Maintaining a muffle furnace is crucial for ensuring its longevity, accuracy, and consistent performance. Proper maintenance involves regular cleaning, inspection of electrical components, and adherence to operational guidelines. Key practices include baking the furnace after long periods of inactivity, keeping the furnace chamber clean, checking wiring and thermocouples, and ensuring the furnace operates in a suitable environment. Regular maintenance not only prevents damage but also ensures the furnace operates efficiently and safely.
Key Points Explained:
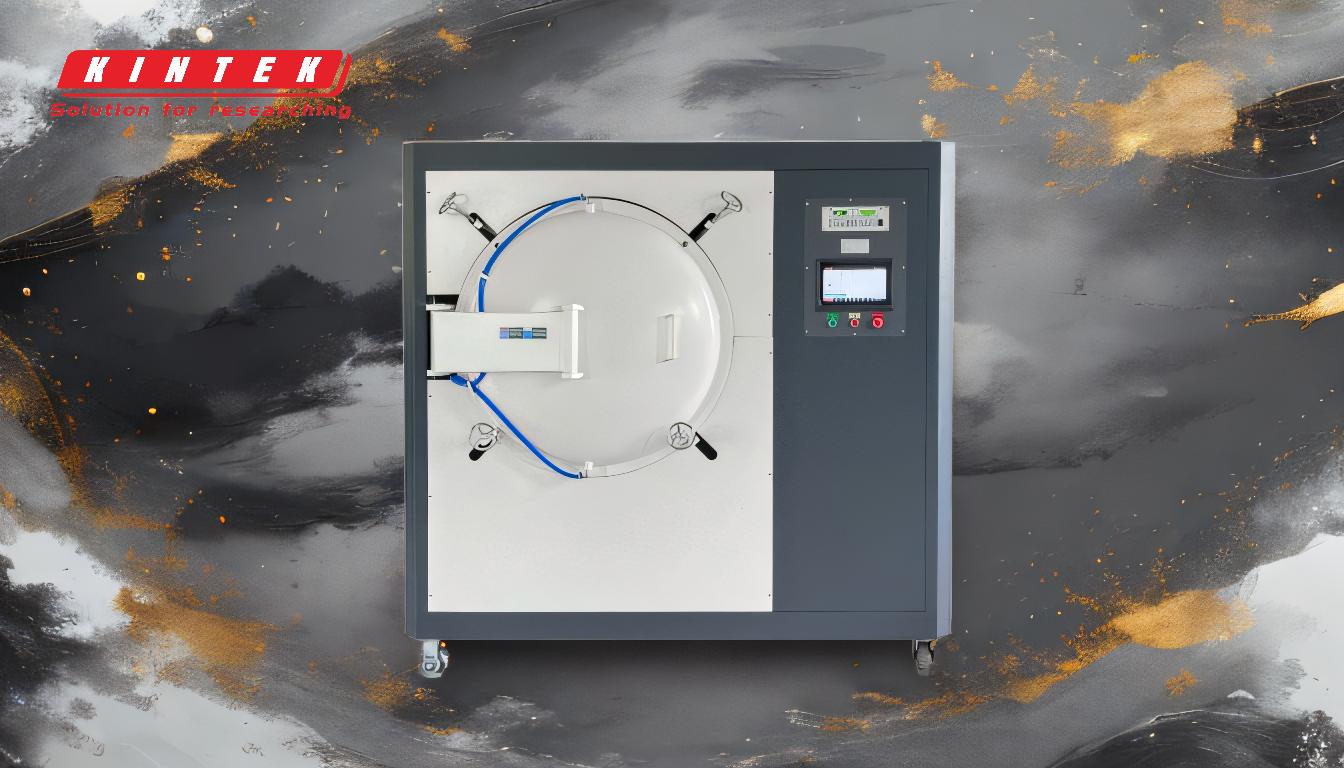
-
Initial Baking After Inactivity:
- When a muffle furnace is used for the first time or after a long period of inactivity, it must be baked. This involves heating the furnace to a temperature between 200℃ and 600℃ for four hours. This process helps to remove any moisture that may have accumulated and ensures the furnace is ready for high-temperature operations.
- Why it’s important: Baking prevents potential damage to the heating elements and ensures the furnace operates efficiently.
-
Environmental Conditions:
- The muffle furnace and its controller should be placed in an environment where the relative humidity does not exceed 85%. The area should be free from conductive dust, explosive gases, and corrosive gases.
- Why it’s important: High humidity and corrosive environments can damage the furnace’s electrical components and reduce its lifespan.
-
Regular Cleaning of the Furnace Chamber:
- Regular cleaning of slag, debris, and oxides from the furnace chamber is necessary to maintain cleanliness and prevent contamination.
- Why it’s important: A clean furnace chamber ensures accurate and consistent results, prevents damage to the furnace lining, and extends the furnace’s lifespan.
-
Inspection and Maintenance of Electrical Components:
- Regularly check the wiring of the electric furnace and controller to ensure it is in good condition. Verify that the indicator pointer moves freely without sticking.
- Why it’s important: Proper wiring and functioning indicators are crucial for safe and accurate operation. Faulty wiring can lead to electrical hazards or inaccurate temperature readings.
-
Thermocouple Maintenance:
- Ensure the metal protection tube of the thermocouple is well grounded. If necessary, use a three-wire output thermocouple to reduce interference.
- Why it’s important: Proper grounding and reduced interference ensure accurate temperature measurements, which are critical for consistent results.
-
Avoid Overheating and Contamination:
- Do not exceed the rated temperature of the furnace to avoid damaging the heating elements. Avoid filling the furnace with liquids or easily dissolved metals.
- Why it’s important: Overheating can damage the furnace, and contaminants can cause corrosion or other damage to the furnace chamber.
-
Handling Alkaline Substances:
- When using alkaline substances, pre-place a refractory plate at the bottom of the furnace to prevent corrosion.
- Why it’s important: Alkaline substances can corrode the furnace lining, and a refractory plate protects the furnace from damage.
-
Routine Maintenance and Component Replacement:
- Perform routine maintenance, such as replacing damaged or worn-out components, to extend the furnace’s lifespan and ensure accurate results.
- Why it’s important: Regular maintenance prevents unexpected breakdowns and ensures the furnace operates efficiently.
By following these maintenance practices, you can ensure that your muffle furnace operates safely, efficiently, and accurately, providing consistent results over its lifespan.
Summary Table:
Maintenance Practice | Importance |
---|---|
Initial Baking After Inactivity | Removes moisture, prevents damage to heating elements, and ensures efficiency. |
Optimal Environmental Conditions | Protects electrical components and extends furnace lifespan. |
Regular Cleaning of the Furnace Chamber | Prevents contamination, ensures accuracy, and extends lifespan. |
Inspection of Electrical Components | Ensures safe operation and accurate temperature readings. |
Thermocouple Maintenance | Provides accurate temperature measurements for consistent results. |
Avoid Overheating and Contamination | Prevents damage to heating elements and furnace chamber. |
Handling Alkaline Substances | Protects furnace lining from corrosion. |
Routine Maintenance and Replacement | Prevents breakdowns and ensures efficient operation. |
Ensure your muffle furnace operates at peak performance—contact our experts today for personalized maintenance advice!