Brazing stainless steel is a strong and reliable joining method when performed correctly. The strength of the brazed joint depends on several factors, including the materials used, the brazing process parameters, and the quality of the joint preparation. Stainless steel brazing typically results in joints with high mechanical strength, good corrosion resistance, and excellent thermal stability. However, achieving optimal strength requires careful control of factors such as heating rate, holding time, cooling rate, and the compatibility of the filler metal with the base material. Proper surface preparation and the removal of oxide layers are also critical to ensure a strong bond.
Key Points Explained:
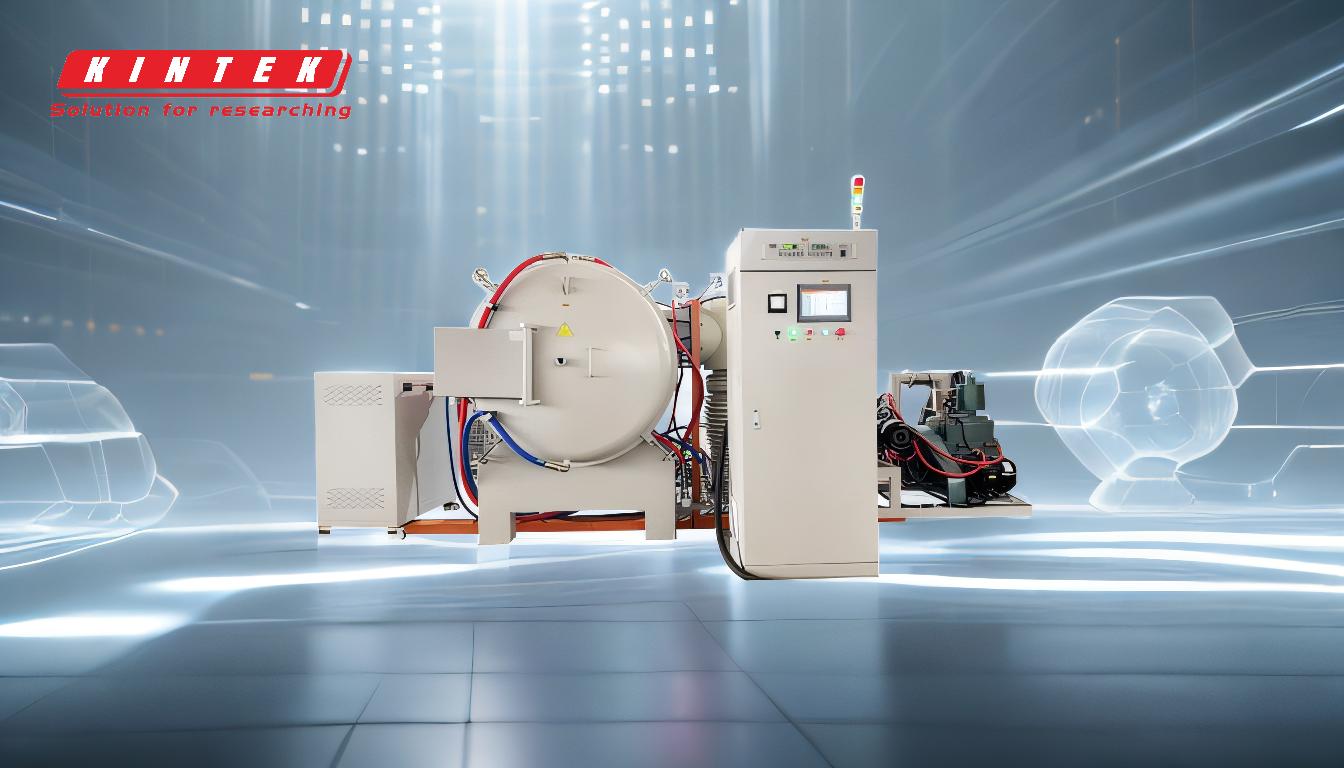
-
Factors Influencing Brazing Strength:
- The strength of brazed stainless steel joints is influenced by multiple factors, including:
- Material Compatibility: The filler metal must be compatible with the stainless steel base material to ensure proper wetting and bonding.
- Surface Preparation: Removing surface oxide films is critical for achieving a strong bond. Alkali cleaning or other surface treatments may be used.
- Process Parameters: Parameters such as heating rate, holding time, cooling rate, and vacuum level (in vacuum brazing) must be optimized for the specific application.
- The strength of brazed stainless steel joints is influenced by multiple factors, including:
-
Mechanical Strength of Brazed Joints:
- Brazed stainless steel joints can achieve high mechanical strength, often comparable to or exceeding the strength of the base material. The exact strength depends on:
- The type of stainless steel and filler metal used.
- The joint design and geometry.
- The quality of the brazing process, including proper temperature control and uniform heating.
- Brazed stainless steel joints can achieve high mechanical strength, often comparable to or exceeding the strength of the base material. The exact strength depends on:
-
Corrosion Resistance:
- Stainless steel is known for its corrosion resistance, and brazed joints can maintain this property if the filler metal and brazing process are chosen correctly. For example, using a filler metal with similar corrosion resistance to stainless steel ensures the joint performs well in harsh environments.
-
Thermal Stability:
- Brazed stainless steel joints exhibit excellent thermal stability, making them suitable for high-temperature applications. The filler metal must have a melting point lower than the base material but high enough to withstand the operating temperatures.
-
Process Optimization:
- Achieving the best results requires experimental screening to determine the optimal combination of process parameters. This includes:
- Selecting the appropriate brazing method (e.g., torch brazing, furnace brazing, or vacuum brazing).
- Adjusting the heating and cooling rates to minimize thermal stress.
- Ensuring proper joint clearance to allow capillary action for filler metal flow.
- Achieving the best results requires experimental screening to determine the optimal combination of process parameters. This includes:
-
Applications of Brazed Stainless Steel:
- Brazed stainless steel is widely used in industries such as aerospace, automotive, and chemical processing due to its strength, corrosion resistance, and thermal stability. Common applications include heat exchangers, piping systems, and structural components.
By carefully controlling these factors, brazing stainless steel can produce joints with exceptional strength, durability, and performance, making it a preferred joining method for many critical applications.
Summary Table:
Key Factors | Details |
---|---|
Material Compatibility | Filler metal must bond well with stainless steel for optimal strength. |
Surface Preparation | Oxide removal is critical for strong bonding; alkali cleaning is common. |
Process Parameters | Heating rate, holding time, cooling rate, and vacuum level must be optimized. |
Mechanical Strength | Joints can match or exceed base material strength with proper brazing. |
Corrosion Resistance | Filler metal choice ensures joints maintain stainless steel's corrosion resistance. |
Thermal Stability | Suitable for high-temperature applications with proper filler metal selection. |
Applications | Used in aerospace, automotive, and chemical processing industries. |
Need durable brazed stainless steel joints? Contact our experts today for tailored solutions!