Sputter coating in scanning electron microscopy (SEM) involves applying an ultra-thin layer of conductive material to non-conductive or poorly conductive specimens to enhance imaging quality. The typical thickness of sputter coatings ranges from 2 to 20 nanometers, with 10 nanometers being a common target. This process prevents specimen charging, improves secondary electron emission, and enhances the signal-to-noise ratio. The choice of coating material, such as gold, gold/palladium, platinum, or iridium, depends on factors like the sample's nature, imaging goals, and the need for energy-dispersive X-ray spectroscopy (EDS) analysis. Sputter coating also reduces beam damage, improves thermal conduction, and protects beam-sensitive specimens.
Key Points Explained:
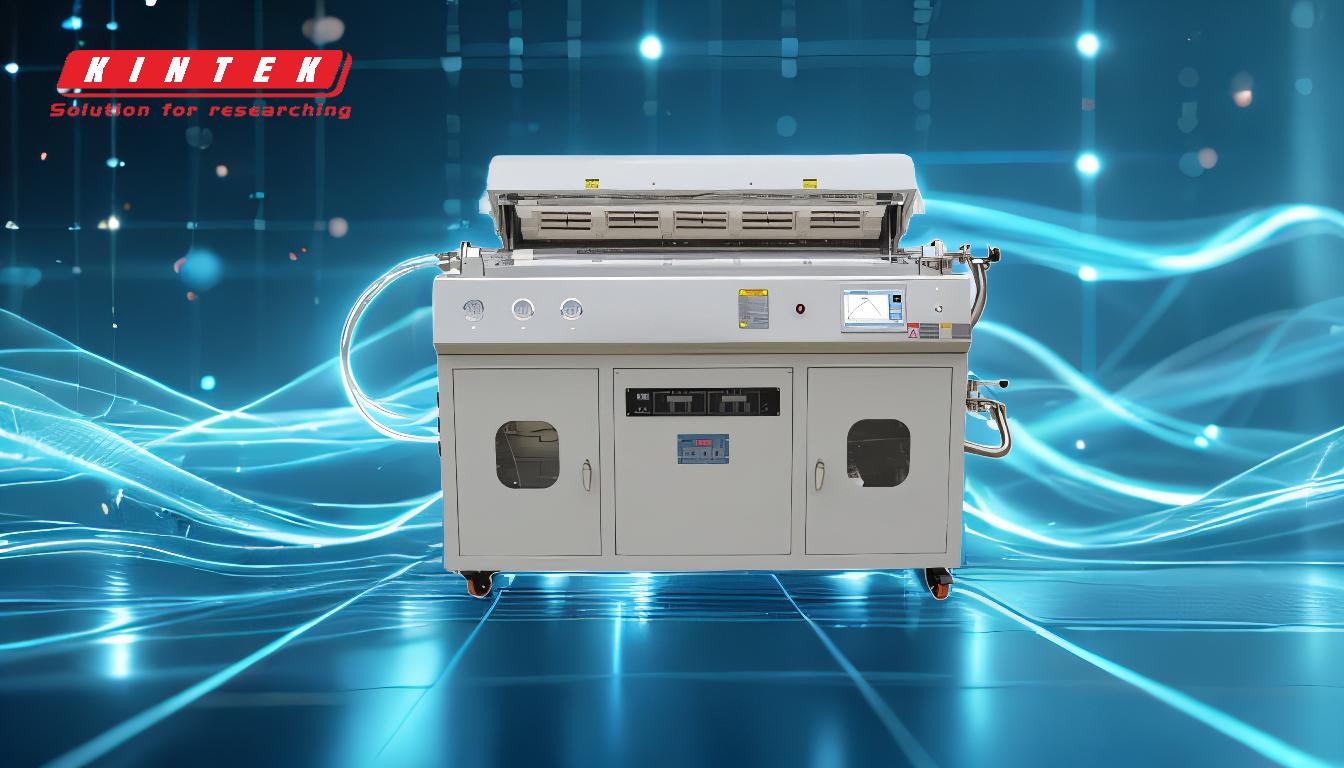
-
Purpose of Sputter Coating in SEM:
- Sputter coating is used to apply a thin conductive layer to non-conductive or poorly conductive samples. This prevents charging during SEM imaging, enhances secondary electron emission, and improves the signal-to-noise ratio, leading to clearer and more detailed images.
-
Typical Thickness of Sputter Coatings:
- The thickness of sputter coatings typically ranges from 2 to 20 nanometers, with 10 nanometers being a common target. This ultra-thin layer is sufficient to provide conductivity without obscuring fine sample details.
-
Coating Materials:
- Common materials used for sputter coating include gold, gold/palladium, platinum, silver, chromium, and iridium. The choice of material depends on factors such as:
- The sample's sensitivity to vacuum.
- The need for sample storage.
- The size of features of interest.
- The imaging goal (e.g., composition study or EDS analysis).
- Common materials used for sputter coating include gold, gold/palladium, platinum, silver, chromium, and iridium. The choice of material depends on factors such as:
-
Factors Influencing Coating Material Selection:
- Grain Size: Smaller grain sizes provide better resolution.
- Secondary Electron Yield: Higher yields improve image quality.
- Thermal Conductivity: Helps dissipate heat from the electron beam.
- Chemical Stability: Ensures the coating does not react with the sample.
- Ease of Removal: Important if the coating needs to be removed after analysis.
- EDS Compatibility: The coating material should not overlap with the sample's elemental peaks in EDS analysis.
-
Benefits of Sputter Coating:
- Reduced Beam Damage: Protects beam-sensitive specimens from damage.
- Improved Thermal Conduction: Dissipates heat generated by the electron beam.
- Reduced Sample Charging: Prevents artifacts caused by charge buildup.
- Enhanced Secondary Electron Emission: Improves image clarity and detail.
- Improved Edge Resolution: Reduces beam penetration, enhancing edge definition.
- Protection of Beam-Sensitive Specimens: Shields delicate samples from beam-induced damage.
-
Application and Process:
- Sputter coating is achieved using a sputtering system, where a target material is bombarded with ions, causing atoms to be ejected and deposited onto the sample. The process parameters, such as power, pressure, and time, are carefully controlled to achieve the desired coating thickness and quality.
-
Historical Context and Broader Applications:
- Sputtering has been used since the early 1800s for various applications, including reflective coatings for mirrors, packaging materials, and advanced semiconductor devices. Its maturity and versatility make it a reliable technique for SEM sample preparation.
By understanding these key points, an equipment or consumable purchaser can make informed decisions about sputter coating materials and processes to achieve optimal SEM imaging results.
Summary Table:
Aspect | Details |
---|---|
Typical Thickness | 2 to 20 nanometers (10 nm is common) |
Purpose | Prevents charging, improves secondary electron emission, enhances SNR |
Common Materials | Gold, gold/palladium, platinum, silver, chromium, iridium |
Key Benefits | Reduces beam damage, improves thermal conduction, protects sensitive samples |
Factors Influencing Material | Grain size, secondary electron yield, EDS compatibility, chemical stability |
Optimize your SEM imaging with the right sputter coating—contact our experts today for tailored solutions!