Hydraulic actuators are essential components in many industrial and mechanical systems, converting hydraulic energy into mechanical motion. The operating pressure of a hydraulic actuator, measured in pounds per square inch (PSI), is a critical factor that determines its performance, efficiency, and suitability for specific applications. Typically, hydraulic actuators operate within a range of 1,000 to 5,000 PSI, depending on the design, application, and system requirements. Understanding the factors that influence operating pressure, such as the type of actuator, load requirements, and system design, is crucial for selecting the right equipment and ensuring optimal performance.
Key Points Explained:
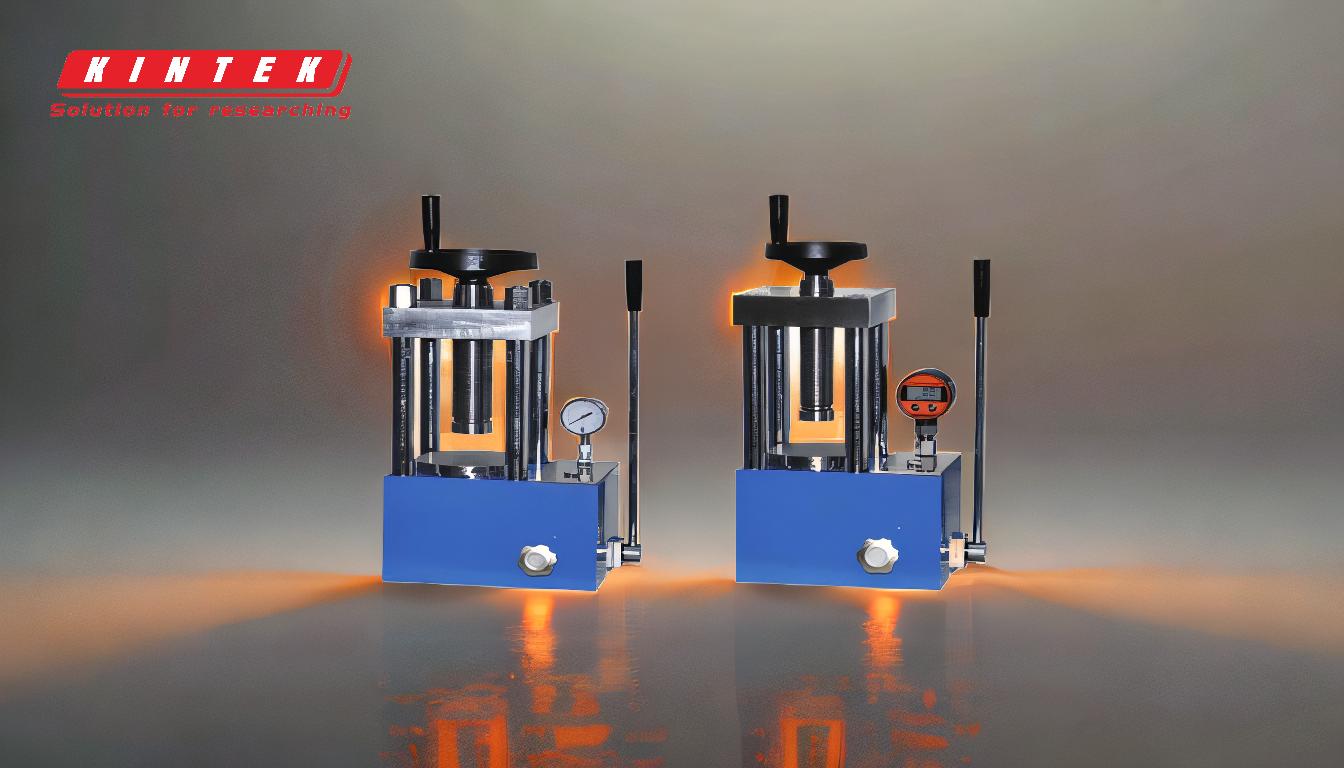
-
Typical Operating Pressure Range for Hydraulic Actuators:
- Hydraulic actuators generally operate within a pressure range of 1,000 to 5,000 PSI. This range is suitable for most industrial and mechanical applications, providing a balance between power output and system safety.
- Low-pressure systems (1,000–2,500 PSI) are often used in applications where precision and control are more critical than raw power, such as in robotics or light-duty machinery.
- High-pressure systems (2,500–5,000 PSI) are employed in heavy-duty applications, such as construction equipment, hydraulic presses, and aerospace systems, where greater force and power are required.
-
Factors Influencing Operating Pressure:
- Type of Actuator: Different types of hydraulic actuators, such as linear actuators (cylinders) and rotary actuators, have varying pressure requirements. For example, linear actuators used in heavy machinery often operate at higher pressures compared to rotary actuators in precision systems.
- Load Requirements: The force or torque required to move a load directly impacts the operating pressure. Heavier loads necessitate higher pressures to achieve the desired motion.
- System Design: The design of the hydraulic system, including the pump, valves, and hoses, plays a significant role in determining the operating pressure. Systems with high-pressure components can safely operate at higher PSI levels.
- Safety and Efficiency: Operating within the recommended pressure range ensures system safety and efficiency. Exceeding the rated pressure can lead to equipment failure, while operating below the required pressure may result in insufficient performance.
-
Applications and Their Pressure Requirements:
- Industrial Machinery: Hydraulic presses, stamping machines, and injection molding equipment often operate at pressures between 2,000 and 5,000 PSI to generate the necessary force for heavy-duty tasks.
- Construction Equipment: Excavators, bulldozers, and cranes typically use hydraulic actuators operating at 3,000–5,000 PSI to handle large loads and provide robust performance in demanding environments.
- Aerospace and Defense: Hydraulic systems in aircraft and military equipment often operate at high pressures (up to 5,000 PSI) to ensure reliability and performance in critical applications.
- Automotive Systems: Hydraulic actuators in automotive applications, such as braking systems and power steering, usually operate at lower pressures (1,000–2,500 PSI) to balance performance and safety.
-
Importance of Pressure Ratings and Safety:
- Hydraulic actuators are designed with specific pressure ratings to ensure safe and efficient operation. Exceeding these ratings can lead to catastrophic failures, such as ruptured hoses, damaged seals, or actuator malfunctions.
- Safety features, such as pressure relief valves, are often integrated into hydraulic systems to prevent over-pressurization and protect the actuator and other components.
-
Selecting the Right Hydraulic Actuator:
- When choosing a hydraulic actuator, it is essential to consider the operating pressure requirements of the application. Factors such as load capacity, speed, and environmental conditions should also be evaluated.
- Consulting with manufacturers or suppliers can help ensure that the selected actuator meets the specific pressure and performance needs of the system.
By understanding the typical operating pressures and the factors that influence them, you can make informed decisions when selecting and using hydraulic actuators, ensuring optimal performance and longevity in your applications.
Summary Table:
Aspect | Details |
---|---|
Typical PSI Range | 1,000–5,000 PSI |
Low-Pressure Systems | 1,000–2,500 PSI (e.g., robotics, light-duty machinery) |
High-Pressure Systems | 2,500–5,000 PSI (e.g., construction, aerospace, heavy-duty applications) |
Key Factors | Actuator type, load requirements, system design, safety, and efficiency |
Applications | Industrial machinery, construction equipment, aerospace, automotive systems |
Need help selecting the right hydraulic actuator for your needs? Contact our experts today!