Selective Laser Sintering (SLS) is a 3D printing technology that uses a laser to sinter powdered material into a solid structure. Its sustainability depends on several factors, including material usage, energy consumption, waste generation, and the lifecycle of printed products. SLS has the potential to be more sustainable than traditional manufacturing methods due to its ability to produce complex geometries with minimal material waste. However, challenges such as high energy consumption, limited recyclability of materials, and the use of non-renewable resources in some powders can impact its overall sustainability. Addressing these issues through advancements in material science, energy-efficient machinery, and recycling systems can enhance SLS's sustainability.
Key Points Explained:
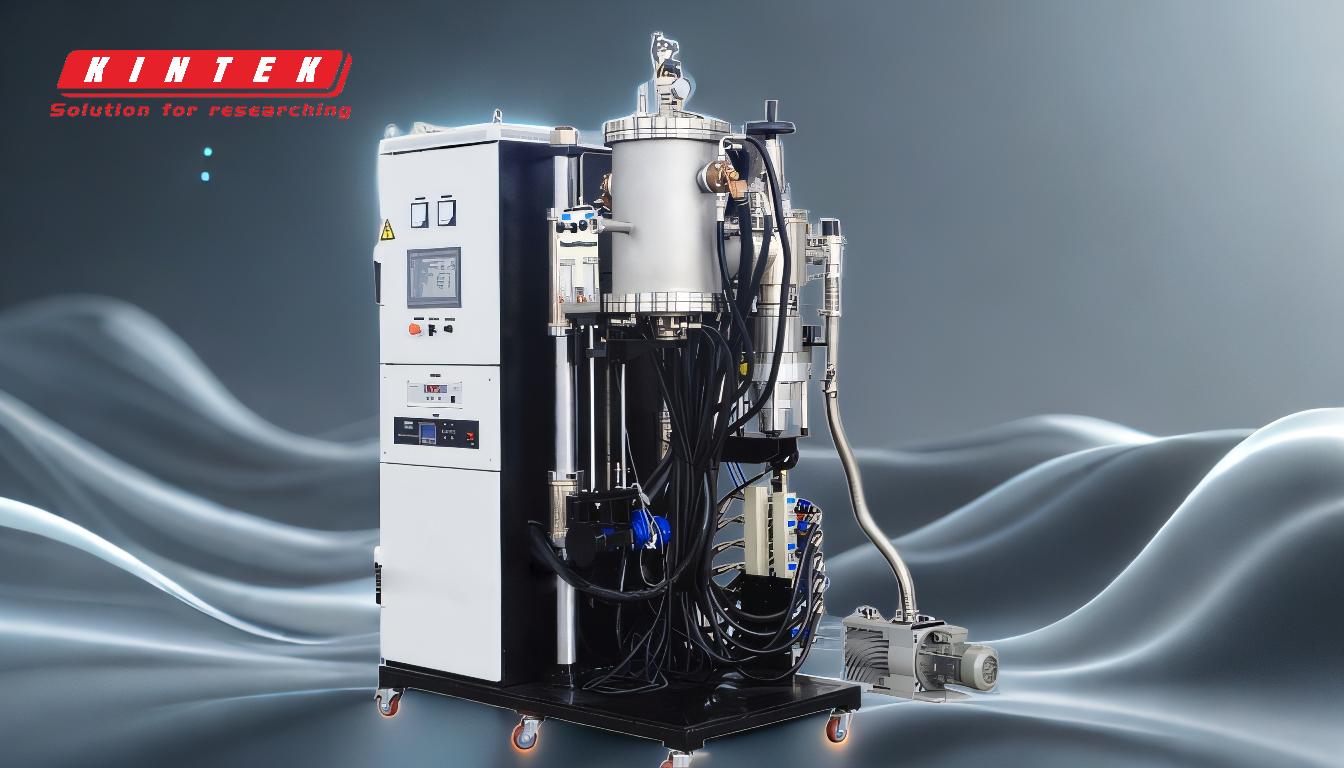
-
Material Efficiency and Waste Reduction:
- SLS is highly efficient in material usage because it only sinters the powder that is needed to create the part, leaving the rest of the powder in the build chamber for reuse.
- This contrasts with subtractive manufacturing methods, which often generate significant material waste.
- However, over time, the powder can degrade due to repeated heating and exposure to the laser, which may limit its recyclability and require disposal or recycling of used powder.
-
Energy Consumption:
- SLS machines require significant energy to operate, particularly for heating the build chamber and powering the laser.
- The energy intensity of SLS can be higher than traditional manufacturing methods, especially for small production runs.
- Advances in energy-efficient laser systems and optimized heating processes can help reduce the environmental impact of SLS.
-
Material Sustainability:
- Many SLS materials, such as nylon and polyamide, are derived from petrochemicals, which are non-renewable resources.
- Research is ongoing to develop bio-based and recyclable materials for SLS, which could improve its sustainability profile.
- The ability to use recycled powders or biodegradable materials would significantly enhance the environmental friendliness of SLS.
-
Lifecycle of Printed Products:
- SLS-produced parts are often used in industries where durability and performance are critical, such as aerospace and automotive.
- The long lifecycle of these parts can contribute to sustainability by reducing the need for frequent replacements.
- However, the end-of-life disposal of SLS parts can be challenging if the materials are not recyclable or biodegradable.
-
Waste Management:
- While SLS generates less waste during the manufacturing process compared to traditional methods, the disposal of unused or degraded powder remains a concern.
- Proper waste management practices, such as recycling or repurposing used powder, are essential to minimize the environmental impact.
- Some companies are exploring ways to recycle SLS powder into new feedstock or other applications.
-
Advancements in Technology:
- Innovations in SLS technology, such as lower-temperature sintering and more efficient lasers, are helping to reduce energy consumption and improve sustainability.
- The development of closed-loop systems for powder handling and recycling can further enhance the environmental performance of SLS.
- Collaboration between manufacturers, researchers, and policymakers is crucial to driving these advancements and making SLS a more sustainable option.
-
Comparison with Other Manufacturing Methods:
- SLS is generally more sustainable than traditional subtractive methods due to its additive nature and reduced material waste.
- However, it may not always be the most sustainable option compared to other additive manufacturing methods, such as Fused Deposition Modeling (FDM), which can use biodegradable materials like PLA.
- The choice of manufacturing method should consider the specific requirements of the application, including material properties, production volume, and environmental impact.
-
Potential for Circular Economy:
- SLS has the potential to contribute to a circular economy by enabling on-demand production and reducing the need for large inventories.
- The ability to reuse powder and recycle parts can further support circular economy principles.
- However, achieving a fully circular system for SLS requires significant advancements in material science, recycling infrastructure, and supply chain management.
In conclusion, while SLS offers several sustainability advantages, such as material efficiency and the ability to produce durable parts, challenges related to energy consumption, material sourcing, and waste management need to be addressed. Continued innovation and a focus on sustainable practices can help make SLS a more environmentally friendly manufacturing option.
Summary Table:
Aspect | Key Insights |
---|---|
Material Efficiency | SLS minimizes waste by reusing unsintered powder, but powder degradation is a concern. |
Energy Consumption | High energy use for heating and lasers, but advancements aim to reduce energy intensity. |
Material Sustainability | Many SLS materials are non-renewable, but bio-based and recyclable options are emerging. |
Lifecycle of Products | Durable parts reduce replacement needs, but end-of-life disposal can be challenging. |
Waste Management | Less waste during production, but proper recycling of degraded powder is essential. |
Advancements | Innovations like lower-temperature sintering and closed-loop systems improve sustainability. |
Comparison to Other Methods | SLS is more sustainable than subtractive methods but may lag behind FDM in some cases. |
Circular Economy Potential | SLS supports on-demand production and powder reuse, but full circularity requires further innovation. |
Learn how SLS can enhance your manufacturing sustainability—contact our experts today!