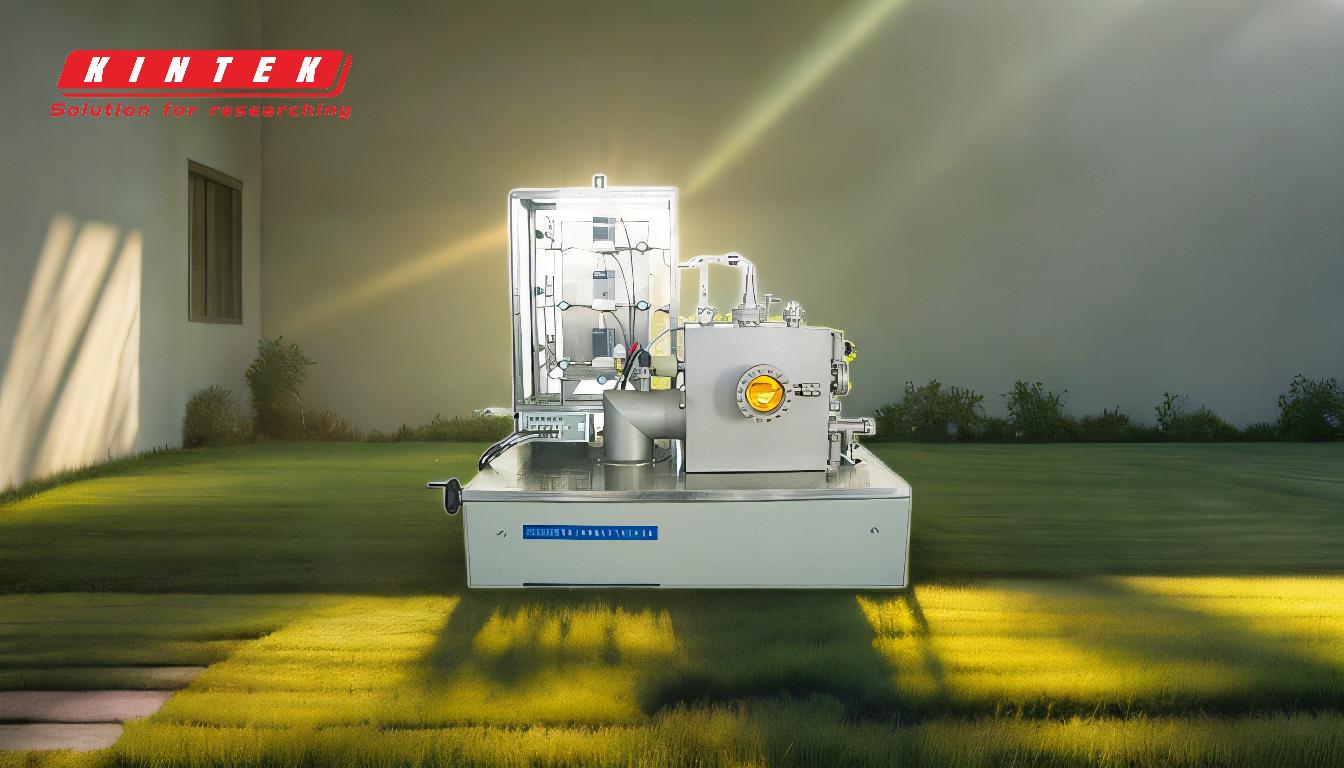
-
Cost Factors in PVD Plating:
- Outsourcing Costs: When outsourcing PVD plating, costs can be high for small volumes, often around $20 per part or per batch. This is due to the overhead costs of the service provider, including equipment maintenance, labor, and operational expenses.
- In-House Costs: Purchasing PVD equipment and performing the process in-house can significantly reduce the cost per part, especially for large volumes. The initial investment in equipment is offset by the long-term savings in per-part costs.
-
PVD Plating Process:
- Vacuum Chamber: The process involves placing the item to be coated in a vacuum chamber, where it is bombarded with ions or atoms of the coating material.
- Vaporization and Condensation: The coating material is vaporized and then condenses onto the surface of the item, forming a thin, durable layer.
-
Benefits of PVD Plating:
- Adhesion: PVD plating offers excellent adhesion to the base material, ensuring a long-lasting and durable coating.
- Hardness and Wear Resistance: The coatings are very hard and resistant to wear, making them ideal for applications where durability is critical.
- Corrosion Resistance: PVD coatings provide excellent resistance to corrosion, extending the life of the coated items.
- Versatility: A wide range of materials can be deposited using PVD, allowing for various colors, finishes, and functionalities.
-
Considerations for Purchasing PVD Equipment:
- Initial Investment: The upfront cost of PVD equipment can be substantial, but it is often justified by the long-term savings and increased control over the coating process.
- Operational Costs: In addition to the initial purchase, consider the costs of maintenance, training, and consumables.
- Volume of Work: The decision to bring PVD plating in-house should be based on the volume of work. High-volume operations are more likely to benefit from the investment in equipment.
-
Applications of PVD Plating:
- Industrial Applications: PVD plating is widely used in industries such as automotive, aerospace, and medical devices, where durability and performance are critical.
- Consumer Products: It is also used in consumer products like watches, jewelry, and electronics, where aesthetics and durability are important.
-
Cost Comparison:
- Outsourcing vs. In-House: For small batches, outsourcing may be more cost-effective, but for large volumes, in-house PVD plating can offer significant cost savings.
- Long-Term Savings: While the initial investment in PVD equipment is high, the long-term savings in per-part costs can make it a worthwhile investment for businesses with high coating needs.
In summary, the cost of PVD plating depends on whether you outsource the process or bring it in-house. Outsourcing can be expensive for small batches, but in-house PVD plating can offer significant cost savings for large volumes. PVD plating provides numerous benefits, including strong adhesion, high hardness, wear resistance, and corrosion resistance, making it a valuable investment for many industries.
Summary Table:
Aspect | Outsourcing | In-House |
---|---|---|
Cost per Part | ~$20 per part (small batches) | Reduced significantly over time |
Initial Investment | Low (no equipment purchase) | High (equipment purchase required) |
Operational Costs | Included in service fees | Maintenance, training, and consumables |
Volume Suitability | Small batches | Large volumes |
Long-Term Savings | Minimal | Substantial |
Ready to optimize your PVD plating costs? Contact us today to explore in-house solutions!