Brazing is a metal-joining process that involves melting a filler metal to bond two or more metal pieces together. Its environmental friendliness depends on several factors, including the materials used, the energy source, and the waste management practices. While brazing can be more energy-efficient than welding and produces fewer emissions, the use of fluxes and filler metals containing hazardous materials can pose environmental risks. Proper handling, recycling, and disposal of materials, as well as the use of eco-friendly fluxes and filler metals, can significantly improve the sustainability of brazing processes. Overall, brazing can be environmentally friendly if best practices are followed.
Key Points Explained:
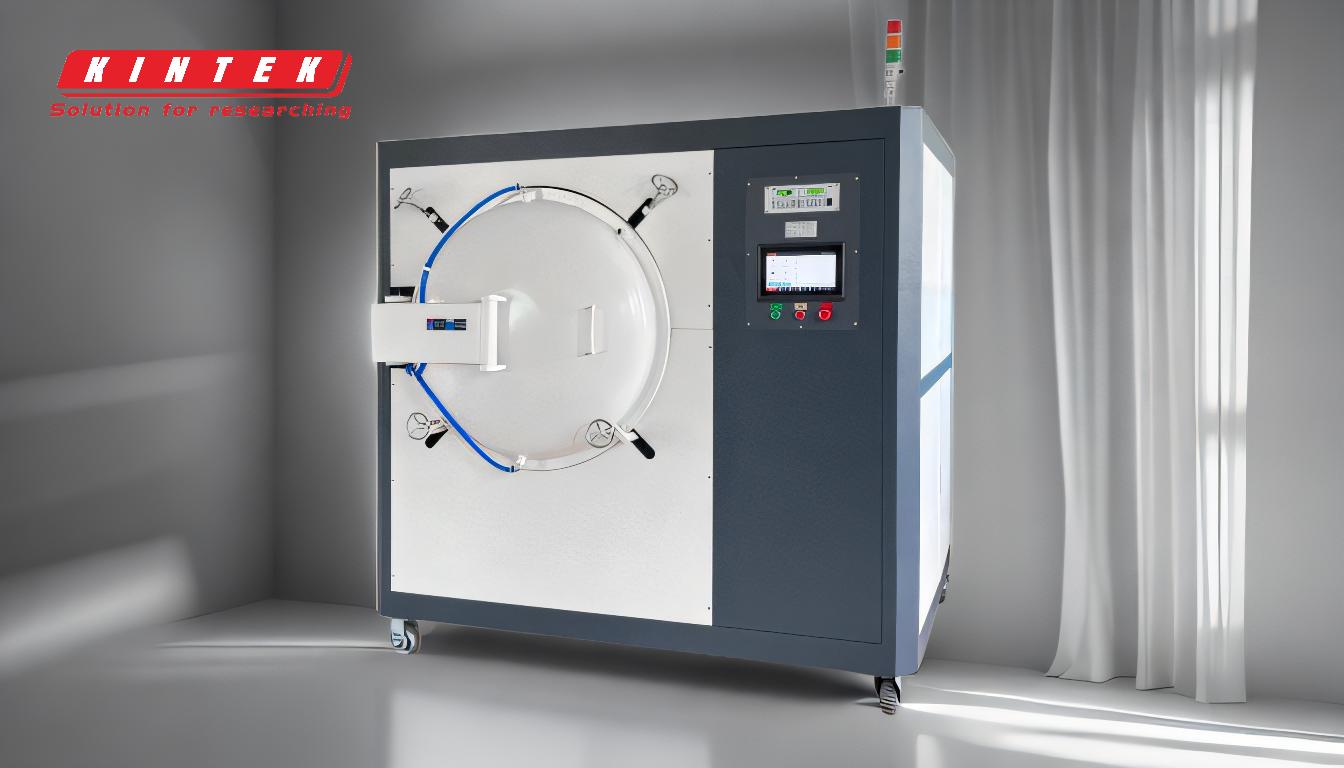
-
Energy Efficiency and Emissions:
- Brazing typically requires lower temperatures compared to welding, which reduces energy consumption and associated greenhouse gas emissions.
- The process can be optimized further by using energy-efficient equipment and renewable energy sources.
-
Materials Used in Brazing:
- Filler Metals: The choice of filler metal can impact environmental friendliness. Some filler metals contain hazardous materials like cadmium or lead, which can be harmful if not properly managed. However, many modern filler metals are designed to be eco-friendly.
- Fluxes: Fluxes are used to prevent oxidation and improve the flow of the filler metal. Traditional fluxes can contain harmful chemicals, but there are now environmentally friendly alternatives available, such as water-based or no-clean fluxes.
-
Waste Management:
- Proper disposal and recycling of waste materials, such as used fluxes and filler metal residues, are crucial for minimizing environmental impact.
- Implementing closed-loop recycling systems can help recover valuable materials and reduce waste.
-
Health and Safety Considerations:
- The use of hazardous materials in brazing can pose risks to workers' health and the environment. Ensuring proper ventilation, protective equipment, and training can mitigate these risks.
- Adopting safer materials and processes can further enhance the environmental and health benefits of brazing.
-
Regulatory Compliance:
- Adhering to environmental regulations and standards, such as RoHS (Restriction of Hazardous Substances) and REACH (Registration, Evaluation, Authorisation, and Restriction of Chemicals), can help ensure that brazing processes are environmentally friendly.
- Compliance with these regulations often drives the adoption of safer materials and practices.
-
Innovations and Best Practices:
- Continuous innovation in brazing technology, such as the development of new filler metals and fluxes, can improve the environmental performance of the process.
- Best practices, such as optimizing process parameters, using renewable energy, and implementing waste reduction strategies, can further enhance sustainability.
By considering these factors and adopting best practices, brazing can be made more environmentally friendly, contributing to sustainable manufacturing processes.
Summary Table:
Factor | Impact on Environmental Friendliness |
---|---|
Energy Efficiency | Lower temperatures reduce energy use and emissions. Renewable energy further optimizes the process. |
Materials | Eco-friendly filler metals and fluxes minimize environmental risks. |
Waste Management | Proper recycling and disposal reduce waste. Closed-loop systems recover valuable materials. |
Health & Safety | Safer materials and practices protect workers and the environment. |
Regulatory Compliance | Adherence to RoHS and REACH standards ensures environmentally friendly processes. |
Innovations & Best Practices | Continuous improvements and optimized processes enhance sustainability. |
Ready to make your brazing process more sustainable? Contact us today for expert guidance and eco-friendly solutions!