Heating steel during heat treatment is a critical process that requires precise control to achieve desired mechanical properties such as hardness, strength, toughness, and ductility. The heating process must consider factors like temperature, atmosphere, and cooling rates to avoid issues like surface decarburization, scaling, or intergranular oxidation. Proper heat treatment techniques, such as annealing, quenching, and tempering, can significantly enhance the performance and longevity of steel components. This answer explores the key considerations and methods for heating steel during heat treatment.
Key Points Explained:
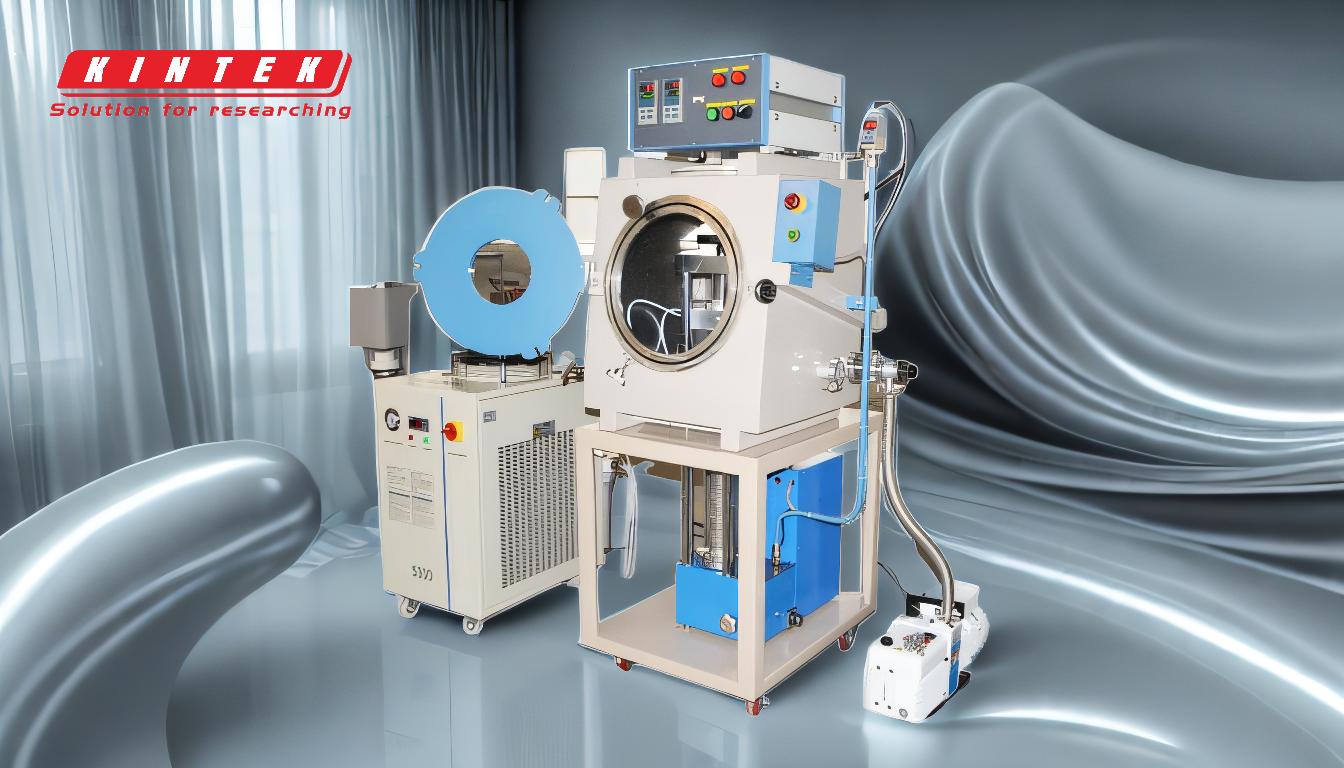
-
Temperature Control:
- The temperature at which steel is heated is crucial for achieving the desired microstructure and mechanical properties. Different heat treatment processes require specific temperature ranges:
- Annealing: Heated to a temperature above the upper critical temperature (typically 700–900°C) and then slowly cooled to soften the steel.
- Quenching: Heated to a high temperature (typically 800–950°C) and rapidly cooled to increase hardness.
- Tempering: Reheated to a lower temperature (150–650°C) after quenching to reduce brittleness and improve toughness.
- Exceeding or failing to reach the required temperature can lead to incomplete transformation of the microstructure, resulting in suboptimal properties.
- The temperature at which steel is heated is crucial for achieving the desired microstructure and mechanical properties. Different heat treatment processes require specific temperature ranges:
-
Atmosphere Control:
- The heating environment must be carefully controlled to prevent undesirable chemical reactions:
- Oxidation and Scaling: Oxygen in the atmosphere reacts with iron to form iron oxide (scale) and can cause intergranular oxidation. This is particularly problematic in carburized components.
- Decarburization: Oxygen and water vapor can react with carbon at the steel surface, reducing carbon content and weakening the material. Hydrogen, while reducing iron oxide, can also cause decarburization above 1300°F.
- Controlled atmospheres, such as inert gases (argon, nitrogen) or reducing gases (hydrogen), are often used to minimize these effects.
- The heating environment must be carefully controlled to prevent undesirable chemical reactions:
-
Cooling Rate:
- The rate at which steel is cooled after heating determines its final properties:
- Slow Cooling (Annealing): Produces a softer, more ductile material by allowing the formation of larger grains.
- Rapid Cooling (Quenching): Results in a harder, more brittle material by trapping carbon in a martensitic structure.
- Tempering: A controlled cooling process after quenching reduces brittleness while retaining hardness.
- Improper cooling rates can lead to residual stresses, cracking, or insufficient hardness.
- The rate at which steel is cooled after heating determines its final properties:
-
Common Heat Treatment Processes:
- Annealing: Used to soften steel, improve machinability, and relieve internal stresses. The steel is heated to a specific temperature and then slowly cooled.
- Case Hardening: Enhances surface hardness while maintaining a tough core. Techniques include carburizing, nitriding, and carbonitriding.
- Quenching and Tempering: Increases hardness and strength while maintaining toughness. The steel is rapidly cooled after heating and then tempered to reduce brittleness.
- Precipitation Hardening: Used for certain alloys to increase strength by forming fine precipitates within the microstructure.
-
Practical Considerations for Equipment and Consumables:
- Furnace Selection: Choose furnaces with precise temperature control and the ability to maintain a controlled atmosphere.
- Atmosphere Generators: Use equipment to produce inert or reducing atmospheres to prevent oxidation and decarburization.
- Cooling Systems: Implement systems for controlled cooling, such as oil or water quenching baths, to achieve desired cooling rates.
- Monitoring Tools: Use thermocouples, pyrometers, and gas analyzers to monitor temperature and atmosphere conditions during heat treatment.
-
Avoiding Common Pitfalls:
- Overheating: Can cause excessive grain growth, reducing strength and toughness.
- Insufficient Heating: May result in incomplete phase transformation, leading to inconsistent properties.
- Improper Atmosphere Control: Can cause scaling, decarburization, or contamination.
- Incorrect Cooling Rates: May lead to cracking, distortion, or inadequate hardness.
By carefully controlling temperature, atmosphere, and cooling rates, steel can be effectively heat-treated to achieve the desired mechanical properties. Proper equipment and consumables are essential to ensure consistent and high-quality results.
Summary Table:
Key Factor | Details |
---|---|
Temperature Control | - Annealing: 700–900°C, slow cooling - Quenching: 800–950°C, rapid cooling - Tempering: 150–650°C post-quenching |
Atmosphere Control | - Use inert gases (argon, nitrogen) or reducing gases (hydrogen) to prevent oxidation and decarburization |
Cooling Rate | - Slow cooling: Softens steel - Rapid cooling: Increases hardness - Tempering: Balances hardness and toughness |
Common Processes | - Annealing, case hardening, quenching & tempering, precipitation hardening |
Equipment | - Furnaces, atmosphere generators, cooling systems, monitoring tools |
Pitfalls to Avoid | - Overheating, insufficient heating, improper atmosphere, incorrect cooling |
Achieve superior steel heat treatment results—contact our experts today for tailored solutions!